thyssenkrupp Bolsters Electric Mobility Production with Annealing, Isolating Line
A new annealing and isolating line has been supplied to thyssenkrupp Steel for the production of high-grade NGO (non-grain-oriented electrical steel strip). This strip processing line comprises a precise heat treatment in which the structure of the cold-rolled strip is recrystallized during the annealing process, followed by the application of an insulating layer to ensure optimal electrical properties. This is particularly important for the materials used in motors and generators installed in electric vehicles.
The new processing line, supplied by the project partner, SMS Group, has an annual capacity of 200,000 tons and is designed to process electrical steel strip in widths of up is now in operation. SMS technology enables the production of electrical sheet for energy-efficient applications, for example electromobility. The technological core of the line is the combined heat treatment and coating process.
With this line, the modernization of thyssenkrupp‘s Bochum location is nearly complete, allowing the steel producer to better serve its clients in the automotive, energy, and other manufacturing sectors. The new plant will allow the manufacture of up to 0.2 mm thin electrical sheet with particularly homogeneous mechanical and magnetic properties, specially designed to meet the requirements of highly efficient motors used primarily in electric vehicles. The finishing line is scheduled to go on stream in 2026.
“This facility not only represents a huge step forward in our production capacities,” said Dr. Harald Espenhahn from thyssenkrupp Steel Europe, “it enables us to manufacture high-quality NGO steels that allow our customers to meet the changing demands of the market and to develop products with increased energy efficiency.”
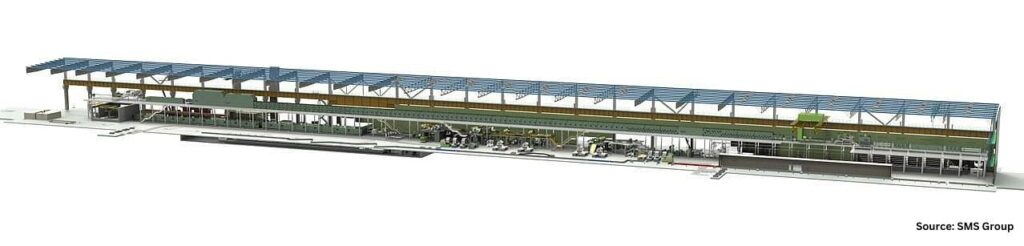
Main image: The team from thyssenkrupp Steel Europe and SMS Group preparing to start up the pioneering plant technology for the manufacture of high-grade electrical sheet / L to R: Engin Karakurt, Chairman of the Works Council of thyssenkrupp Steel in Bochum; Dr. Harald Espenhahn, Head of Technology and Environmental Management, thyssenkrupp Steel; Andy Rohe, Head of Downstream Operations, thyssenkrupp Steel; Thomas Eiskirch, Mayor of Bochum; Dr. Marie Jaroni, Chief Transformation Officer at thyssenkrupp Steel; Markus Kovac, Head of the Bochum Plant Area, thyssenkrupp Steel
Press releases are available in their original form here and here.
Find heat treating products and services when you search on Heat Treat Buyers Guide.Com
thyssenkrupp Bolsters Electric Mobility Production with Annealing, Isolating Line Read More »