We’re addressing problems our readers operating older equipment face: Does your safety logic measure up?
This column is a Combustion Corner feature written by John Clarke, technical director at Helios Electric Corporation, and appeared in Heat Treat Today’s June 2023 Heat Treat Buyers Guide print edition.
If you have suggestions for topics you’d like John to explore in the future, please email Bethany@heattreattoday.com.
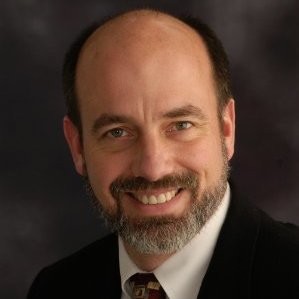
Technical Director
Helios Electric Corporation
Source: Helios Electric Corporation
This month we will break temporarily from our discussion of radiant tubes systems to address a problem faced by our readers who operate older equipment. Does your safety logic measure up? Have you availed yourself of the latest thoughts about how to best construct a safe system?
The National Fire Protection Association (NFPA) publishes various codes and standards to guide the design of heat process equipment. These codes and standards are under constant review by experts in the field and are updated regularly. The latest versions of NFPA 85, 86, 87, and others are readily available for download at nfpa.org/Codes-and-Standards for about a hundred dollars. The investment in reviewing new versions of critical standards provides valuable insight into the thinking of experienced professionals who apply their ongoing experience as they seek to make our combustion equipment ever safer.
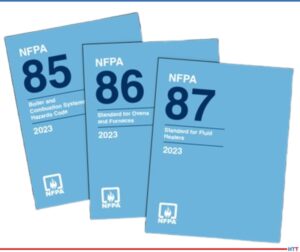
The standards above are generally prescriptive — in that they specify devices and locations, but they also teach the reason behind specific requirements if the reader slows down and thinks logically. An example of this is the requirement in NFPA 86 that states the motor starter which drives the combustion air blower (or other critical devices) be included in the interlock string. If the blower motor pulls too much current, the motor starter’s overload relays trip, shutting off the combustion air blower. A fuel rich condition is prevented because as soon as the blower trips, the interlock string is interrupted and the shutoff valves close, preventing any further fuel gas from being introduced to the system. The code also specifies that a low combustion air pressure switch (or draft switch) be applied; but these devices take time to react to the failure, and with safety logic, the sooner a system is rendered safe, the better.
Monitoring the motor starter and the combustion air pressure switch are on the prescriptive side of the standard, but let us think a bit more about this requirement. Loss of the combustion blower is a critical failure. Are there other failures that can shut off the blower that would not be indicated by the auxiliary contact on the motor starter? If the motor fuses were to blow, or a line of sight disconnect were to be opened, would the interlock detect this failure? What can I do to detect these conditions? Perhaps it would be appropriate to monitor not only the contact on the starter, but the current pulled by the motor using some type of current relay?
The safeties that were installed on my system were good enough when it was manufactured in 1990, why upgrade them now? That is a fair question, but one of those questions that is best answered with another question. Has technology advanced in the last 30 years? Have we gained experience, learned from our mistakes and successes? The answer is yes.
So why not avail yourself of the experience learned by the professionals that volunteer their time to ensure our codes and standards encompass their collective experience? Your assignment is to purchase and download the latest version of the applicable codes or standards and take the time to review them. The reading is pretty dry, but the payoff can be extremely beneficial.