Railway Supplier voestalpine To Expand with Hardening Line
voestalpine Fastening Systems, a supplier to the railway industry, is bolstering its hardening processes of steel parts with a technological line consisting of multiple furnaces and washers. The process will be carried out in a protected nitrogen atmosphere with temperatures up to 1742°F (950°C) on parts to be used in railway rolling stock.

Deputy Director of Aluminum Process and CAB Furnaces
SECO/WARWICK
The technological line on order from SECO/WARWICK consists of two CaseMaster furnaces, three tempering furnaces, and two washers. In addition, the railway supplier will have an electric chamber, a cooling station, and an endothermic atmosphere generator delivered.
“[T]he result of technological tests carried out in a service hardening plant that the customer was acquainted with … convinced voestalpine Fastening Systems that we would meet the high requirements of the contract. The line is configured in such a way that if the volume of the company products decreases, the customer can also offer commercial processing due to the wide technological spectrum of this main furnace unit,” said Mariusz Raszewski, deputy director of the Aluminum Process and CAB Furnaces Team at SECO/WARWICK.
The technological line will include a loader operating in automatic mode, a set of roller tables, and a closed-loop water system. The number of the supplied technological line units is selected to ensure the quality of manufactured components. The whole process will be supervised by a master system, which is used to continuously monitor the heat treatment equipment operation and provides advanced data analysis for the production processes.
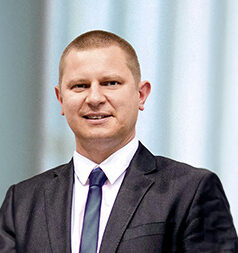
Chief Operating Officer
voestalpine Fastening Systems
“The universal furnace solution will allow [the client] to process various parts in various configurations. Apart from technological parameters, it is important for us to limit processed part deformations, which is possible with the solution on order,” said Mariusz Fogtman, chief operating officer, voestalpine Fastening Systems Sp. z o. o.
This is the first cooperation between both partners in this product area. SECO/WARWICK has previously delivered vacuum furnaces to the voestalpine Group.
Press release is available in its original from here.
Find heat treating products and services when you search on Heat Treat Buyers Guide.Com
Railway Supplier voestalpine To Expand with Hardening Line Read More »