Binder Removal in Vacuum Sintering
Source: TAV: The Vacuum Furnaces Blog
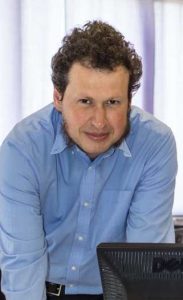
Heat Treat Today previously posted Parts 1 and 2 of this series on vacuum sintering. Part 1 focused on the two processing steps of debinding and sintering. Part 2 addressed primarily the vacuum sintering furnace itself. This installment analyzes the process and variables involved with binder removal.
Andrea Alborghetti, technical manager of TAV Vacuum Furnaces and contributor to the company’s blog, provides an analysis of burning vs capturing binders, addressing advantages as well as problems that may arise and how to execute control in the process, as in this example:
“One thing that is worth clarifying is that the flames usually seen on the outlet of kilns that use combustible gases (hydrogen, for example) as the process gas, were not originally designed to burn the binder disassociation residues to reduce emissions to the legal limits. Rather, it is solely for disposing of the emitted hydrogen safely, thus avoiding hazardous, potentially explosive atmospheric concentrations being created outside of the kiln.”
Read more for further analysis of binder removal, including discerning the type of residue found with your process: “Perfect Vacuum Sintering Step by Step #3”
Binder Removal in Vacuum Sintering Read More »