Inside GKN Powder Metallurgy’s Acquisition of Forecast 3D
Picture two men sitting at a bar table watching a video on a smartphone. As they enthuse about how much they love it, a bystander might be tempted to think they’re just killing time goofing off. “It’s fantastic technology,” the man with the phone, Forecast 3D founder and CEO Corey Weber, says of the Multi Jet Fusion (MJF) process featured in the time-lapse video that shows a Californian facility in the dead of night illuminated only by the passing of a dozen lights flashing over a dozen powder beds through until the morning. As he pulls back his smartphone, he and Guido Degen, GKN Powder Metallurgy’s President of Additive Manufacturing, look pleased with both the technology and themselves.
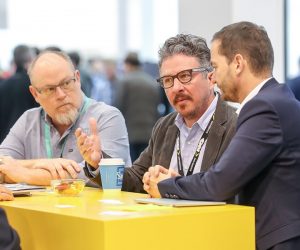
GKN Powder Metallurgy’s acquisition of Forecast 3D appears to be natural synergy. Much of Forecast 3D’s expertise exists in polymer 3D printing, serving the aerospace and medical markets on the West Coast. GKN’s focus is metal parts, the bulk of which is for the automotive market in Central Europe and the Midwest of the United States. When GKN highlighted the contrasting technological expertise that exists in both companies, the figureheads at Forecast were on the same wavelength.
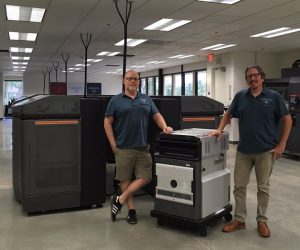
“We knew that the opportunity is much bigger than the size of our pockets,” Weber acknowledges. “We needed resources and our goal was to get someone that shared our vision. We found those with GKN. . . . And, honestly, it’s kind of a relief because now we can really focus on polymers and let them handle metals.”
To read more from the original article, click here: https://www.tctmagazine.com/3d-printing-news/gkn-powder-metallurgy-forecast-acquisition-deal/
Inside GKN Powder Metallurgy’s Acquisition of Forecast 3D Read More »