16 News Chatter To Keep You Current
Heat Treat Today offers News Chatter, a feature highlighting representative moves, transactions, and kudos from around the industry. Enjoy these 17 news items.
Equipment
- Pomini Tenova, which manufactures advanced roll shop equipment, recently signed two contracts for fully automatic roll shop equipment with Baowu of China. The first contract includes a set of four automatic CNC roll grinders with two automatic inspection stations, to be installed at a plant where two new cold rolling mills for silicon steel will be in operation. The second contract includes two automatic CNC roll grinders and an automatic inspection station, equipped with an automatic roll loading system, which will be installed in the roll shop of a new cold rolling mill for silicon steel production.
- Nucor Steel has commissioned SMS group for the modernization and expansion of its Steckel mill at its site in Tuscaloosa, Alabama. The existing Steckel mill will be converted into a tandem Steckel mill, designed to produce high-strength thin strip as well as to boost capacity.
- A global car window manufacturer’s European branch has purchased two SECO/WARWICK technological lines for two of the company’s locations. The order includes RHLE units for bending car windows.
- Jiangsu Dongpu Fine Ceramics Technology Co., Ltd., has installed a hot isostatic press (HIP) from Quintus Technologies. The HIP model operates company’s production line for Si3Ni4 bearing balls in its manufacturing facility in Lianyungang, China.
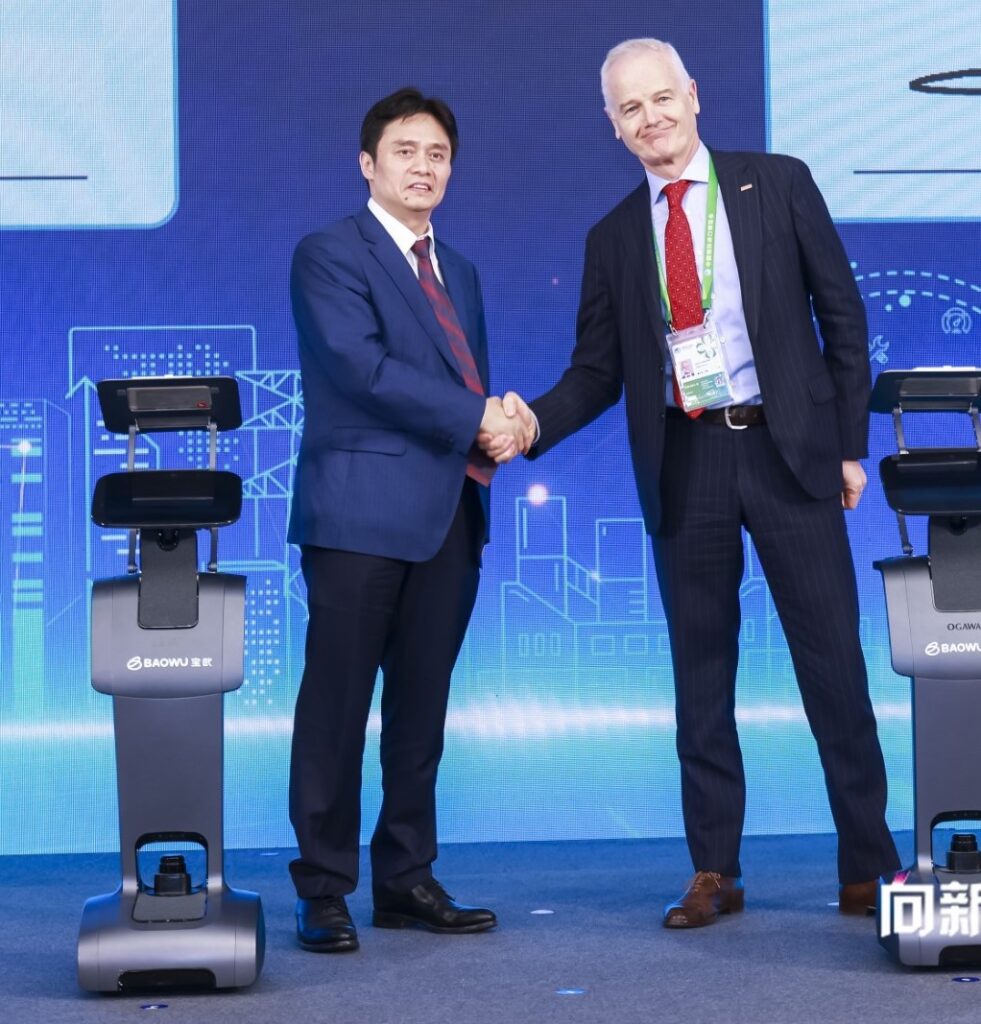
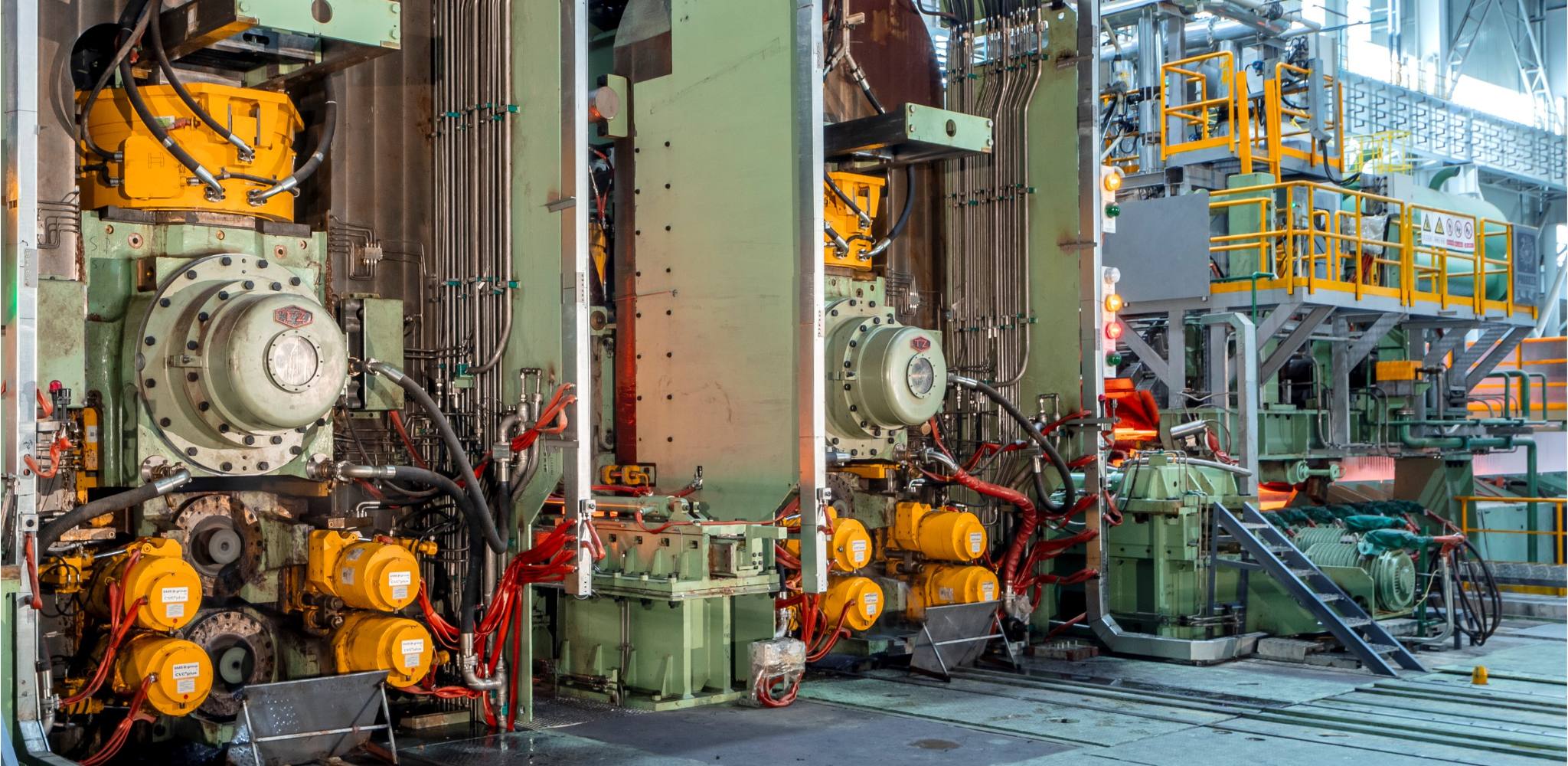

Company & Personnel
- Inductotherm Group has appointed Mick Nallen and Satyen Prabhu as co‐leaders, a transition which became effective July 1, 2024, when Gary Doyon stepped down from his role as CEO. Mick and Satyen have a combined experience at the company of nearly 70 years.
- Vincent Lelong of ECM USA presented on low pressure carburizing with vacuum furnace technology at Purdue University’s School of Materials Engineering undergraduate seminar. This seminar regularly features industry speakers, some of whom are members of the Purdue Heat Treating Consortium.
- The direct reduction plant at Nucor Steel Louisiana achieved a world production record of 330.3 tons per hour of high-quality cold direct reduced iron (CDRI), yielding an outstanding 7,928 tons per day (tpd). A high-quality direct reduced iron (DRI) output with 95% metallization (%M) and a carbon content of 3.3% (%C) was measured. The ENERGIRON technology was jointly developed by Tenova and Danieli.
- Jabil Inc, which designs and manufactures supply chain solutions, announced its acquisition of Mikros Technologies LLC, which engineers and manufactures liquid cooling solutions for thermal management.
- Aerospace Testing & Pyrometry, Inc., (ATP) recently opened its Pacific Northwest office in Seattle, Washington. With this new facility, the company will now have a footprint in all four corners of the United States.
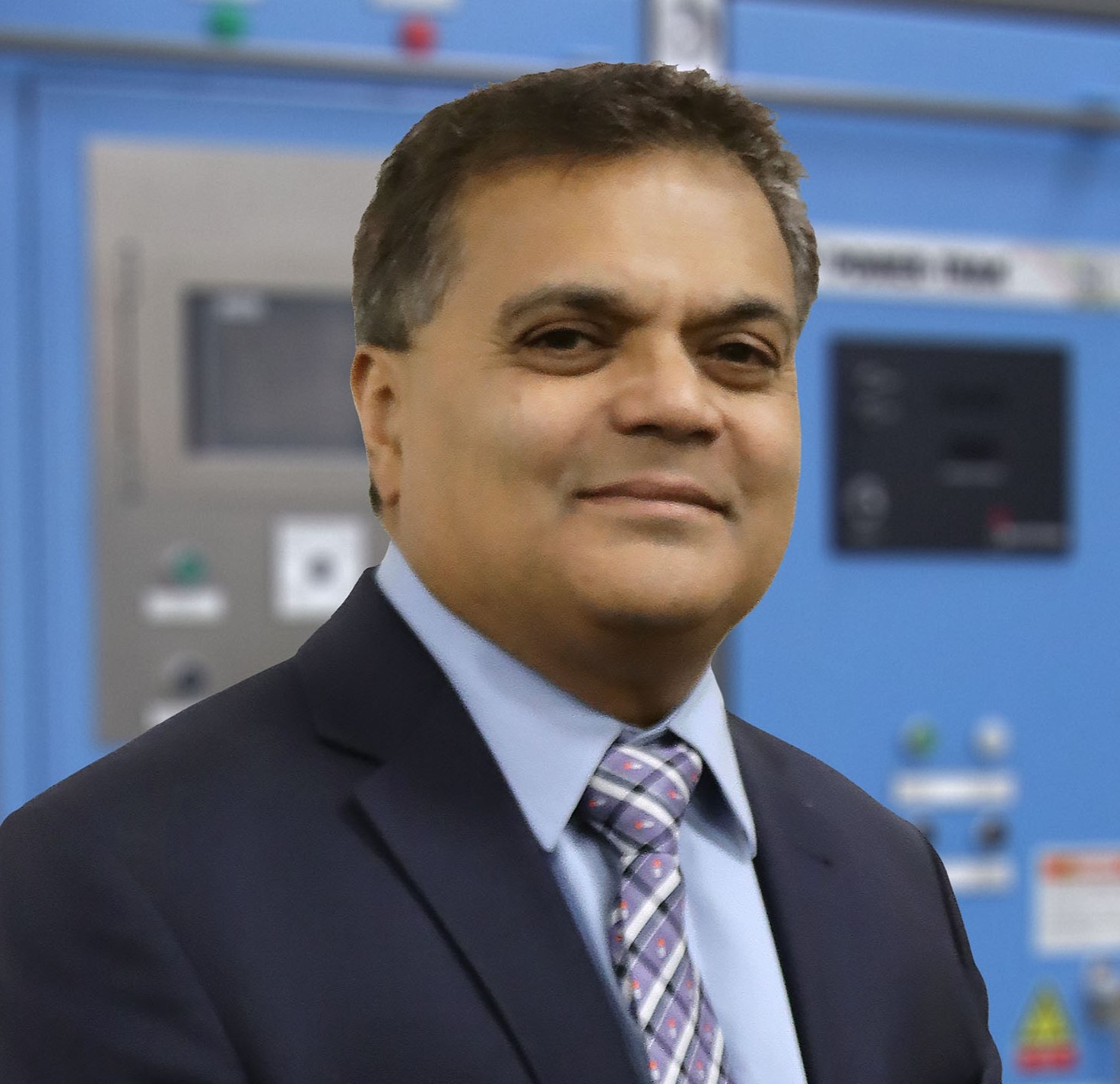
Co-Leader
Inductotherm Group
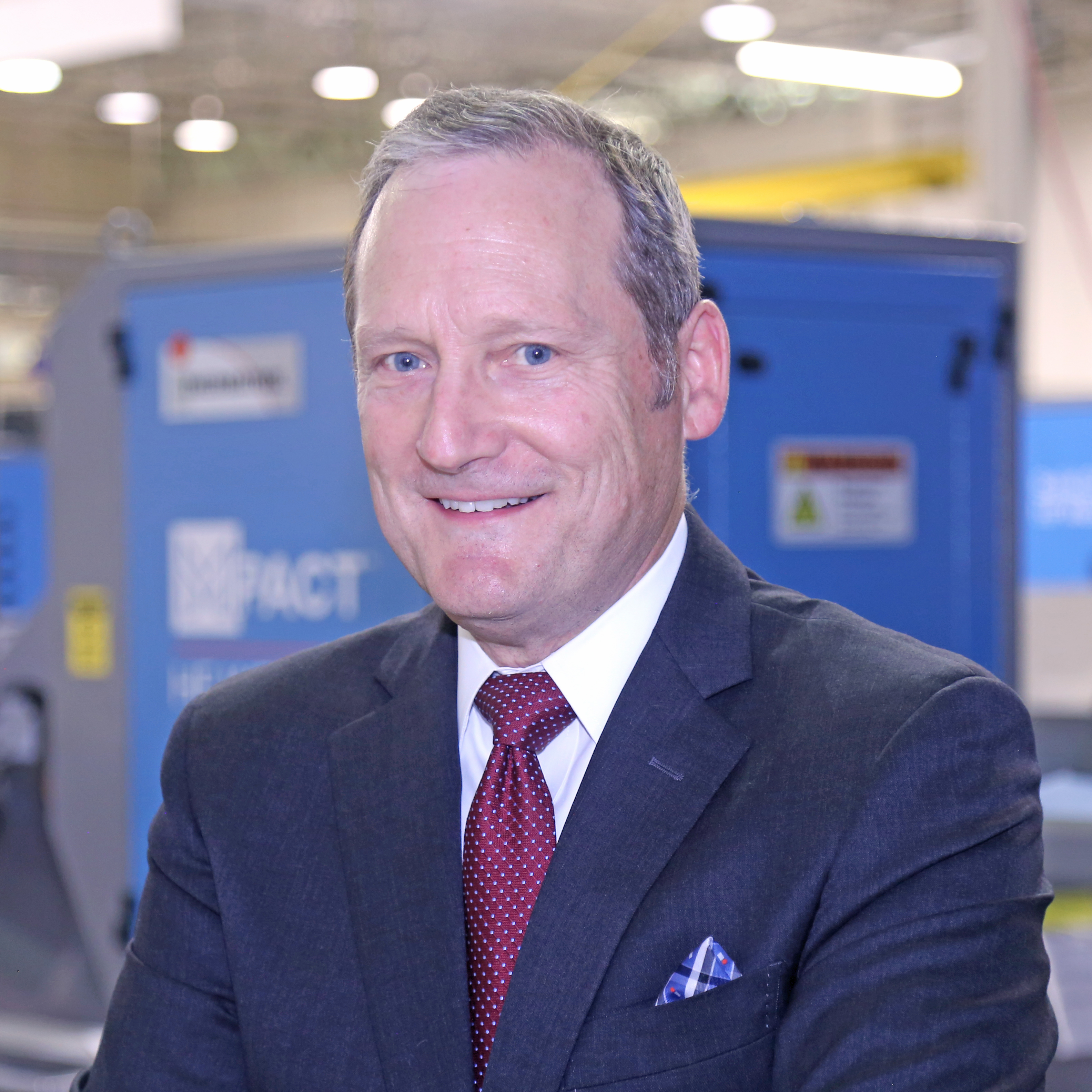
Co-Leader
Inductotherm Group
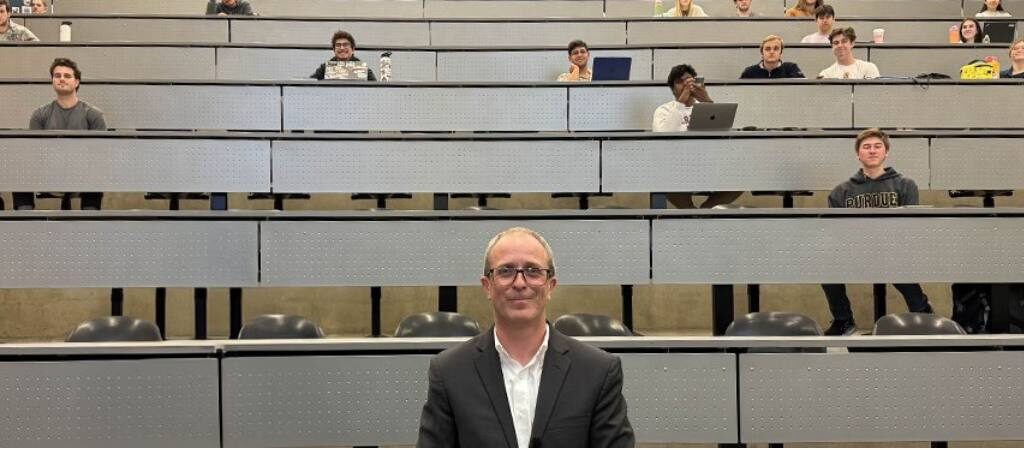

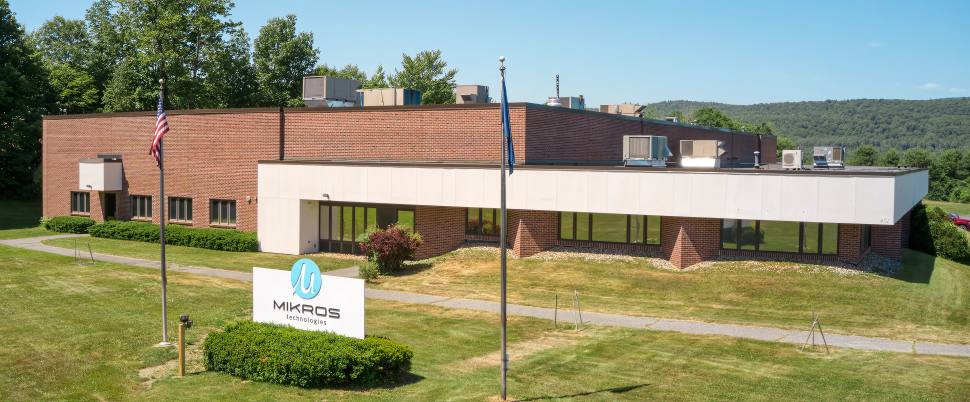

Aerospace Testing & Pyrometry, Inc.
Kudos
- Solar Atmospheres‘ Greenville, SC, facility recently announced it has been awarded Parker Aerospace approval. Its five facilities are now able to assist clients with Parker Aerospace thermal processing requirements.
- Furnace manufacturer Grieve Corporation has reached its 75th year in business. Begun in 1949 as a small job shop in Chicago, the company now occupies a 100,000 square foot facility in Round Lake, Illinois
- StandardAero, an independent provider of engine maintenance, repair and overhaul (MRO) services, recently celebrated the tenth anniversary of its Singapore facility, a Pratt & Whitney Canada Designated Overhaul Facility (DOF) for the PW150A turboprop engine. This anniversary coincides with the company’s redelivery of its 500th PW150A engine, which powers the popular Bombardier Dash 8-400 regional turboprop.
- Paulo’s Cleveland Division was recently awarded approval from GE Aviation for hot isostatic pressing, specifically GT193 Process Code FF.
- C3 Data has achieved SOC 2 Compliance, which ensures stringent standards for handling sensitive data.
- Tennessee Society of Association Executives recently honored Tom Morrison of the Metal Treating Institute (MTI) with the Industry Marketing Award for its Jobs of Tomorrow Workforce Development Program.
- Solar Atmospheres of Western Pennsylvania announced that it has been awarded Pratt & Whitney‘s PWA 11, “Heat Treatments” approval. The facility is now certified to perform heat treatments for P&W’s Suffix 17, “Precipitation Harden,” and Suffix 22, “Austenitize, Quench, and Temper.”
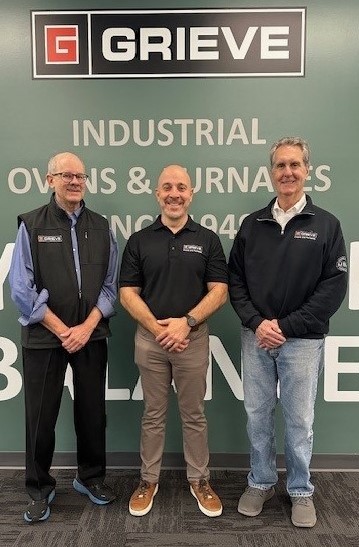
Left to right: Frank Calabrese, vice president; Tony Caringella, president; Doug Grieve, chairman of the board

Find Heat Treating Products And Services When You Search On Heat Treat Buyers Guide.Com
16 News Chatter To Keep You Current Read More »