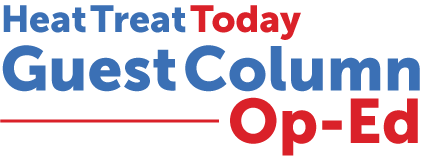
Metal 3D additive manufacturing has grown dramatically in the last five years. Nearly every metal printed part needs to be heat treated, but this presents some challenges. This article will address some of the challenges that a heat treater faces when working with these parts.
This Technical Tuesday article, written by Mark DeBruin, metallurgical engineer and CTO of Skuld LLC, was originally published in December 2023’s Medical and Energy magazine.
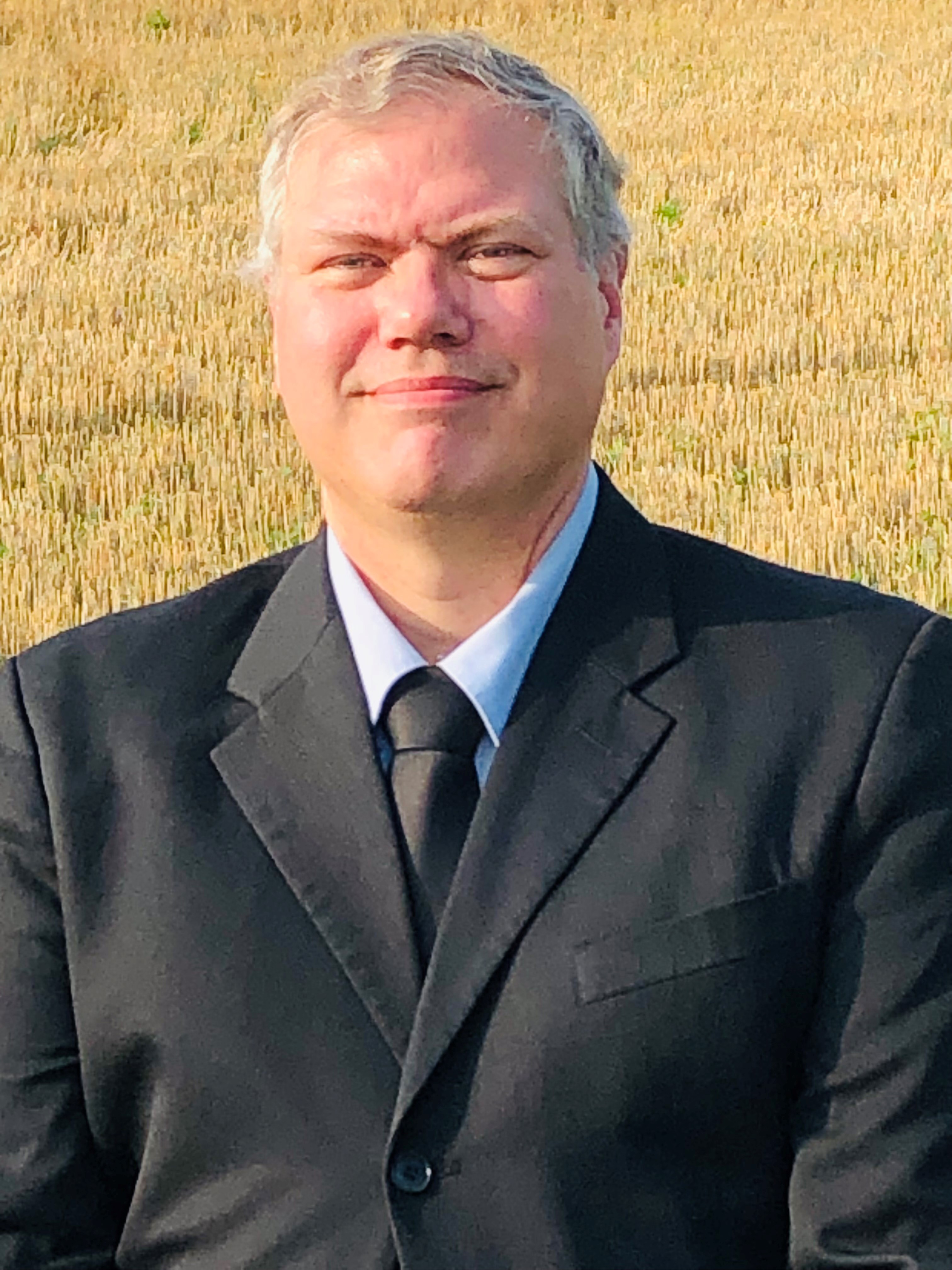
In my experience, on average, about 10% of all 3D metal printed parts break during heat treatment; this number varies depending on the printer and the unique facility. While materials can be printed with wire or even metal foils, I’m going to mainly focus on the approximately 85% of all metal 3D printed parts that are made from metal powder and either welded or sintered together.
Most metal printed parts normally have heat added to them after printing. In addition to the heat of the printing process and wire electrical discharge machining (EDM) process to separate the part from the build plate, heat may be added up to five times. These steps are:
- Burnout and sintering (for some processes such as binder jet and bound powder extrusion)
- Stress relieving
- Hot isostatic pressing (HIP)
- Austenitizing (and quenching)
- Tempering
3D printing can create a non-uniform microstructure, but it will also give properties the client does not normally desire.
Heat treating makes the microstructure more uniform and can improve the properties. Please note that heat treating 3D printed parts will never cause the microstructure to match a heat treated wrought or cast microstructure. The microstructure after heat treating depends on the starting point, which is fundamentally different.
If the part is not properly sintered, there is a high chance it will break during heat treatment. It may also exhaust gases, which can damage the heat treat furnace. The off gases will recondense on the furnace walls causing the furnace to malfunction and to need repair. This can potentially cost hundreds of thousands of dollars.
During powder 3D printing, there is a wide variety of defects that can occur. These include oxide inclusions, voids, unbonded powder, or even cracks that occur due to the high stresses during printing. Even if there are not actual defects, the printing process tends to leave a highly stressed structure. All of these factors contribute to causing a print to break as the inconsistent material may have erratic properties.
In a vacuum furnace, voids can be internal and have entrapped gas. Under a vacuum, these can break. Even if something was HIP processed, the pores can open up and break. Even if they do not break and heat is applied, the metal will heat at different rates due to the entrapped gas.
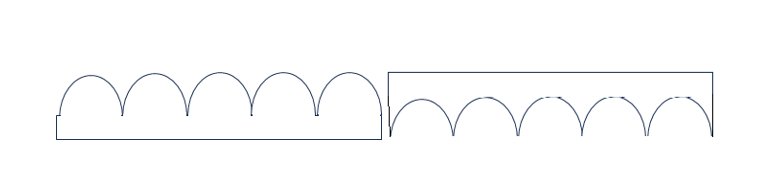
There are also issues during quenching due to the differences in the surface finish. In machining, the surface is removed so there are not stress concentrators. In 3D printing, there are sharp, internal crevices that can be inherent to the process that act as natural stress risers (see Figure 1). These can also cause cracking.
When 3D printed parts break, they may just crack. This can result in oil leaking into the parts, leading to problems in subsequent steps.
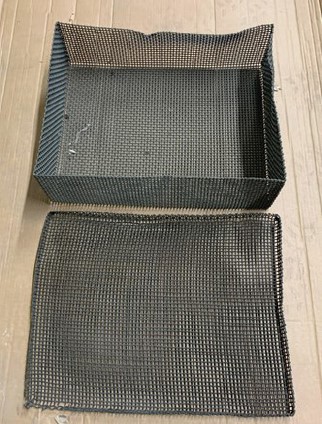
However, some parts will violently shatter. This can happen when pulling a vacuum, during ramping, or during quenching. This can also cause massive damage to the furnace or heating elements. It can potentially also injure heat treat operators.
A lot of heat treaters protect their equipment by putting the parts into a wire mesh backet (Figure 2). This protects the equipment if a piece breaks apart in the furnace, and if a piece breaks in the oil, it can be found.
Print defects in metal 3D printed parts can be a challenge to a heat treater. Clients often place blame on the heat treater when parts are damaged, even though cracking or shattering is due to problems already present in the materials as they had arrived at the heat treater. As a final piece of advice, heat treaters should use contract terms that limit their risks in these situations as well as to proactively protect their equipment and personnel.
About The Author
Mark DeBruin is a metallurgical engineer currently working as the chief technical officer at Skuld LLC. Mark has started five foundries and has worked at numerous heat treat locations in multiple countries, including being the prior CTO of Thermal Process Holdings, plant manager at Delta H
Technologies, and general manager at SST Foundry Vietnam.
For more information:
Contact Mark at mdebruin@skuldllc.com