Titanium Producer Boosts Melt Capabilities with New Furnaces
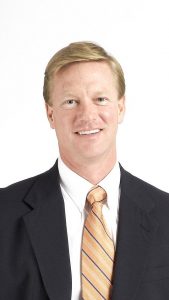
Perryman Company, a metal fabricator headquartered in Houston, Pennsylvania, recently announced it will more than double its current titanium melting capacity through the addition of two new furnaces, one electron beam (EB) and one vacuum arc remelt (VAR).
The integrated titanium producer from melting of ingot to finished products has existing melting facilities at its western Pennsylvania location which are utilized for projects in the commercial aircraft and medical sectors. The company expects the new furnaces to alleviate backlog and support demand for titanium products in these as well as other industrial, recreation, and infrastructure industries.
“Our aerospace forecast model indicates there will be a need for additional melting capacity. With the increased capacity we will be in position to pursue segments of the aerospace market where we have not yet been a participant. We believe there’s more opportunity for us to leverage our fully integrated capabilities,” stated Frank Perryman, president and chief executive officer of Perryman Company.
The added capacity will also support planned growth in medical, additive/3D and other emerging markets.
Installation of the new furnaces will begin in late 2018 and are expected to be fully operational by mid-2019. Once complete, the company’s total melt capacity will exceed 26 million pounds, placing Perryman among the world’s largest melters of aerospace quality titanium.
Titanium Producer Boosts Melt Capabilities with New Furnaces Read More »