Aluminum Rolling Company Expands Operations with Heat Treat Software
The aluminum rolling division of ElvalHalcor S.A., Elval, has placed an order for a sustainability suite with a heat treat supplier with North American locations. This technology will be used for Elval’s flat-rolled aluminum manufacturing plant based in Oinofyta, Greece.
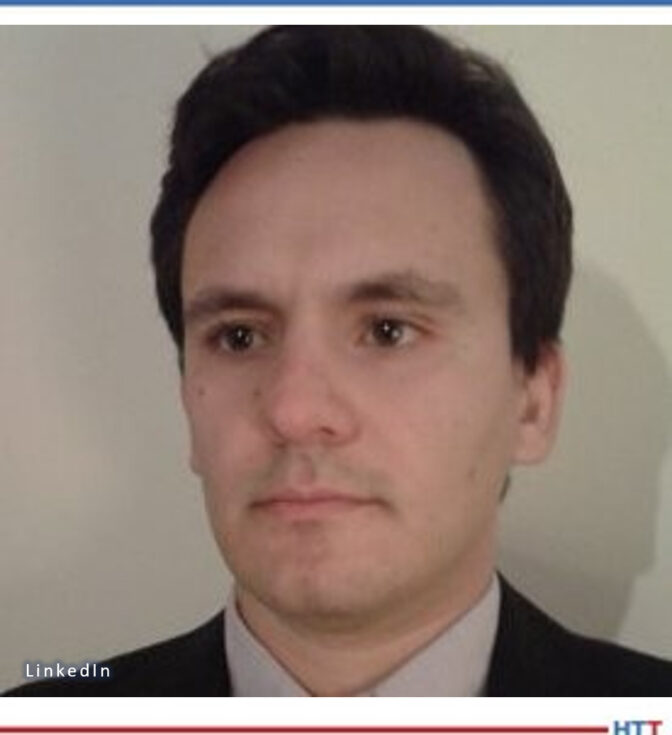
Electrical & Electronic Maintenance Deputy Director
Elval
Source: LinkedIn
The Viridis Energy & Sustainability Suite from SMS group will contribute to Elval’s goal to reduce carbon emissions and optimize overall production processes. With the installation of two modules of the Suite, Viridis Performance and Viridis Grids, Elval will be equipped to meet the ever-increasing demands for responsible and energy-efficient management in the aluminum industry.
The automated machine learning (Auto ML) resources of Viridis Performance calculate targets automatically, maintaining relevance in changing production conditions. It will comprise over 70 equipment assets, such as melting furnaces, preheating furnaces, hot and cold rolling mills, among others. Viridis Grids will support Elval to precisely and autonomously calculate energy consumption forecast based on the production plan via automated machine learning resources.
Stated Drakotos Athanasios, the electrical & electronic maintenance deputy director at Elval, “Our partnership with SMS group represents a significant step in our sustainability journey. The Viridis Energy & Sustainability Suite aligns perfectly with our commitment to sustainable aluminum production and reducing our energy and environmental footprint. We are confident that this investment will have a positive impact on our operations and support our carbon footprint reduction pathway”.
Aluminum Rolling Company Expands Operations with Heat Treat Software Read More »