From Furnace To Your Front Door: A Morning in Heat Treatment
Heat treatment impacts almost every facet of our lives, yet few people are aware of how important this practice is to a modern way of living. Heat treatment is a process which changes the microstructure of a metal, such as hardening, carburizing, tempering, and many others.
When a metal is formed, it undergoes heat treatment in order to make it longer lasting, change its structure so that it becomes harder or softer, or reduce the tendancy toward cracking which can form during manufacturing. To help us appreciate the impact of heat treatment on our daily lives, Tiffany Ward, daily editor for Heat Treat Today, has prepared this illustrative post.
Breakfast of Champions
You wake up in the morning and roll yourself out of bed, greeting a foggy sunrise through the window. You stumble to the kitchen to fire up your cast iron skillet.
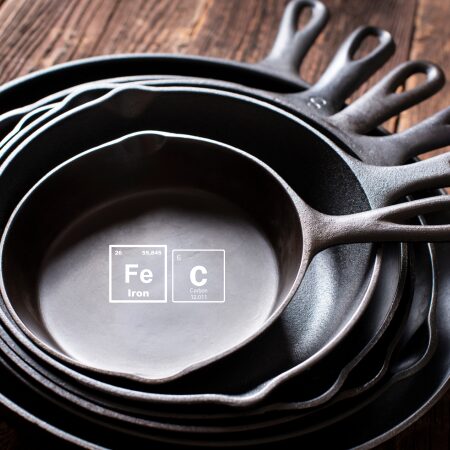
At one time, that same cast iron skillet lived a provincial life, known as simply: iron. Cast iron is made from iron with greater than 2% carbon, which is in the form of graphite. When that iron was “cast,” it was melted at a high temperature, and once cooled, it transformed into a very stable material that heats and cools uniformly. Perfect for your sunny-side-up eggs.
At the foundry, someone poured the molten metal into a mold to form the exact shape your pan is in today, and then it underwent numerous heat treat processes: annealing, normalizing, tempering, and even graphitizing (a process of converting carbon into graphite). The particular processes the skillet underwent depend upon the chemistry of the cast iron.
Almost all cast iron has carbon and nitrogen added to its surface in a process called ferritic nitrocarburizing plus post-oxidation. This heat treatment gives a shallow surface layer to the pan for better wear resistance. The skillet is heated up between around 1550°F and 1650°F inside a protective atmosphere of Endothermic gas. Endothermic gas is a generated heat treat atmosphere. It is made up of approximately 40% hydrogen, 40% nitrogen, and 20% carbon monoxide. The Endothermic gas is enriched with both a hydrocarbon gas (i.e., natural gas or propane) and ammonia so that carbon and nitrogen can be added to the iron.
There are a variety of different furnaces that can be used for ferritic nitrocarburizing. Box, pit, and tip-up furnaces are used due to their large capacity. For cast iron skillets, one common choice is the pit furnace — a cylindrical furnace typically located in the floor of a factory. Pit furnaces can hold a lot of heavyweight items, making them a good fit for the cookware now resting on your stove.
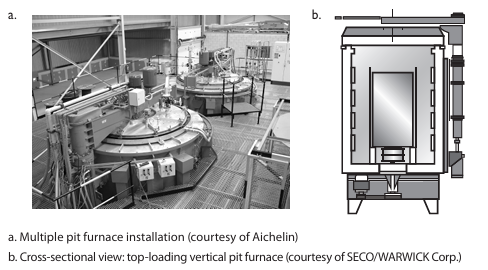
Technical Resource: An Overview of Case Hardening: Which Is Best for Your Operations?
Technical Resource: Nitriding and Nitrocarburizing: The Benefits for Surface Treatment
It Cuts Like a Knife
You pull a knife out of your drawer and begin slicing an apple. The blade reflects a beam of sun from the window, but it isn’t your best knife. You’ve noticed that some of your knives are sharper and can resharpen more easily than others; this is because of the quality of the original material used and the heat treatment process employed in manufacturing the knife.
Perhaps the knife you chose to use today was made from high carbon steel such as 1095. The blade was heat treated using a process of hardening, quenching, and tempering. After the blade was formed, it entered a continuous mesh-belt furnace and was quenched in either oil (in the case of a 1095 steel), or in the case of stainless steel or tool steel, cooled in still air.
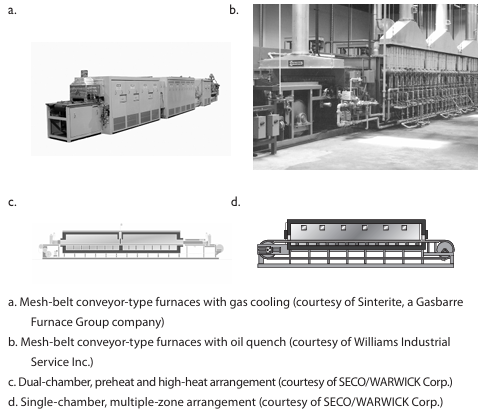
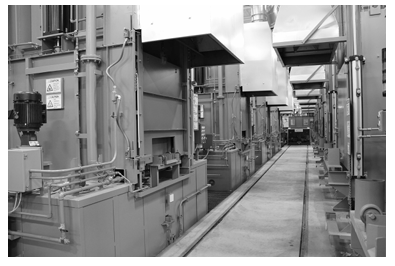
At the same time of hardening and quenching, the handle was joined to the blade in a process called brazing. The entire knife was heated up to an austenitizing temperature and rapidly cooled in the quenching process, giving it a particular hardness level.
The hardening process can be performed in a vacuum furnace or an atmosphere furnace. The atmosphere is typically nitrogen or, more commonly, a nitrogen/hydrogen mixture. Another option is nitrogen plus dissociated ammonia (dissociated ammonia is 75% hydrogen, 25% nitrogen).
A typical temperature for the heat treatment of high carbon 1095 steel knives is 1475ºF. Stainless steels are run at higher temperatures, typically in the range of 1800º/1950ºF and tool steels even higher, to around 2200ºF.
Technical resources: Ask the Heat Treat Doctor®: How Does One Determine Which Quench Medium To Use?
Technical Resource: Heat Treat Radio #105: Lunch and Learn: Batch IQ Vs. Continuous Pusher, Part 2
Time to Look Pretty
After breakfast you head to the bathroom. You are anxious to rid yourself of unshaven scruff, carefully running a razor over your face. The razor blades were hardened and tempered for sharpness, so that you get a smooth, clean shave.
Like knives, razor blades are hardened and are made of a medium to high carbon steel. Unlike knives, they are hardened in a continuous strip form. Envision all of your razor blades as a single, thin strip, run continuously through a furnace to heat and cool them. The blade is heated in a protective atmosphere as it runs through the furnace. On one end of the furnace is a reel that coils the strip and at the other end is an un-coiler.
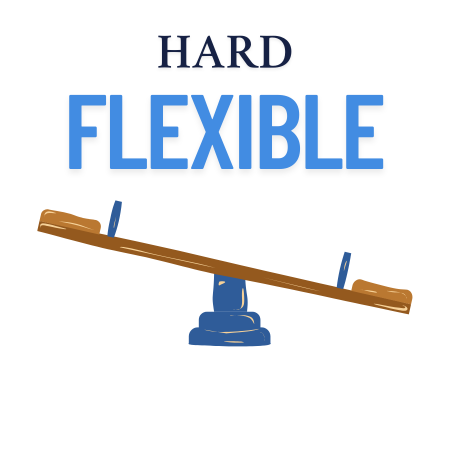
Continuous style furnaces have alloy tubes inside of them that are very small in diameter, typically one inch, which run the entire length of the furnace. As the razor strip is run through the tube it is exposed to an atmosphere of nitrogen and hydrogen, typically with 3% hydrogen, to protect the razor blade surface from oxidation. Once heated, the blade enters cooling either by surrounding the tube with water or by blowing forced air on the tubes.
A process called tempering follows hardening and quenching. When you harden a material you make it stronger, but less ductile, so there is a concern that the razor blade might break. The tempering process improves ductility, removing some of the hardness but improving flexibility.
Dan Herring, The Heat Treat Doctor®, describes the balancing act this way: “On one end of the teeter totter, metallurgically, are strength properties and on the other side of the teeter-totter are ductility properties. It’s always a challenge to properly balance the teeter-totter. If you get the hardness too high, what happens to the ductility? It’s very low. As a result, the material is super hard but may crack easier. On the other hand, if ductility is too high, the material is super flexible so that it can bend like a branch of a tree in the wind, but it has little strength. You need a balance of strength and ductility in all heat treated products, which is accomplished in part by proper tempering.”
Technical Resources: Tempering: 4 Perspectives — Which makes sense for you?
Technical Resources: Ask The Heat Treat Doctor®: What Are the Differences Between Intergranular Oxidation (IGO) and Intergranular Attack (IGA)?
Wake Up and Smell The Heat treatment
Our lives are touched by heat treatment at every turn. Highly technical processes play their role in the formation of even the most common household items. While heat treatment may seem to some a niche industry, its impact on everyday life is ubiquitous.
A special note of thanks to Dan Herring, The Heat Treat Doctor®, for his insights and contributions which informed this post.
Find heat treating products and services when you search on Heat Treat Buyers Guide.Com
From Furnace To Your Front Door: A Morning in Heat Treatment Read More »