Stainless Corrosion
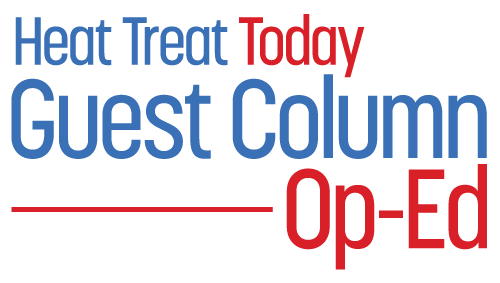
Stainless steel has crept into our kitchens and now also our garages, the Tesla Cybertruck being the latest product to sport a stainless steel layer. What most people don’t realize is that while stainless steel is corrosion resistant, it will rust in a lot of circumstances. In this Technical Tuesday article, Sarah Jordan explores how stainless steel can be compromised by improper heat treatment and the steps heat treaters can take to prevent corrosion.
This column was adapted from a #MetallurgyMonday post written by Sarah Jordan in June 2024 and shared at her LinkedIn account. It appeared as an article in Heat Treat Today’s August 2024 Automotive print edition.
I’m starting to see Cybertrucks out in the wild more, so I decided to talk about stainless corrosion for #MetallurgyMonday. (If you don’t know what #MetallurgyMonday is, it is a weekly educational post on metallurgy topics that I’ve been writing on LinkedIn for the past two years.)
First a little up front. I’m not a fan of the aesthetics of the Tesla Cybertruck. Plus, we need about twice the load capacity for our work purposes since Skuld actually uses our truck as a truck.
More to the point, stainless steel is not rust proof. It is corrosion resistant and will rust in a lot of circumstances.
To understand why, we need to understand what prevents corrosion in the first place. The key elements are chromium and nickel. Chromium reacts with oxygen to create a thin layer of chromium oxide. This is on the surface and blocks further oxidizing of the underlying layers. Meanwhile, the nickel enhances the corrosion resistance. It also makes the material more formable and weldable.
The short story is that if the chromium oxide layer gets compromised, stainless steel will corrode.
Improper heat treating can also contribute to stress corrosion cracking.
Sarah Jordan
- Pitting corrosion: If you have a scratch or a pit, this can damage the protective film, and then corrosion begins. It’s worse in environments with chloride ions, such as seawater or pool water. Chlorides break down the passive layer, leading to rapid and severe corrosion in small areas.
- Crevice corrosion: This occurs when two objects come together, especially things like fasteners or where there is a gasket. Inside the crevice you will have a lack of oxygen. The lack of oxygen prevents the reformation of the protective chromium oxide layer. Once corrosion gets started, it can get very severe by propagating in the crevice.
- Stress corrosion cracking (SCC): Corrosion is made worse where there is a combined effect of tensile stress and a corrosive environment. It typically affects stainless steel used in structural applications that are exposed to chloride or sulfides. SCC can cause sudden and catastrophic failure of the metal structure.
- Galvanic corrosion: Galvanic corrosion happens when two metals are put together. One of them almost always wants to preferentially corrode. The one that corrodes is the one that is higher on the galvanic series.
- Intergranular corrosion (IGC): Sometimes this is called intergranular attack (IGA). In this case, corrosion occurs preferentially at grain boundaries. This can occur in stainless if the grain boundaries get depleted of chromium because a minimum amount is needed to ensure the passive film can form to protect the metal. When this occurs, there can also be localized galvanic corrosion.
- Composition variation: If the composition has segregation, then there are some areas that have less of the corrosion-helping elements. And on top of that, galvanic corrosion can start happening within the material.
What does all of this have to do with heat treating? Improper heat treating can contribute to corrosion.
For instance, intergranular corrosion can be caused if the material is exposed to 842–1562°F (450–850°C) for too long as this will cause chromium carbide to form at the grain boundaries and deplete the chromium. This process is called “sensitization.” It is avoided by making sure quench rates are fast enough through the risky temperature range.
A somewhat similar situation can occur during heat treating if sigma phase forms in super duplex stainless steel. Sigma phase is an iron chromium phase which can also deplete the chromium.
Improper heat treating can also contribute to stress corrosion cracking. When material is quenched, it can cause residual stresses that, if not relieved, can become an issue.
Corrosion in stainless steel can often be traced to improper heat treatment. When stainless steel is heated between 842–1562°F (450–850°C), chromium carbides can form at the grain boundaries, depleting the surrounding areas of chromium and making them susceptible to corrosion.
All of this to say, things like the Cybertruck (or for that matter stainless fridges and appliances) can be prone to corrosion since they are exposed to a lot of abuse and aggressive environments. It is critical to ensure they are properly manufactured, including good heat treating practices. It is also critical to provide them with proper maintenance to keep the corrosion resistance and appearance lasting as long as possible.
About the Author:

Founder & CEO
Skuld, LLC
Source: Author
Sarah Jordan is an accomplished metallurgical engineer and entrepreneur. She received a bachelor’s of science and master’s of science in this discipline from The Ohio State University and has been pursuing a PhD in Metallurgical Engineering from WPI. Skuld is a certified WOSB and EDWOSB startup focused on 3D printing, advanced manufacturing, and advanced materials.
For more information, contact Sarah at her LinkedIn profile: Sarah Jordan | LinkedIn.
Find Heat Treating Products And Services When You Search On Heat Treat Buyers Guide.Com
Stainless Corrosion Read More »