Heat Treater To Receive 2 Furnaces
François Studer SA, a Swiss commercial heat treater with 45 years of experience, will advance their hardening capabilities with the order of two furnaces: a vacuum furnace with 15 bar abs high-pressure gas hardening and a furnace for tempering with vacuum purging.
The new solutions from SECO/WARWICK will help increase processing capacity while maintaining the processed element’s high precision and quality. This is important to the heat treater, a hardening plant that processes two truckloads of charges every day.
“We are constantly developing,” commented Francois Studer, CEO of Francois Studer S.A. “We needed to add the capacity to utilize vacuum carburizing, pre-nitriding for carburizing technology and low-pressure carbonitriding, and the new Vector fits these needs perfectly. The retort furnace, on the other hand, significantly increases the hardening plant’s processing capacity in terms of time-consuming tempering and nitriding processes using ZeroFlow technology.”
The vacuum furnace on order by the hardening plant enables efficient processes to be carried out at a vacuum level in both medium and high ranges. The round heating chamber allows for oversized loads. Combined with dedicated LPC, HPGQ technology and a high vacuum system, the furnace will meet the heat treater’s requirements for hardening and carburizing a wide range of various parts.
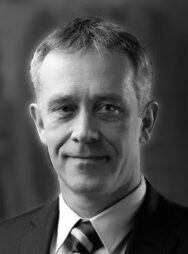
Vice President of Business of the Vacuum Furnace Segment
SECO/WARWICK
The partial pressure system used helps to prevent evaporation and sublimation of alloying elements from the load surface during the vacuum heat treatment or vacuum brazing process. Partial pressure control is important when processing many materials to prevent the heating chamber evaporation and contamination. Isothermal quenching provides control of the cooling process by automatically managing the load temperature and the gas blower motor control using a frequency converter. The carburizing and low pressure carbonitriding (LPCN) options, which the furnace for François Studer SA is equipped with, enables precision processing to increase the steel surface hardness during the entire thermal process.
“The Vector furnace will streamline and increase the hardening process capacity and improve process efficiency. The advantage of this product is a large working space which can be adjusted to an oversized load, using the round heating chamber’s advantages. This is the so-called golden mean for many commercial heat treaters, also because it can be equipped with numerous additional options. With limited production areas, multifunctional, failure-free furnaces are worth their weight in gold for commercial heat treatment,” added Maciej Korecki, VP of the Vacuum Furnaces Team at SECO/WARWICK.
The second furnace on order is a horizontal retort furnace for gas nitriding using ZeroFlow technology and for high tempering with vacuum purging.
The press release is available in its original form here.
Find heat treating products and services when you search on Heat Treat Buyers Guide.Com
Heat Treater To Receive 2 Furnaces Read More »