High-Strength Al-Based Alloys Being Developed for Aerospace and Automotive
A global technology group, an industrial gases company, an additive and design company, and an engineering university in Germany have entered into a research partnership with the end goal of supporting the aerospace and automotive industries through their research and development of aluminum based-alloys.
Oerlikon, a global technology group, entered into a research partnership with Linde, an industrial gases company, GE Additive, an additive and design company, and the Technical University of Munich (TUM), a leading German university in engineering, to conduct additive manufacturing (AM) research with the aim of developing new high-strength, lightweight aluminum-based alloys that can serve the safety and weight reduction needs of the aerospace and automotive industries.
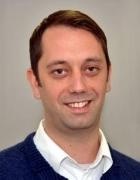
Project Manager for
the AM Institute
This collaboration seeks to address the challenge of aluminum AM. “There are significant challenges during the AM of aluminum alloys because the temperatures reached in the melt pool create an extreme environment that leads to evaporation losses of alloying elements that have comparatively low boiling temperatures — such as magnesium,” said Dr. Marcus Giglmaier, project manager for the Additive Manufacturing Institute and research funding manager. “Additionally, the cooling rates of more than 1 million °C per second, create high stresses during the solidification process, which can cause micro cracks in the solid material.”
The project draws on the strengths of each of its members. Oerlikon’s experience in powder and material science will contribute to the development of the novel material; Linde’s technology and expertise in gas atmosphere control and evaporation suppression during the AM process – including the processing of aluminum-based alloys – overcomes impurities within the print chamber, which will help manufacturers achieve optimal 3D-printing conditions; GE Additive will assist in the collaboration; and, for its part, the Institute of Aerodynamics and Fluid Mechanics (AER) at TUM will be able to provide a detailed understanding of the physical phenomena taking place during the AM process using numerical simulations.
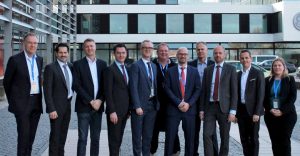
High-Strength Al-Based Alloys Being Developed for Aerospace and Automotive Read More »