Tool Steel Potential Dependent Upon Heat Treating
Source: L&L Special Furnace
With its unique ability to be used in the shaping of other materials, tool steel, which includes a variety of carbon and alloy steels, is a particularly valuable property for tool manufacturers as well as manufacturers of components and parts that require the same degree of distinctive hardness, resistance to abrasion and deformation, and ability to hold a cutting edge at elevated temperatures.
The three-phase process of heat treating tool steel — annealed, austenite, and martensite — ensures the tool retains these qualities, achieves intended functionality, and meets performance specifications. In addition,
“The phases that define the process of heat treating tool steel alter the microstructure of the steel itself. Observable under a microscope, heat treatment rearranges the atoms of the iron, carbon, and any other metal components, which serves to give the final material specifically desired properties.” — L&L Special Furnace
Multiple factors can influence the final product, including the appropriate hardening and tempering temperatures depending on the type of steel.
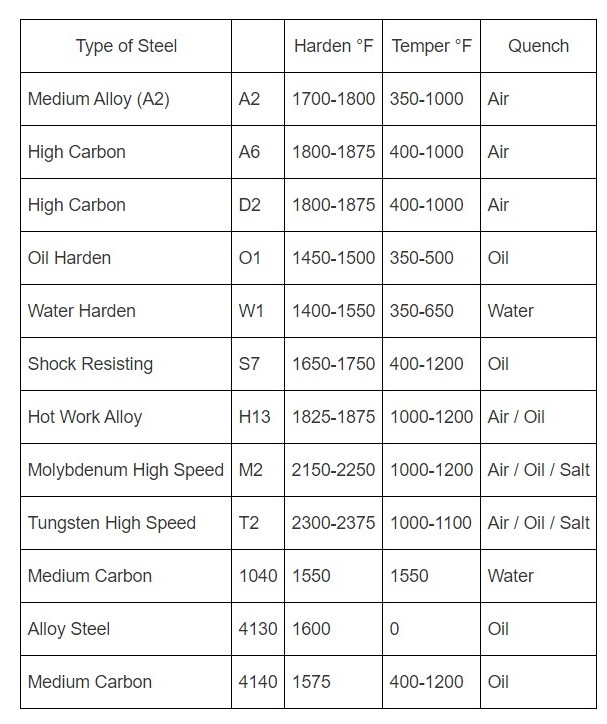
“Heat treating tool steel does more than adding significant value to the treated material—it makes the use of the tool steel possible. Without properly applied heat treating, tools simply wouldn’t work or couldn’t even be made. Modern metallurgical engineering is essential to the production and manufacturing of tool steel and all of its applications.” — L&L Special Furnace
Read more: “The Critical Aspects of Preparing Tool Steels Through Heat Treatment”
Photo credit (main image): Youtube.com and caption: “Visual indication of tool steel phase change to austenite when heat treating. Small pools of iron are forced from the steel as the volumetric change takes place and small amounts of carbon are burned off.”
Tool Steel Potential Dependent Upon Heat Treating Read More »