Welcome to another episode of Heat Treat Radio, a periodic podcast where Heat Treat Radio host, Doug Glenn, discusses cutting-edge topics with industry-leading personalities. Below, you can either listen to the podcast by clicking on the audio play button, or you can read an edited version of the transcript. To see a complete list of other Heat Treat Radio episodes, click here.
Audio: C3 Data
In this conversation, Heat Treat Radio host, Doug Glenn, interviews Nathan Wright of C3Data, a company based in Indianapolis, Indiana, which assists heat treaters and calibration labs ensure furnace compliance with Nadcap, AMS2750 & CQI-9. Their discussion about how you can cut the amount of time you spend testing and repairing furnace calibration report for your CQI9 and NADCAP compliant furnaces — from what might currently be up to an hour or more, per furnace, to somewhere down around five minutes per furnace — will help you imagine the day when you can have a single dashboard in your office where you can see in real time whether your furnaces are currently compliant with those standards or your own custom standards. Imagine not having to guess if your furnace is compliant or having to wait until the next SAT or TUS is performed to find out that you just ran two or three loads in a furnace that is out of spec. Also, imagine being able to click a few buttons and have a fully code compliant report printed out in minutes for when the auditor shows up at your door. After listening to today’s Heat Treat Radio podcast, you’ll be one step closer to making this a reality in your shop.
Click the play button below to listen.
Transcript: C3 Data
The following transcript has been edited for your reading enjoyment.
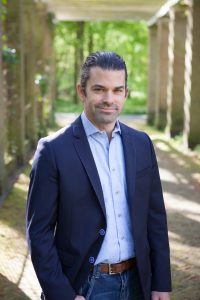
Welcome to Heat Treat Radio. I’m your host and publisher of Heat Treat Today, Doug Glenn. Before we jump on the phone with Nathan Wright, of C3 Data, let me encourage you to visit www.heattreattoday.com for more helpful heat treat information. Manufacturers with in-house heat treat departments, especially in the aerospace, automotive, medical and energy sectors as well as general manufacturing, find this site especially helpful. Every weekday, at least one new piece of technical or commercial news is posted to the site. The site also includes a new feature: Heat Treat Consultants. If you have ever wondered where you can find a simple, concise list of heat treat consultants, check out Heat Treat Today. You can find it on the site under the “Resources” tab. Today’s Heat Treat Today radio episode is brought to you by Dry Coolers. Designers and builders of industrial cooling systems and the professional engineering services surrounding those systems. As a leader in the heat treat industry for decades, they are located in Oxford, Michigan, and supply cooling systems for the aerospace, automotive, medical and energy industries plus many others. If you have an industrial cooling need, call Dry Coolers. They are on the web at www.drycoolers.com. Or you can reach them by phone at 800-525-8173.
Heat Treat Radio jumped on the phone and called Nathan Wright to discuss this new technology. Here’s a lightly edited version of our conversation. Nathan is a long-time pyrometry guy with multiple pyrometry labs around North America, including a lab in Mexico. With several decades of experience in the industry, Nathan was pretty convinced there was a better way to do pyrometry and furnace compliance. Here’s Nathan to explain what it is, exactly that his company, C3 Data does for the heat treat market.
Nathan Wright (NW): Heat treaters and other companies come to us to help them reduce the cost to comply with NADCAP. So if you are a NADCAP heat treater, and or trying to become compliant with CQI9, you are an ideal client. So, companies come to us to help them reduce the cost associated with trying to comply with those two specifications, specifically with respect to the pyrometry requirement; so, in terms of time and money spent, we help them reduce those costs. We do this by leveraging two very simple technologies: the cloud and mobile devices. And we use these to eliminate virtually all of the time spent writing reports and calculating correction factors and ensuring that all the equipment that you use is compliant. We build these higher specs into the software so that all the end user has to do after they set their exponents is plug in the readings, and we do the rest.
Doug Glenn (DG): And it’s cloud-based?
NW: That’s correct. It’s cloud-based in terms of where all the data is stored. But we do have, as I mentioned earlier, the mobile technology that is used, sort of a modern-day version of the clipboard. When a pyrometry technician is out in the field, rather than writing down on a piece of paper or lugging around a laptop with an excel spreadsheet, there is an app specifically designed for those types of testing requirements. And that’s done all on the mobile device. The app really knows everything about the furnace when you walk up to it. We integrate QR codes into our calibration labels that get printed, and simply by scanning the barcode on the furnace, the app knows everything about your furnace from the furnace class to the operation ranges to the instrument types, the calibration points, everything about it. So, in terms of training and the technician making sure that that furnace is tested and compliant with the specs, it’s kind of a no-brainer. Walk up, scan the QR code, and the app kind of walks you through a tutorial step by step, and at the end, it gives you sort of a green means go, red means no indicator as to whether or not the test that you are performing passed or failed.
DG: I understand the spec is built right into the app. So, if, or should I say when, the spec is updated, your app is updated and the end user pretty much automatically has the new spec immediately on his device.
NW: That’s correct. And we intentionally sit on a couple of the committees — CQI9 as well as the AMAC committee — when you talk about AMS . . . really just to participate in the conversation to understand what changes are being made to the new revisions of both of those specifications. So, proactively, we have our coders in the background sort of prewriting some of the code that may or may not become part of the specification. So that from day 1, all the customer would have to do is refresh their web browser (for the web version), and on the mobile app version they simply do the auto update on their app, and they know moving forward that every test they do from that day forward is in compliance with what will be the AMS 27 revision F, and of course with CQI9, it will be rev. 4. So, yes, we address those concerns by being actively connected with those communities and ensuring the software automatically gets updated.
A Better Way: The Story Behind C3 Data
DG: So, tell us a bit about how this all came about. And also about you.
NW: I started doing pyrometry work, I’d say calibrations, surveys, and SATs, approximately twenty years ago. And I always had in my mind that there had to be a better way of doing this type of testing. Having sat in literally hundreds of NADCAP audits myself, there’s just a lot of human error that goes into — I guess the root of the non-conformances, and I even tried to bring a C3 Data like product to life back in the most powerful hand-out tool that you could get — a palm pilot. So, you can see that I’ve been thinking about this in depth for quite a while. And anyone who’s ever had to do an SAT, and all that’s required to make sure the equipment is current and then actually doing the reporting, knows the agonizing pain that goes into doing this type of testing. So, after twenty years of doing that I have a unique perspective on how to build this from the industry. So we started building the product, the C3 Data product, for our own pyrometry labs. I’ve been doing this for twenty years. I own two labs, and as I mentioned earlier, we just wanted to build a tool that would eliminate most of the arduous and daunting parts of the pyrometry compliance. Anyone who is responsible to comply with NADCAP, CQI9 – they know that it’s the paperwork administration, it’s the scheduling, and frankly, sometimes it’s just the math. So, in a sense, we can honestly say that we built this product with each customer in mind because we do the same things that they do and we initially built it for us. It’s pretty exciting to get the word from our subscribers that they are saving a lot of time and eliminating the NCRs. I talk about saving time. . . . We’ve had customers tell us as much as 60 percent of the time that they were spending doing testings and reportings, has been reduced by 60 percent. We are pretty excited about those numbers.
DG: I imagine it’s not only the time savings that is a real benefit, but the peace of mind knowing that you are compliant – especially when the auditor comes a-knockin’!
NW: Yes, I would say that the most comforting feeling — from one of our subscribers – is going into a NADCAP audit knowing, with confidence, that all the information that is required is there. Not only is it there, but it is all compliant. No matter what report you pull up, whether it’s a certification for a thermocouple or for a daylogger or for a field test instrument. Any type of test result is insured and guaranteed to be compliant because the system is built around those specifications and doesn’t allow you to make some of the most common mistakes that are attributed to about 50 percent of the non-conformances really are pyrometry related. So the confidence that the end user has is really high going into an audit. And anyone that has been in an audit knows that that is the most nervous day.
DG: You mentioned “we” when you were talking about the company. Tell me a bit about the company now. You have some pyrometry labs, correct?
NW: We do, we have a couple of laboratories. One in Mexico, one in the midwestern part of the United States, but in the last three years, I’ve sort of taken a back seat to those companies in order to really focus on C3 Data. We’re headquartered in Indianapolis and the product has actually been under development for about five years although it has only been commercially available, I guess, going on now about three years. So we employ a staff of five here in the U.S., and more recently we’ve established sales and support channels in Europe – covering the UK, France, Germany, Italy, and Spain. So, we are excited about that new relationship and getting that product in the hands of a large segment of the heat treat world over there.
DG: Are there different standards there in Europe? Or are they all the same?
NW: No, No. Very similar. I mean, it’s the AMS 2750 for NADCAP accredited companies and CQI9 for the automotive. In fact, well, CQI9 was authored by the big three here in the U.S., and for several years, Europe was not really recognizing that standard and more recently with several automotive recalls in Europe from European manufacturers, they were really looking for a way to minimize the large expense associated with those non-compliances and recalls. And so, they really have, in the last nine/ten months – more recently — started to adopt CQI9 pro-actively because rather than write their own specifications they wanted to adopt it. So we are pretty excited that we don’t have to customize the software for yet another specification. I will say, speaking of custom specification, the software is not limited to just AMS and CQI9. We do have a build-your-own spec feature that is built into C3 Data that allows you to take a Boeing spec that by and large is AMS 2750 but has its own nuances that are associated with an individual prime like Boeing, just to use them as an example. And so we allow users to go in and build their own specifications to ensure compliance to not just the prime specifications that we typically think of (i.e. AMS and CQI9).
DG: And now for a quick reminder that this episode of Heat Treat Radio is being sponsored by Dry Coolers. Dry Coolers can provide open evaporative towers, closed loop evaporative towers, air cooled or dry cooler closed loop systems, chillers, vapor coolers and condensers, pumping stations, control panels, emergency backup systems, filtration and solids removal equipment, as well as complete plant-wide water systems. If you have any industrial cooling need, call Dry Coolers. They are on the web at www.drycoolers.com or by phone at 800-525-8173.
C3 Data in Action
DG: So, Nathan, how would this look for a heat treater? How do they interface with C3 Data? You mentioned subscribers.
NW: It’s set up as what we call “software as a service”. So, unlike a traditional software product where you buy it once and own it, and then pay for incremental updates, we just have a subscription service that the user can customize based on their needs. If you are just using the software to perform SATs, there is a fixed monthly fee. But if you wanted, a year later, to add temperature uniformity surveys, or instrument calibration, you can incrementally bump up and add on plugins to the software. It’s all web-based so the beauty of this is that there is no IT that needs to be involved. There’s not a lot of technology that the end user needs to have other than how to go to the website and log in to their password-protected account. You can increase or decrease your subscription levels at any time and it’s month to month. There are a lot of advantages to this software model because it is low risk. You can try it out. You can cancel it a month later and decide that it’ not for you. So, we like that. The biggest, most powerful part of software and servers being web-based is, as we mentioned when these specifications get updated, we can simply update them in the background and the end user just has to refresh their browser and instantly the update is made. The system is very intuitive. By the way, the subscription service comes with unlimited phone and email support. So, as you bring on new users, we will train them. This is typically done through a “go to meeting” online, so there is no need to incur travel expenses. And we can do a twelve-minute meeting, we can do a two-hour meeting with a large group if we need to. We can customize the training based on the skill set of the group or group of individuals that are using the software.
But in terms of the setup, I think the biggest hurdle is getting all the information into the system. The system only knows what you tell it. So, there is a section in the portal where the user can go in and must go in and define all the furnace settings. So, we talked earlier about instrument types, operating ranges, furnace classes, all those types of things. Once you define all those, what we call furnace set up variables, the system will hand walk you through everything. I guess my only point is that there is a little up-front investment to populate the user account with all the furnace and instrument information. That’s probably the biggest hurdle for any user because we have knocked down all the other hurdles – the training, the updating of the software as we mentioned is a simple refresh of the browser. So, it’s very intuitive but there is a little bit of upfront time involved – and we say about five to ten minutes per furnace is the typical amount of time spent and that can be reduced over time by getting people familiar with the software. So, if you are a typical, well I shouldn’t say typical because there is no typical heat treat size, but a heat treater that has ten furnaces, it might take you a couple hours to populate your system.
DG: Well, five to ten minutes per furnace does not sound like much. Tell us a bit about this dashboard.
NW: Dashboard culminates all the information that’s being populated in a single system, and it gives the ability to display a real-time plant overview of all the furnaces and their real-time compliant status against the specifications. So, we have customers out there currently that have 60- to 70-inch television monitors displaying the C3 dashboard. And in their procedure, the operators of the furnaces are told that before they load a furnace, the first thing that they do is that they look at their C3 Data dashboard and they verify that that furnace is either green, yellow or red. Depending on the company, they may have different protocols, but ultimately if it is red, you are supposed to stop as the furnace operator and go to your boss and say, “Hey, I can’t load this furnace because it is not compliant. What should I do?” And, there is a lot of power in that because, you know, currently the systems that exist today are spreadsheets or, worse yet, printed pieces of paper that just sit stagnant in a filing cabinet and they don’t tell you anything in real time. Meanwhile, furnaces are being loaded — potentially furnaces that are not compliant — being loaded with product that are safety critical parts for the aerospace and automotive industry. So, dashboard really takes that culmination of a lot of details of compliance-related information and gives it to you instantaneously. This also gives the ability for a quality assurance manager of a company that may have multiple locations to sort of figure out where he or she should be focusing their efforts on helping with furnace compliance. Case in point, if you have seven different facilities that you are responsible for as a quality assurance manager, you are going to want to go to those places where more furnaces are red and not really spend any of your time in those locations where all those furnaces are green. And so this allows them to have that real-time visibility without ever leaving their desk and make real-time decisions about where they need to focus their time and energy.
DG: Any specific heat treaters that will find this system helpful? Or is it pretty much broad-based?
NW: Generally speaking, any heat treater that needs to ensure high quality should be using a system like C3 Data. And many do. The problem is that most people have failed at what we call rolling their own. These systems range the gambit. They are also susceptible to the same issues. Namely, the cost to manage these cobbled together mixtures of cell spreadsheets, and outlook for scheduling and other tools that they combine and rely on, and there is usually what we call the “key man” risk associated with these systems. And that employee may or may not always be employed there to keep the system up to date. So this usually causes frustration and ends up costing much, much more than people think. But, to be specific to your question, the customers that are NADCAP, or just simply required to comply with AMS 2750 or CQI9, they rely on the software and so any customer that’s, as we mentioned, that’s looking to comply with those specifications, C3, all those specs are included out of the box with C3. That would be our ideal demographic.
DG: Anything else like it in the marketplace? And if so, how does C3 differ?
NW: There are a few companies that have attempted to build what C3 Data has. But I would say that they all suffer from the same two problems. Their software was not built around the prevailing specifications like the AMS and CQI9, as we keep mentioning. And secondly, they were built by people that don’t do pyrometry. So, the user experience quickly becomes frustrating for people using the competition’s product. Because, unless you have done this type of work, it’s really impossible to know all the limitless permutations of the spec and account for them all. So, their software ends up running you instead of the other way around. Another thing that is unique about C3 is that we allow the user to fully integrate with existing service providers and vendors. For example, if you had a lab that is coming in on site to perform your calibrations, their reports will automatically funnel in to the C3 account. And they are available in real time. So, that’s one. I mean we integrate with sensor vendor. GeoCorp is one of our sensor vendors. When you buy a thermocouple from GeoCorp, and you have a C3 Data account, your sensors will automatically get pulled into your C3 Data account. Including all the correction factors and the math associated with the rounding and all that, so there is a lot of integration with the vendors and service providers – including data logger manufacturers. But there are some major data logger manufacturers that integrate directly with our temperature uniformity survey software that, again, all that calibration data for those loggers technically can go into our system as well as generating temperature uniformity survey reports that are fully compliant in less than five minutes. So, this is a big one. I think there are listeners out there who have done surveys know that a survey report can take, and it varies depending on your experience and what systems you have, but it can take anywhere from 20 to 45 minutes and even sometimes an hour just to do a report. We can consistently offer a product that does this in less than five minutes and guarantee its compliance. But I think our biggest competitor is really not a company, it’s the status quo. People who are “getting by” with their in-house systems and they don’t know what else is available and they don’t realize the tremendous cost they currently are incurring doing it the way they have always done it. So, that is probably our biggest competitor – getting past the “If it ain’t broke, don’t fix it” type of mentality.
Nathan didn’t want to name drop during the podcast but shortly after the interview, Nathan informed me that C3 Data signed a distributor agreement with CCPI Europe, Limited – to represent C3 Data in Europe. CCPI will do essentially the same thing in Europe that Geocorp does here in North America. CCPI Sensors will integrate directly with C3 Data for customers in that part of the world.
DG: And how about when the auditor walks in. Do most of them accept your reports?
NW: Most auditors have accepted it. We are trying to get the word out to a lot of the NADCAP auditors that this is a user-friendly system and that it can be trusted. As a result of some of the feedback we have gotten from some auditors we’ve built in some, I guess, “check your math here” kind of thing — they want to know — yes, it says that the test passed because I see the number turns green instead of red but how do we know that? And so we’ve built in some software validation tools in there for NADCAP auditors to become more comfortable by seeing the math behind the numbers. As well as for our users. But, yes, you are right. The most rewarding moment is the day of the NADCAP audit, you can go to the single screen where you have scheduler and tests. You have one system. Not a filing cabinet, not an excel spreadsheet and another spreadsheet on a different file server. It’s one system accessible anywhere on the web that you can go and have a NADCAP audit. You can personally have a NADCAP audit remotely. In an ideal world, that might be something that is considered by PRI someday but the beauty is, yes, it’s in one location. You are never chasing down paper. And the bottom line is you know that it’s all compliant – 100 percent of the time.
So, if you are a captive or commercial heat treater looking for smart ways to reduce your compliance investment, you might want to take a look at C3 Data. Here’s a system that could significantly reduce the time you invest in conducting the litany of compliance tests required and the time it takes to prepare those time-consuming reports after each test. Better to let C3 take care of it. If you’d like to contact Nathan, feel free to email me directly and I’ll put you in touch with him. You can email me at Doug@heattreattoday.com. C3 Data is on the web at www.C3data.com. And you can reach out to Nathan that way as well.
Special thanks go to Dry Coolers, Inc., for their support of Heat Treat Radio and for their sponsoring this podcast. Dry Coolers, industrial cooling systems, made to order. Dry Coolers is on the web at www.drycoolers.com.
Don’t forget to visit www.heattreattoday.com frequently. We post a new heat treat industry item – either a technical article or some industry news — every weekday. If you would like more Heat Treat Radio, simply google Heat Treat Radio. We are the first thing that pops up. Or, you can also subscribe to Heat Treat Radio on iTunes or Soundcloud. This and every other episode of Heat Treat Radio is the sole property of Heat Treat Today and may not be reproduced without express written permission and appropriate attribution from Heat Treat Today. Jonathan Lloyd of Butler, Pennsylvania, produced and mixed this episode. I’m your host, Doug Glenn. Thanks for listening.
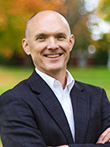
To find other Heat Treat Radio episodes, go to www.heattreattoday.com/radio and look in the list of Heat Treat Radio episodes listed.