Heat Treat Radio #11: Laser Heat Treating with Laser Hard
Welcome to another episode of Heat Treat Radio, a periodic podcast where Heat Treat Radio host, Doug Glenn, discusses cutting-edge topics with industry-leading personalities. Below, you can either listen to the podcast by clicking on the audio play button, or you can read an edited version of the transcript. To see a complete list of other Heat Treat Radio episodes, click here.
Audio: Heat Treat Radio: Laser Heat Treating with Laser Hard
In this conversation, Heat Treat Radio host, Doug Glenn, interviews two families who have been at their manufacturing game for multiple generations. Not long ago they joined forces to establish a new company — Laser Hard, Inc. — and to introduce one of the most cutting edge-heat treat technologies around today: laser heat treating. For many of you who have difficult-to-heat treat parts, whether it’s because of blind holes, or the fact that the part is too big to move, or perhaps you’d like to significantly reduce, if not eliminate, post-heat treat hard machining, you’re going to find today’s Heat Treat Radio episode on laser heat treating especially interesting.
Click the play button below to listen.
Transcript: Heat Treat Radio: Laser Heat Treating with Laser Hard
The following transcript has been edited for your reading enjoyment.
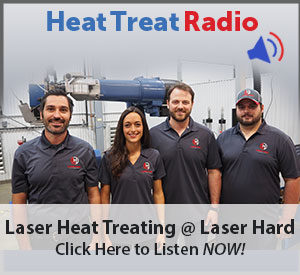
In this episode of Heat Treat Radio, let’s talk about one of the most cutting-edge heat treat technologies around today — laser heat treating.
Thanks for joining us. My name is Doug Glenn and I’m your Heat Treat Radio host and publisher of Heat Treat Today. You can find us on the web at www.heattreattoday.com or simply by Googling Heat Treat Radio. And here’s something new, Heat Treat Radio is now on iTunes! On the website, we update our heat treat content daily, and if you’re a manufacturer with an in-house heat treat department, you’re going to love our site.
Although it sounds Star Treky, laser heat treating is a pretty well-established technology, especially in Europe, but not so much in the United States. The applications are intriguing to say the least – as is the way it is being introduced into the United States – and as are the two families introducing it. One family – long time heat treaters. The other family – long time laser welders and laser cladders. Both minding their own businesses – literally – both thinking about ways to better serve their customers. These two businessmen were from the same small town in Pennsylvania, and they paired up to create a new company called Laser Hard.
And that’s where our story begins.
Introducing Doug Peters of Peters’ Heat Treating and Blair Learn of Phoenix Laser Solutions
Doug Glenn (DG): First, let me introduce you to the two patriarchs: Doug Peters of Peters’ Heat Treating, and Blair Learn of Phoenix Laser Solutions.
Both Doug and Blair are seasoned veterans in their respective industries, and both have children involved in their family businesses in Meadville, Pennsylvania – a mid-sized city about 40 minutes south of Lake Erie and 20 miles from the Ohio state border. These two patriarchs have known each other for years – primarily because Phoenix Laser had been sending heat treating to Peters’ Heat Treating.

Peters’ Heat Treating started in 1979, and here’s Doug Peters with a short history of Peters’ Heat Treating.
Doug Peters (DP): We basically started because there was a need in the area for a commercial heat treater. I heard about it from clients of mine. I was in the insurance business and I finally got tired of listening to everybody saying that the place needed a good heat treater so we started one. That expanded to Erie in ’82, then opened the production plant on 13 acres up here in 2013.
Doug and his wife Jackie have three kids involved in their business: Christopher, who helps with IT and other special projects at the heat treat company, and then husband and wife team Diana Peters Wilkosz and her husband Andy Wilkosz who are both heavily involved in Laser Hard as well as the heat treat company.
The other patriarch in this picture is Blair Learn, father of three boys, Chris, Dave, and Mike, all of whom are owners of Phoenix Laser Solutions. Here’s Blair with a brief history of his family business.

Blair Learn (BL): So we started here in 2008, but we’ve been laser welding for 25 years. We used to have a design and build plastic injection mold hut. We would build high cavitation molds, and we needed a laser there to fix the day-to-day bumps and dings — you know, DCRs and stuff.
Besides the laser heat treating technology, which we’ll get to in just a minute, the thing that excites these two seasoned entrepreneurs is seeing their 20- and 30-something kids run with a new business. Doug Peters says it well.
DP: I think one of the things that’s most interesting to me is that the two patriarchs have stepped back and this company truly belongs to our sons and daughters.
DG: And who are these sons and daughters? Well, there are more than we have time to put in this podcast, but let me introduce them all to you now and then we’ll hear from just two of them.
Introducing Chris Learn and Andy Wilkosz of LaserHard, Inc.
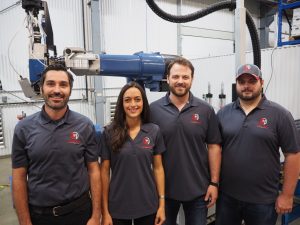
On the Peters’ Heat Treating side of the business is, as I mentioned before, Diana Wilkosz, maiden name, Peters. Diana is the marketing brains behind Laser Hard and oversees marketing, HR, and finance for Peters’ Heat Treating. This is a good time to mention that Laser Hard can be found on the web at www.laserhard.com, a website undoubtedly put together by Diana and her team.
We’ll hear from Diana’s husband, Andy Wilkosz, in just a few minutes.
From the Phoenix Laser Solutions side of the business is two of the three brothers, Chris and Dave Learn. Dave is treasurer and Chris is president. Both of the patriarchs, Doug Peters and Blair Learn, are heavily involved in sales and oversight of the new company.
Now, let’s hear from Chris Learn.
Chris Learn (CL): Yeah, my name is Chris Learn. I’m the owner of Phoenix Laser. And I pretty much oversee the shop floor. Mainly on the laser welding side.
DG: And now, as promised, let’s hear from the spokesperson from the Peters’ Heat Treating side of the business – Andy Wilkosz.
Andy Wilkosz (AW): I’m Andy Wilkosz, vice president of Laser Hard. I also work for Peters’ Heat Treat.
DG: So these are the players. But what about the technology – laser heat treating. Pretty fascinating stuff. Listen as we go back to Andy as he discusses cutting-edge robotics and real-time, feedback-loop pyrometry that makes this laser heat treating system so much different AND BETTER than other laser heat treating systems.
AW: So, I was part of the team that worked on initial startup and all the initial projects associated with the robot and the laser system. Some of the things that set it apart from the traditional lasers and systems that are out in the marketplace now is this has the Fonhoffer Control System so there is onboard optical pyrometry which is a very strong tool for this. A traditional laser is almost like a guess-and-check type of method where you adjust the wattage, see if you achieved the hardness, and in this system, we have the optical pyrometry that has a feedback loop that reads the temperature of the part and then it can control which is really important as a part’s geometry changes. We are going to be able to have better repeatability and control for our customers’ parts. Now, obviously it’s always best if you get one set up part but if the customer just has one part, we are much more likely to get it right and not hurt their part with some of the hazards that could be associated with laser-like melting.
DG: Doug Peters expounded as well on some of the advantages of the Laser Hard heat treating system.
DP: You can locally heat treat parting lines. You can locally heat treat shear areas in a cut off die. You can, instead of having to heat treat the whole part — basically the strength, Doug, is that you can finish a part, we can locally heat treat and then you can put it to work. So the precise heat of a laser enables us to not have to temper everything. In Europe, as they employ this technology, they don’t temper much, if anything because they don’t need to, because of the way this works. Right now I can tell you that the main strength I see in this thing is the precise placement of the treatment, whether it be cladding or heat treating, and the areas that we can direct the beam that you cannot get at with any other technology or method of heating. So, in other words, if you have a blind hole that is two inches deep, I can put a beam into the bottom of the hole and I can harden just the bottom of the hole, and you can’t do that with induction or flame. And with traditional heat treating you are going to have the hard finish cost associated with the distortion as part of the base heat treating cycle.
DG: With laser, you can get in the hole, do the job, and be done with no additional post treatments.
DP: Exactly. And no post hard finish time either — which is huge. The majority of time in building a tool is generally in hard finish time.
DG: And finally, Chris Learn also had something to say about the advantages and application of laser hardening. Chris Learn…
CL: It’s heavily being used in the automotive industry for very large plastic injection tools. So they got this very large plastic injection cavity or core and they are just locally heat treating the parting line and the shut offs. Where before they would have to buy a more expensive material and you know, rough machine it, then heat treat the entire huge block and then finish machine it, you know, with hard milling or eem processes that are very expensive, where now they can just buy a cheaper material, finish machine it and then laser harden just the part you need.
Portability
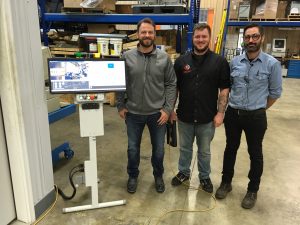
One of the other benefits of this new laser heat treating service being offered by Laser Hard is its portability. Andy Wilkosz commented on the unit’s portability and its potential application in the gear market.
AW: Another powerful aspect of this is we are hoping to really serve the gear market as well. Where in traditional heat treating, what you run is going to be limited on your furnace size. With this robot having the ability to move around — it’s on tank treads — and the range that it can articulate to, you are only limited by what you can get to. So we have the ability to do very, very large parts.
DG: I don’t know if you caught what Andy said. He said that the laser heat treating unit was on “tank treads.” Those tank treads along with a robotic laser heat treating or cladding arm allow the unit to move on-site to where the part is located and once there to move around the part as needed to do whatever process needs done whether it be heat treating or cladding.
As we left the Laser Hard offices and went into the shop to see the unit in action, I asked Chris Learn about the unit’s mobility as well – the ability to take that machine on-site.
CL: So I think the biggest reason for taking this piece of equipment mobile is if the workpiece is too large to transport. Or if it’s too expensive and too risky to transport. So, it’s a very high-cost situation that instead of taking the part here and having us manipulate it here at our shop, even though we have a ten-ton crane, some parts that we deal with are twenty tons, thirty tons. So, it’s a size restriction. Sometimes it’s going to make sense to take this on site.
DG: I next asked Andy to give us a brief explanation of how the unit works. Here’s Andy, and again, please pardon the background noise from the laser welding shop.
AW: Right now, we have a part chucked up in the rotary axis and with the laser scan technology that we have on the laser, it interfaces with the software on the computer and what Mason can do is, we’ll rotate the part, as he rotates the part, it requires image information through the scan and it will actually build a 3D model of the part and its geometry on the computer. Then once we have that on the computer, we can use the computer to draw and program the path of the heat treat or the laser hardening pattern – whether it be a spot or in this case it’s a round bar and what we are going to do is we are going to traverse the bar in a spiral candy cane/barber pole pattern so that you can harden the entire surface. The beam size is about, the max width is, we’ll say 850,000, it’s a little bit more than that but we’ll use round numbers. So if you want to harden an area larger than that, what you end up doing is making multiple overlapping passes.
DG: To actually see the equipment in action, you’ll have to link over to Heat Treat Today’s website and search for Laser Hard. We’ll have an article there with photos of the players and a brief video of the laser heat treating system in action.
Click below or here to view a video of the equipment in action.
Here’s what’s important to remember:
- This laser heat treating and cladding system has a real-time feedback loop that makes it possible to not guess at whether the heat treating process being run is being run correctly.
- This laser heat treating and cladding system is portable and can go on-site to perform any process needed.
- For large parts or for specialty parts where shipping is problematic, this laser heat treating system may be just the ticket you’ve been looking for.
The young team at Laser Hard, backed by the two industry veterans, are bringing an innovative new heat treating technology to the United States.
If you’re interested in knowing more about Laser Hard and the services they provide, feel free to visit their website at www.laserhard.com or contact me directly and I’ll put you in touch with one of the key players. More information, including photos of the Laser Hard team and the equipment, as well as a short video of the equipment in use, can be seen by visiting Heat Treat Today’s website and searching for Laser Hard.
Stop back at Heat Treat Today’s site frequently. We update the site daily with information pertinent to heat treaters with in-house heat treating departments, especially those in the aerospace, automotive, medical, and energy sectors, as well as general manufacturing.
If you’d like to hear more Heat Treat Radio, you can do that in one of three ways:
- You can Google “heat treat radio” – we’re the first thing that pops up,
- You can visit www.heattreattoday.com and find “Heat Treat Radio” under the Resources tab,
- Or, as I mentioned at the beginning of the podcast, you can find “Heat Treat Radio” on iTunes or on SoundCloud.
If you have a specific topic you’d like covered on Heat Treat Radio, please feel free to contact me directly with your suggestion. My email is doug@heattreattoday.com.
Heat Treat Radio podcasts are the sole property of Heat Treat Today and cannot be reproduced without permission and appropriate attribution.
This episode of Heat Treat Radio was produced and mixed by Jonathan Lloyd, Butler, Pennsylvania.
My name is Doug Glenn. Thanks for joining us.
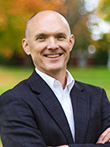
To find other Heat Treat Radio episodes, go to www.heattreattoday.com/radio and look in the list of Heat Treat Radio episodes listed.
Heat Treat Radio #11: Laser Heat Treating with Laser Hard Read More »