Jason Schulze on AMS2750E: Examining Requirements That Apply to TUS Thermocouples
This is the sixth in a series of articles by AMS2750 expert, Jason Schulze (Conrad Kacsik). Click here to see a listing of all of Jason’s articles on Heat Treat Today. In this article, Jason advances the discussion of TUSs with an examination of requirements that apply to TUS thermocouples. Please submit your AMS2750 questions for Jason to editor@heattreattoday.com.
Introduction
Any technician who has performed a temperature uniformity survey understands that the assembly, use, and placement of thermocouples are imperative to the success of the TUS.
As we move through the requirements of Temperature Uniformity Surveys, in this installment we examine the requirements which apply to TUS thermocouples.
TUS Thermocouples Re-Use, Quantity, and Arrangement Requirements
TUS Thermocouple Re-Use Requirements
AMS2750E, paragraph 3.1.3, can be difficult to understand at times. To start, it’s important to understand the difference between expendable and nonexpendable thermocouples.
Expendable Thermocouples:
“Thermocouples made of fabric or plastic covered wire. The wire is provided in coils or on spools. Insulation usually consists of glass braid or ceramic fiber cloth on each conductor plus glass braid overall.”
Nonexpendable Thermocouples:
“Thermocouples that are not covered with fabric or plastic insulations. One type consists of ceramic insulators over bare thermocouple wire, sometimes inserted in a tube for stability and protection. A second type consists of a combination of thermocouple wires, mineral insulation, and a protecting metal sheath compacted into a small diameter. The thermocouple thus constructed is protected, flexible and, within the temperature limits of the sheath material, may be used many times without insulation breakdown. This type of thermocouple, conforming to ASTM E 608, is available under many trade names.”
Once these definitions are understood, we focus on paragraphs 3.1.3.3, 3.1.3.4, and 3.1.3.5 carefully to ensure you apply the correct usage allowance to the correct thermocouples.
Paragraph 3.1.3.3:
“Expendable test sensors may be reused if ‘U’ in the following formula does not exceed 30. A ‘use’ for test thermocouples is defined as one cycle of heating and cooling the thermocouple (2.2.77). U = Number of uses below 1200 °F (650 °C) + 2 times number of uses from 1200 °F (650 °C) to 1800 °F (980 °C). Expendable base metal test thermocouples shall be limited to a single use above 1800 °F (980 °C).”
Notice the paragraph begins with the term “expendable test sensors.” This prohibits the U-formula from governing the replacement frequency of nonexpendable test sensors as well as expendable sensors which are not used as a test sensor.
Paragraph 3.1.3.4:
“Any base metal TUS thermocouple that is (1) used exclusively under 1200 °F (650 °C), (2) identified, and (3) preserved/protected from damage (i.e., crimping, excessive moisture contact, corrosion, etc.) between tests or remains installed on a rack that is protected between tests,) shall be limited to no more than 90 uses or 3 years, whichever comes first and may be reused subject only to the limitations of 3.1.3.1 to 3.1.3.2.”
This paragraph begins with “Any base metal TUS thermocouple.” This would apply to any base metal thermocouple (i.e. Type K, Type N, etc.) used for a TUS, whether expendable or nonexpendable.
Paragraph 3.1.3.5:
“Nonexpendable base metal TUS thermocouples reinstalled for each TUS through ports in the furnace, used in the same location and depth of insertion for each TUS and used exclusively under 1200 °F (650 °C) shall be limited to no more than 90 uses or 3 years, whichever comes first and may be reused subject only to the limitations of 3.1.3.1 to 3.1.3.2.”
This paragraph is very specific regarding its application. For this paragraph to apply, the supplier would need to be using a) nonexpendable thermocouples that are b) base metal, which are c) reinstalled through ports in the furnace and used (non-resident) d) at the same location and e) depth of insertion.
Suppliers interpreting the usage requirements of test thermocouples should pay close attention to Figure #1 in AMS2750E. Figure #1 lays out the usage requirements of AMS2750E in an easy-to-read format that can be used as a quick reference.
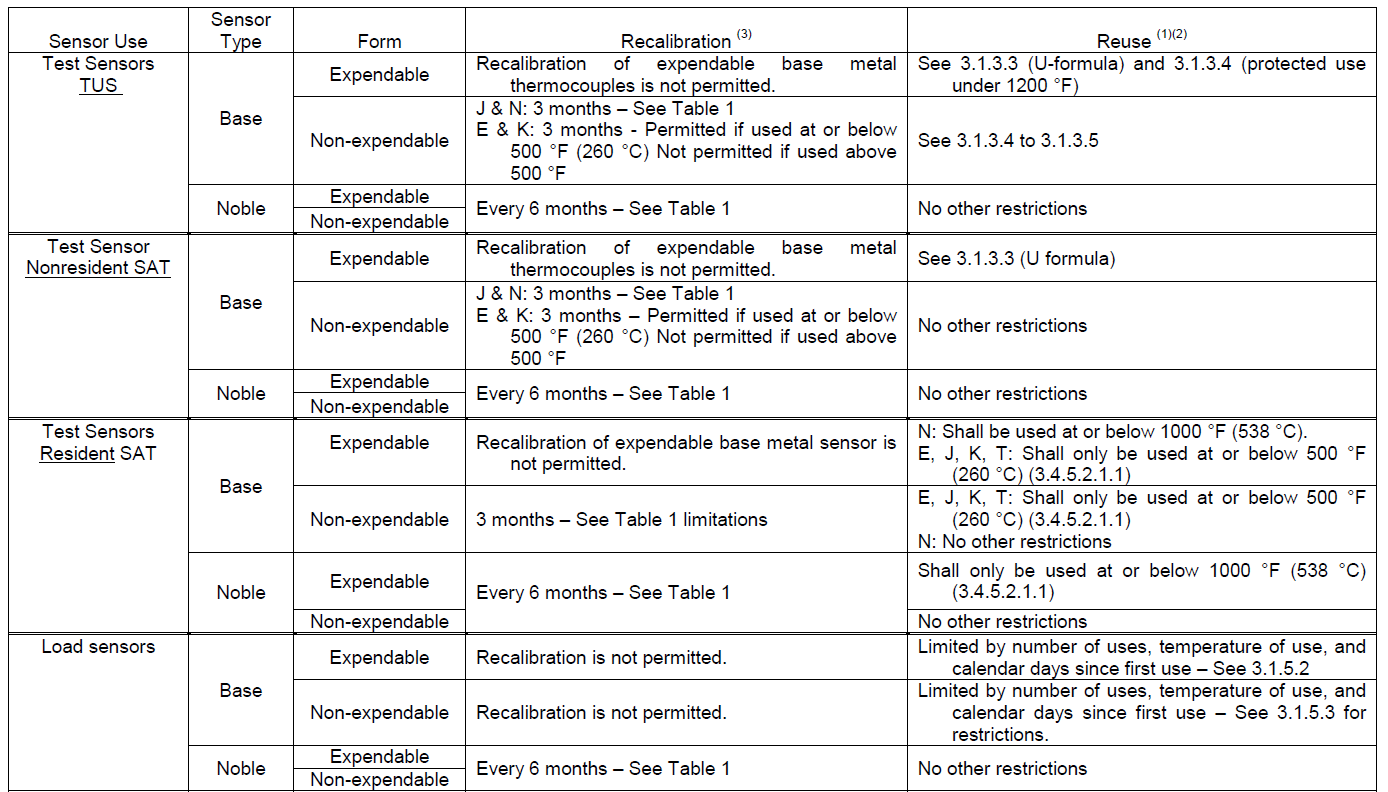
TUS Thermocouple Quantity Requirement
AMS2750E, page 27, paragraph 3.5.13.1, states that the number of TUS thermocouples shall be in accordance with Table 11. The top 2 lines reflect the most widely used. (See Figure 2.)

The amount of test sensors is based on the cubic foot of the qualified work zone. This should not be mistaken for the cubic foot of the heating area in the furnace, or control zone, as the full heating area is not always the size of the qualified work zone.
Table 11 begins by categorizing the options as “Workspace Volume Less Than.” Once your qualified work zone is established, you will need to apply that to the table to determine how many TUS thermocouples will be needed. As an example, if your qualified work zone is 562 cubic feet, you would need a minimum of 19 test thermocouples distributed throughout the qualified work zone during the TUS.
TUS Thermocouple Placement Requirement
Thermocouple placement is described in AMS2750E paragraphs 3.5.13.2.1 and 3.5.13.2.2. Paragraph 3.5.13.2.1 relates to the thermocouple placement for qualified work zone volumes that are less than 3 cubic feet. Typically, this would apply to small air furnaces or laboratory furnaces used for testing, although could very well apply to smaller atmosphere or vacuum furnaces. Each paragraph describes the requirements for a rectangular qualified work zone and cylindrical qualified work zones.
Paragraph 3.5.13.2.1
“For furnace work zone volumes less than 3 cubic feet (0.085 m3), four TUS sensors shall be located at the four corners and one at the center. If the furnace work zone volume is cylindrically shaped, four TUS sensors shall be located 90 degrees apart at the periphery and one shall be located at the center. In both cases, all TUS sensors shall be located to best represent the qualified work zone.”
To better describe the requirement within this section, I’ve included a diagram of the requirement for both rectangular and cylindrical qualified work zones.
The location is a requirement, although the numbering sequence identified in these diagrams is optional and the supplier has the freedom to number the locations as they see fit.
“For furnace work zone volumes greater than 3 cubic feet (0.085 m3), eight TUS sensors shall be located at the corners and one shall be located in the center. If the work zone volume is cylindrically shaped, three TUS sensors shall be located on the periphery of each end, 120 degrees apart. One of the remaining TUS sensors shall be located at the center; the other two shall be located to best represent the qualified work zone. For furnace work zone volumes greater than 225 cubic feet (6.4 m3), the additional TUS sensors required by Table 11 shall be uniformly distributed to best represent the qualified work zone. When radiant heat from the periphery of the work zone is used to heat the product, the additional sensors shall be uniformly distributed at the periphery of the work zone.”
Again, the diagrams to the right better describe the requirements within paragraph 3.5.13.2.2.
Conclusion
Now that the TUS thermocouple requirements have been established, we will move on to the requirements of initial and periodic TUS requirements in the next article.
Submit Your Questions
Please feel free to submit your questions, and I will answer appropriately in future articles. Send your questions to editor@heattreattoday.com.
Jason Schulze on AMS2750E: Examining Requirements That Apply to TUS Thermocouples Read More »