A 3D equipment and materials supplier recently announced a collaboration agreement to develop advanced tungsten-based metal 3D printing using binder jetting that focuses on two metal matrix composites.
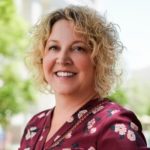
Global Tungsten & Powders Corp, a global manufacturer of tungsten and metal powders, and The ExOne Company, which manufactures industrial sand and metal 3D printers using binder jetting technology, have entered into this collaborative partnership to focus on tungsten-copper (W-Cu), used in high-voltage electrical applications, and cemented carbide (WC-Co), used in cutting tools and wear-resistant parts.
GTP uses the ExOne® Innovent®, an advanced and compact binder jet 3D printer, to manufacture parts in tungsten carbide and other tungsten composites. Binder jetting is a 3D printing process that uses a digital file to inkjet a bonding agent into a bed of powder particles, creating a solid part one layer at a time. Compared to other 3D printing processes, binder jetting delivers precision parts at a high rate of speed, making it an ideal approach for serial production.
The new ExOne-GTP collaboration focuses on the development of two metal matrix composites:
- cemented carbide (WC-Co), a material with very high hardness and toughness that is widely used for the production of cutting tools and wear-resistant parts
Tim Pierce, ExOne Vice President of Metal Commercial Products - copper-tungsten (CuW), which is used in applications where high heat resistance, high electrical and thermal conductivity, and low thermal expansion are needed
“Binder jetting is the 3D printing method of choice for serial production of hard metal parts,” said Deborah West, vice-president of Business Unit Refractory & Specialty Powders, GTP. “Traditionally, tungsten carbide powder is pressed into the desired shape and then sintered to give it strength and density. Instead of costly and timely mold construction, the parts now can be printed directly in the desired shape, still using sintering technology to achieve the final strength. As a market leader in the development and production of high-quality tungsten powders, GTP always stays on top of the latest technology. We are excited to work with ExOne in the development of cutting-edge technology for the additive manufacturing industry.”
“Metal 3D printing using our exclusive approach to binder jetting has exciting and significant consequences for a variety of manufacturers, including those who make parts with cemented carbide and other tungsten composites,” said Tim Pierce, ExOne Vice President of Metal Commercial Products. “Our latest development collaboration with GTP will help advance the materials necessary to deliver on the vision of producing these parts faster, with less waste and more geometric design freedom.”