The rise of electric vehicles (EVs) is changing the automotive manufacturing game, and laser heat treating could be the new MVP. Learn how laser heat treating is reducing cost, improving time to market, and limiting distortion.
This Technical Tuesday article was composed by Aravind Jonnalagadda (AJ), CTO and co-founder, Synergy Additive Manufacturing LLC. It appears in Heat Treat Today’s August 2023 Automotive Heat Treating print edition.
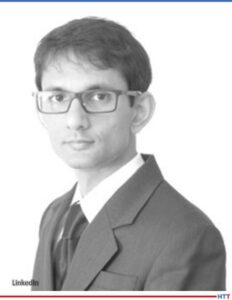
Aravind Jonnalagadda
CTO and Co-Founder
Synergy Additive Manufacturing LLC
Source: LinkedIn
The electric vehicle initiative and the efforts of automakers to overhaul their current vehicle lineups with electric offerings has many automakers and technology corporations rethinking automotive engineering to the most minute detail of manufacturing. The modern automotive industry not only affects automakers, but consumers, who will also transition into a diverse new market of emerging technologies. Deloitte Insight estimates that by 2030, EVs will account for 31% of total market share for new car sales. Per the report, the worldwide market for new EVs is expected to swell from 2.5 million in 2020 to 11.2 million in 2025 to 31.1 million by 2030 (Woodward, et al., “Electric vehicles”).
Contact us with your Reader Feedback!
With a surge in demand for new EVs, OEMs are racing to bring new models to the market. This demand has prompted automakers to push towards shorter product life cycles for EVs compared to their internal combustion engine (ICE) counterparts. Along with this, the recent supply chain disruptions fueled a renewed push towards new technologies and reliable partners who can accelerate the product life cycles while reducing the overall manufacturing costs. One such technology that gained a stronghold in the tool and die industry over the last few years is laser heat treating on automotive dies.
Laser Heat Treat Accelerates EV Dies to Market
Automotive dies often require all the male radii to be heat treated to reduce the wear and improve die life. Conventional heat treating processes such as induction and flame have high heat input, which distorts the die. To account for this, the die makers leave extra stock material to later come back and hard mill the die to finish dimensions.
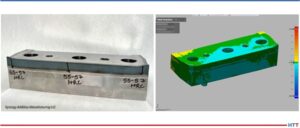
Laser heat treated trim inserts (approximate dimensions of 7” x 4” x 3”, base material 4140)
demonstrate distortion of less than 10 microns and hardness of 55–57 HRC
Source: Synergy Additive Manufacturing LLC
This additional hard milling step adds substantial cost to the die manufacturing process. Conventional processes are often performed by hand and lack feedback control. This results in poor quality and inconsistencies in the heat treated surfaces. Laser heat treating, on the other hand, results in minimal distortion. The dies are machined to their final form and laser heat treated as a final step, thereby reducing the process steps such as hard milling, 2D based machining, etc. This saves substantial time and costs for the die makers, not to mention improved and repeatable quality.
The laser heat treating process involves a laser beam (with a typical laser spot size from 0.5” x 0.5” to 2” x 2”) focusing on the metal surface. With proper control, the incident laser energy raises the surface temperature of the metal above its martensitic transformation temperature. The metal’s thermal mass aids in rapid “self quenching” (by removing the heat via conduction), resulting in the formation of the desired martensite microstructure. This gives the material its required hardness and wear properties. To watch a video, go to: https://www.youtube.com/watch?v=8cUxEexAI9E.
By utilizing a laser beam, unrivaled precision is achieved by delivering the smallest possible energy to the metal part, resulting in minimal to virtually no distortion in large automotive dies. The unique characteristics of laser technology offer the following benefits:
- Minimal to virtually no distortion
- No hard milling required on large automotive dies
- Consistent hardness depth (via. feedback control)
Heat Treatable Materials
Any metal with 0.2% or higher carbon content is laser heat treatable. Common materials used in automotive industry include: D6510, 0050A, A2, D2, S7, G3500, GM338, GM190, H13, 4140, 4130, 410 SS,431 SS, P20, 8620, and others.
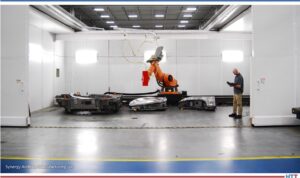
Source: Synergy Additive Manufacturing LLC
When analyzing over 100 applicable die castings (post, cavity, and binders), Autodie LLC concluded that an average of 7-day reduction in time to market (TTM) was achieved by switching over to laser heat treating process. By avoiding hard milling operation, laser heat treating resulted in 37% reduction in machining time. Substantial savings in cutter cost were observed as the castings are now finished by 3D machining while in soft condition. Over an 11-month period, Kaizen savings had a benefit to cost average of 28.6 (Jonnalagadda and Timmer, “Laser Heat Treating”).
Conclusion
Laser heat treatment offers substantial cost savings as well as reduction in TTM. This process is likely to expand into the automotive and metal part manufacturing sectors. For example, Synergy Additive Manufacturing’s laser heat treating process is already being used in a variety of automotive applications such as trim dies, hot stamping dies, hem dies, restrike bars, flange dies, and molds. A variety of non-automotive parts such as large gears and bearings are also already being laser heat treated. Laser heat treatment faces no significant barriers to adoption, aside from the ones that are common to any emerging technology. These include lack of familiarity and a shortage of existing suppliers. The savings, measured by cost, schedule, quality, and energy reduction, are significant and well supported.
About the author:
Aravind Jonnalagadda (AJ) is the CTO and co-founder of Synergy Additive Manufacturing LLC. With over 15 years of experience, AJ and Synergy Additive Manufacturing LLC provide high-level laser systems and laser heat treating, specializing in high power laser-based solutions for complex manufacturing challenges related to wear, corrosion, and tool life. Synergy provides laser systems and job shop services for laser heat treating, metal based additive manufacturing, and laser welding.
For more information:
Contact Aravind Jonnalagadda at aravind@synergyadditive.com.
References:
Aravind Jonnalagadda and Brian Timmer, “Laser Heat Treating of Automotive Dies for Improved Quality and Productivity” (Great Designs in Steel Conference, 2021), https://www.steel.org/steel-markets/ automotive/gdis/2021-gdis-presentations/.
Michael Woodward et al., “Electric vehicles: Setting a course for 2030,” Deloitte Insights, July 28, 2020, https://www2.deloitte.com/us/en/insights/focus/future-of-mobility/electric-vehicle-trends-2030.html.
Find heat treating products and services when you search on Heat Treat Buyers Guide.com