The Cost of Furnace Insulation Failure
You see a little orange light coming from your furnace while it’s operating. What if that was a clue that you were losing over $7,000 annually on one furnace? In today’s Combustion Corner installment Jim Roberts, president of US Ignition, shares more details about the long term costs of furnace insulation failure.
This informative piece was first released in Heat Treat Today’s May 2025 Sustainable Heat Treat Technologies print edition.
A furnace guy walks into a bar and smells burning hair! A sure indication of wasted resources…
Normally, I would not concern myself, as a burner guy, with heat loss issues. But as a furnace guy, this is one of the biggest culprits when it comes to running an energy-efficient operation. Burner guys take it as an affront when the burners get blamed for being inefficient or hard to keep balanced. It’s the ultimate slap in the face when the burners (and sometimes the whole furnace) get labeled as a “gas hog.” The seasoned furnace guys who just read that are shrinking back in horror at the mention of a gas hog because they know there are many ways to waste fuel, and some of them are hard to rectify if equipment is not up to snuff.
This installment will provide an example of what can be done to avoid wasting fuel and why you should prioritize this problem.
Insulation and Energy Loss
The aforementioned smell of burning hair, of course, was rather dramatic and hopefully unlikely, but we have all walked into a heat treat facility and been hit in the face with some sort of otherworldly blast of heat. I know, you’re thinking, “Well, duh, Captain Obvious, we are in the business of making things really hot in here.” I get it. However, we all know that if the furnace insulation has broken down, or worse yet, failed completely in spots, energy loss is imminent and will affect the bottom line. And it never seems to be one big issue, but it’s a compounded effect that will add up to serious energy dollar loss.
A Tale of Two Furnaces
Our example today is the retelling of my own experience. I got called to a shop in the Northwest geo-zone a while ago (okay, a long while ago). There were two furnaces sitting side by side with matching load profiles. The manager of the operation walked me out into the work area, and staring at a pair of furnaces said, “One is using almost twice as much fuel. Same everything from an equipment standpoint but almost double the fuel usage.” I looked and observed that the furnace in question had visible orange around the door seams, around the burner flanges, and around the flue. The other furnace had a completely dark exterior. The work associates in this plant were all suffering from radiation blindness — they could not see this very visible damage because the insulation on this furnace had deteriorated slowly enough they were accepting it as normal. Only, it’s not.
Let’s Run the Numbers
If you can see any type of color around doors, the energy loss is massive. At 2000°F Flue gas temperatures, the heat loss from radiation alone is already around 40,000 BTU/hr per square foot of visible radiation.
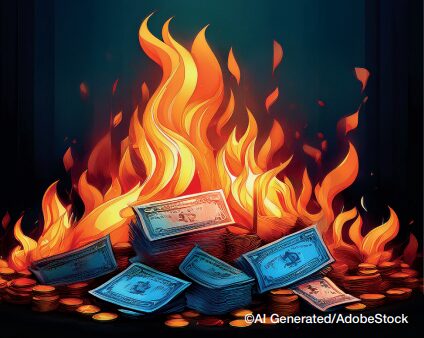
If you consider that there are probably outside air ingresses through these gaps as well, you can estimate that will result in 10,000 BTU/hr per square foot of additional loss. Those numbers combine for a 50,000 BTU/hr per square foot of loss from the big orange leaks. That’s 50 cubic feet of natural gas every hour for every square foot. You might say, “Well, nobody would have a square foot of glowing furnace shell.” However, if you take it a 10-foot door opening, and the gap is 1 inch all the way around, the square foot of exposed area is leaking heat off at 4 times that square footage because it’s really just a ribbon of heat pouring out.
So now, I was witnessing 200 cubic feet of fuel leaking out every hour that this furnace was heating all day, every day. That is 200 cubic feet × 24 hours/day × 6 days/week × 50 weeks/year = 1,440,000 cubic feet of gas wasted on a single door.
If we estimate that gas is averaging around $5.25/1,000 cubic feet of industrial grid price, that leaky door costs $7,560.00 per year in fuel. If we consider that the gas that was being blown into the room was really intended to heat the load, we can argue there are production losses as well.
Become an Energy Hero
In the case of the client I was helping, I recommended refractory repairs to ensure there was no orange showing outside the furnace. The manager thought I had invented heat — I was his energy hero — and all of a sudden, the burners weren’t gas hogs, and the furnace was up to speed with its twin.
You, too, can be a burner/furnace/energy hero for your facility by not allowing yourself to become radiation blind. Look around, feel the heat that is there, and don’t accept it as the norm. When you see it, fix it. The money you save will almost always pay for the repairs many times over.
Be safe always, and we’ll chat more next month.
About The Author:
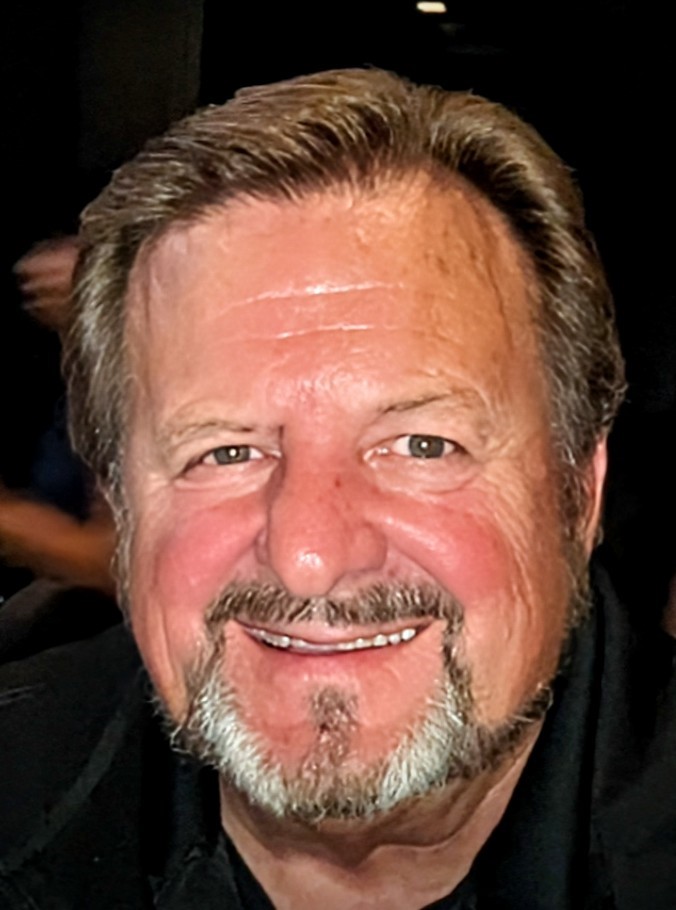
President
US Ignition
For More Information: Contact Jim Roberts at jim@usignition.com.
Find heat treating products and services when you search on Heat Treat Buyers Guide.Com
The Cost of Furnace Insulation Failure Read More »