Hot isostatic pressing (HIP) has been a player in heat treating for 50 years, but recent advances in its technology are providing cutting edge opportunities for new applications in the thermal processing industry.
Heat Treat Today asked two experts in the HIPing world about the state of hot isostatic pressing: What are the latest technologies and where are its potential growth markets in the thermal processing industry? They represent both sides of HIPing – one from a HIP equipment manufacturer and the other from a HIP process/service provider. Each gives a unique perspective on the HIP market and the industry itself.
Our expert contributors are Chad Beamer, an applications engineer in Hot Isostatic Pressing, at Quintus Technologies, a high pressure technology company, and Derek Denlinger, a corporate lead metallurgist at Paulo, a thermal processes and metal finishing operations company. This Original Content Technical Tuesday article was taken from 2020 Q4 Heat Treat Today print magazine.
What is HIP?

Corporate Lead Metallurgist
Paulo
Paulo’s Derek Denlinger says, “Hot isostatic pressing is fundamentally, when parts simultaneously see high temperature (in some cases as much as 2500oF) and very high pressure (up to 30,000psi) from all directions for a duration of time.”

Applications Engineer – Hot and Cold Isostatic Pressing
Quintus Technologies LLC
Chad Beamer of Quintus adds, “Pressure-based compaction processes can be used to establish density by applying a uniaxial pressure within rigid dies. Such mechanical or hydraulic approaches can produce non-complex parts or ‘green’ compacts. Although a cost-effective and high-throughput technique, these conventional presses exhibit geometrical limitations and compressibility constraints, yielding product that is not uniform in density and microstructure.”
“Isostatic pressing was developed with the desire to improve upon these shortcomings,” continues Beamer. “Such compaction techniques leverage Pascal’s law by using a fluid contained in a pressure vessel, either in the liquid or gas state, to transmit equal pressure in all directions on the surface of a workpiece.”
Beamer further explains, “Various isostatic pressing techniques exist today such as cold isostatic pressing (CIP), warm isostatic pressing (WIP), and hot isostatic pressing (HIP). HIP is a heat treatment process that utilizes isostatic pressure via a gas at high temperatures. It is commonly used to consolidate metal or ceramic powder and to reduce defects present in castings and additively manufactured parts. The output is a product with improved mechanical properties, workability, and reliability.”

What happens in the HIPing process?
Denlinger explains, “In the HIPing process, parts are heated to a temperature high enough to weaken material strength. High pressure, usually applied through a pressurized gas medium such as argon, applies a compressive stress onto the part from every direction. Given a hold period of time, this compression effectively allows for internal voids or pores to close up due to a mixture of mechanical deformation, creep, and metallic diffusion. The part consolidation sets the stage for any other heat treatment that may follow in order to maximize material performance.”
Since the densification of the workpiece is achieved by the simultaneous application of pressure and elevated temperature during HIP, Beamer adds, “Temperatures are usually in the range of 900oF-3600oF (500o-2000oC) depending on the material being HIPed. A good rule of thumb is a temperature targeting approximately 80% of the materials solidus temperature. Pressures in the vessel can reach twice that of the pressure at the bottom of the Mariana Trench, generally in the range of 15,000-30,000 psi (100-200MPa). The combined temperature and pressure applied should be capable of exceeding the yield strength of the material.”
Latest HIP Technologies
Both Beamer and Denlinger share optimism about the new HIP advancements, especially the new high pressure heat treatment (HPHT).
Beamer states, “A recent development in HIP technology is the ability to perform rapid gas cooling and quenching in the HIP system. Originally developed to shorten cycle time, this advancement is now being leveraged to perform many of the standard heat treatments for metals in the HIP furnace. Now a single piece of equipment can be used to apply both HIP and heat treatment, all carried out in one cycle. This approach is referred to as high pressure heat treatment (HPHT). Benefits to this new treatment include:
- the ability to remove an additional process step and piece(s) of equipment
- more cost-effective manufacturing path
- fewer times a component must be heated up
- less time spent at elevated temperature
- elimination of the risk of thermally induced porosity (blistering) in additively manufactured parts
“These modern systems are continuing to evolve with other promising advancements such as steered cooling. This controlled cooling approach within a HIP vessel allows cooling rates for a component to be optimized in order to achieve the desired microstructure. These advancements are quite exciting for many industries as they are expanding the design windows for material systems and creating new opportunities within a HIP system.”
“HIP has been around commercially for around 50 years,” Denlinger points out, “but more recent technology has been focused on better control of thermal aspects of the process. This is opening the doors for more fine-tuned ‘high pressure heat treatment’ processing that can offer speed and, in some cases, performance benefits that were previously not possible. These types of processes have often been coupled with the ever-growing additive manufacturing processes, though applications to more traditional manufacturing methods are gaining momentum. The influence of pressure on diffusion and transformation in materials has been identified, but not fully explored for many alloys, so new high pressure heat treatments are now being considered to compete with traditional HIP and heat treatment methods.”
What is HIP’s niche in the thermal processing industry? Who are its customers? Where do you see potential growth markets?
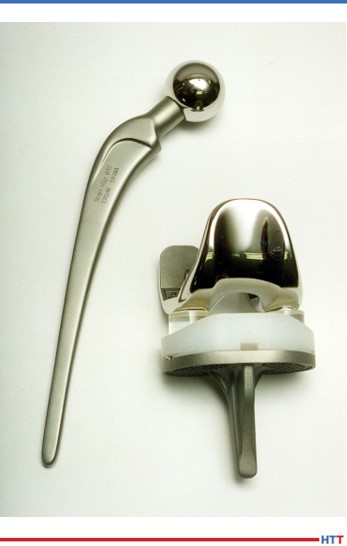
According to both men, the future is bright for HIPing.
Beamer explains why specific industries choose HIPing: “HIP is often desired where the risk of failure is not an option. Therefore, it is not surprising that HIP is commonplace in aerospace, energy, and medical industries. Applications within these industries include densification of products, consolidation of powder, diffusion bonding, as well as HPHT. For the aerospace industry, HIP is used to remove porosity from nickel-base and titanium-base castings as well as defects present in additively manufactured parts. The medical industry applies HIP to improve the quality and durability for cobalt chrome and titanium implants. HIPing of large and complex near-net-shape powder metal components to achieve fully densification is routine in the energy industry.”
Denlinger agrees, “HIP has most often been used for fatigue benefits, which is an important performance criterion in the aerospace industry. This remains in the scope, but applications in other sectors are growing due to the adoption of additive manufacturing. Oil and gas, medical, manufacturing equipment, space, firearms, and other industries are increasing their use of HIP and high-pressure heat treatment. Partnering with companies to explore additive manufacturing solutions with both HIP and traditional heat treatment in our arsenal has been very successful; challenging the status quo with the latest HIP technology and our expertise in heat treatment has been a great learning experience.
Regarding market expansion for HIP, Beamer shares, “Potential growth markets for HIP include medical, defense, space, automotive and the ongoing developments with additively manufactured applications. The medical industry is showing growth with an aging population coupled with a cultural shift to living a more active lifestyle. Another trend within the medical industry is to insource HIP versus going through a supplier, which can offer process optimization opportunities and increased quality control.”
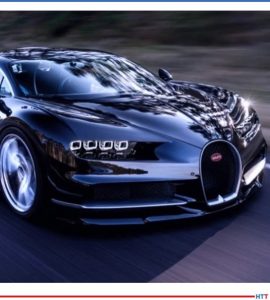
Beamer continues, “Growth for HIP in the defense industry can be attributed to strong government funding, such as the development work being done through America Makes. One of the most exciting growth markets here in the US is space, in which many high-profile companies are showing interest in HIP and HPHT technologies.
“Although the HIP process is not typically characterized as a high-volume process,” Beamer concludes, “the automotive industry is finding its benefits useful for cast engine blocks and emerging technology such as binder jet applications. Despite the present challenges due to the Covid-19 pandemic, specifically within the civil aerospace industry, there are many exciting growth opportunities for HIP.”
(All photos in this article provided by Quintus Technologies)
About the Authors:
Chad Beamer has a MS from the Ohio State University in Material Science and has worked as a material application engineer with GE Aviation for 7 years and as a technical services manager with Bodycote for 5 years. In February, Chad began working with Quintus Technologies as an application engineer for the Advanced Material Densification division focusing on hot isostatic pressing (HIP). As an applications engineer, he manages the HIP Application Center located in Columbus, Ohio, educates on the advancements of HIP technologies, and is involved in collaborative development efforts both within academia and industry.
For more information, contact Chad at chad.beamer@quintusteam.com or 614-404-3982
Derek Denlinger is the corporate lead metallurgist at Paulo. Derek has a Bachelor of Science in Metallurgical Engineering from Missouri S&T in Rolla. He started in the foundry industry before transitioning to heat treatment at Paulo where he has been for the past 5 years. The past two years, Derek has been focused on additive manufacturing and hot isostatic pressing assisting with Paulo’s entry into the HIP market.
For more information, contact Derek at ddenlinger@paulo.com