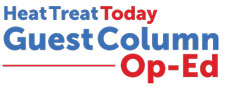
You can take the aircraft apart, but can you put it back together? Reverse engineering, as anyone who has ever taken apart the TV remote will tell you, is more complicated than it first appears. It is, however, far from impossible. Learn the essential steps to reverse engineering, the role of heat treating, and the challenges the thought process presents.
For this Technical Tuesday piece, take a few minutes to read Jonathan McKay's, heat treat manager at Thomas Instrument, article drawn from Heat Treat Today's March Aerospace Heat Treating print edition. Heat Treat Today is always pleased to share pieces from one of our 40 Under 40 alumnus like Jonathan!
If you want to share ideas about the aerospace industry, our editors would be interested in featuring it online at www.heattreattoday.com. Email Bethany Leone at bethany@heattreattoday.com with your own contributions!

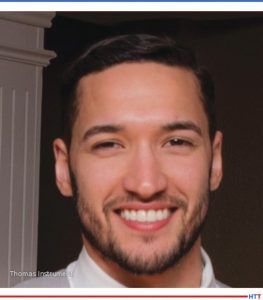
Heat Treat Manager at Thomas Instrument
Source: Thomas Instrument
Reverse engineering (RE) is the process of taking a component or design and dissecting it all the way down to the raw material. Reverse engineering can range from a singular component such as a piston or gear, to multiple components that make up an overall assembly such as an engine or mechanical actuator. This process allows engineers to analyze and gain an understanding of a component’s overall function and design through deductive reasoning. RE can range in the type of analysis, from geometric measurements and material analysis to electrical or mechanical testing. Each analysis reveals clues of how something can be reproduced. The idea of reverse engineering is to look beyond what’s in front of you and find the unexposed clues that can show why something was designed or possibly the thought process of the original designer.
Reverse engineering typically happens through a third-party manufacturer usually not affiliated with the original equipment manufacturer (OEM). Often this is done because the original manufacturer no longer supports the product, or the original design is outdated and needs to be modernized to improve efficiency, functionality, or life expectancy. To put this in perspective, the U.S. Airforce received its first B-1 Bomber in 1984. Since then, over 100 aircrafts have been delivered. After nearly 50 years the aircraft is still flying, but many OEM manufacturers have moved on to newer programs, thus allocating their capabilities and capacity towards the present and future market demands. This creates a market for fabrication of replacement components and assemblies to support aging platforms. In most cases, the OEM’s retain proprietary data thus creating a need for RE processing.
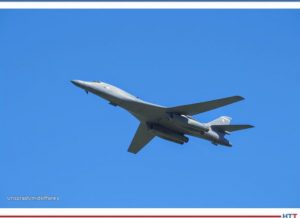
Source: Unsplash.com/midkiffaries
With aerospace products in particular and specifically aging aircrafts, one will encounter obsolescence issues. The goal is to maintain the aircraft with replacement parts that conform to all form, fit, and function requirements while also assuring they have proper life expectancy with respect to maintenance cycles. With this in mind, you typically work with low volume production and invest more time into the design and planning phase of the process. When engaged in this process, it is critical that one understands and implements a fabrication plan that will yield a product that is equivalent or better than that of the OEM. Some engineers would say “Well, let’s make it bigger and better,” but with aerospace components this is not always the case. Typically, the main focus is to replicate the original design intent to the best of your ability because you have a specific footprint and weight to maintain as well as functionality. The exchangeability of the original design and RE design is key. The reverse engineered product needs to possess the same functional and physical characteristics and be equivalent in the performance, reliability, and maintainability. This allows both items to be exchanged without concern for fi t, performance, or alterations to its adjoining component(s).
Another key point in RE processing could be to limit long lead phases by minimizing the need for additional qualification testing where possible. As plating, heat treat, or materials begin to deviate from the initial design, you must consider requalification testing to prove those changes are not detrimental to the application and do not cause more harm than good. Sometimes engineers create features within a design that are meant to be a weak point; this prevents a more critical component from breaking or being destroyed. When you begin to make deviations, it may push the weak point closer to the critical component.
While there are certainly many steps to RE, the essential steps include:
- Collect as much data as possible from an external standpoint without destroying or disassembling; i.e., note the overall measurements, orientation, special features, electrical or mechanical properties, etc. It is also a good idea to analyze mating components and/or the system in which the component is utilized. Mating parts are a big part of the discovery; the mating parts can help determine what alternate materials, plating, heat treat, or finishes can be used.
- Start creating preliminary drawings with detailed dimensions, notes, and features that were inspected from Step 1.
- Slowly disassemble the part (if an assembly) and inspect key features and create preliminary drawings for sub-assembly components. In some cases, it helps to reassemble the product to ensure an understanding of how it goes back together in order to optimize the assembly process once new components are manufactured.
- Evaluate the product(s). Conduct material analysis to acquire chemical and mechanical property data. This will aid in defining the appropriate layout for machining, material conditioning (i.e., heat treatment), external finishes/coatings, etc.
While the design and planning phase may pose some challenges, the more critical challenges that occur during reverse engineering are in the execution of the manufacturing, assembly, and qualification testing. To elaborate, once you begin machining and processing components, there may be special methods of manufacturing that require discovery because standard methods may not have worked when the OEM produced it. When this happens, you go back and forth on updating and fine-tuning the process plans, fixturing, programs, etc. Sometimes this means scrapping parts and starting over or validating if parts are still usable for prototyping. Along the same lines, when the process progresses into the assembly and testing phase, engineers typically discover variability, errors, or weak points that require adjustments. In those cases, the engineer’s drawings must be revised. A large percentage of these issues can be limited through experience with similar components or assemblies, but in most cases, there is a lot of analysis and some trial-and error involved in the manufacturing, assembly, and testing phase that is not apparent upon initial RE processing.
References:
- Boeing. “The Bone.” https://www. boeing.com/defense/b-1b-bomber/
- DLA. “Master List of Technical and Quality Requirements Version 14.”
- MIL-STD-280A. “Handbook for definitions of item levels, item exchangeability, models, and related terms.”
- DOD Washington, D.C. 20301.
Special thanks to David V. Jones and Thomas R. Blackburn IV at Thomas Instrument for their input on this topic.
About the Author:
Jonathan McKay is a mechanical engineer at Thomas Instrument, a company specializing in reverse engineering critical aerospace components. At the company, he is manning the establishment of heat treat operations, has created procedures and process plans for Thomas Instrument to be an approved heat treater for an aerospace prime, and has attained Nadcap accreditation for heat treat.
Contact him at Jonathan.mckay@thomasinstrument.com