Nevada, Wisconsin Construction Equipment Manufacturer Expansion Includes Heat Treat
A manufacturer and supplier of earth-moving equipment recently announced expansion plans that include two of its brands building new facilities in Nevada and Wisconsin, one to host a new heat treat shop.
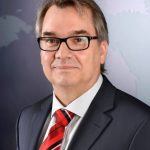
Komatsu Equipment Company will a build state-of-the-art, $47 million customer support and service center in Elko, Nevada. This announcement comes not long after Komatsu Mining Corp reported intentions to construct a new headquarters and manufacturing campus near the location of the company’s original machine shop off South First Street in Milwaukee, Wisconsin.
Komatsu’s investment of nearly $300 million at the Milwaukee site will include the design and construction of advanced machine, heat treat, and fabrication shops; state-of-the-art technology, R&D, and robotics labs; as well as new office and training facilities. Komatsu Mining Corp. aims to reduce energy consumption with green initiatives, including solar panels, wind spires, a remotely operated closed-loop heat treat system, green spaces, LED lighting and other sustainable solutions. Project completion is expected in 2022.
“The new campus provides us opportunity for advancement in state-of-the-art facilities that expand our capabilities on a global scale,” said Jeff Dawes, President and CEO of Milwaukee-based Komatsu Mining Corp. “Our new facilities will be designed to enhance safety, efficiency and environmental sustainability – all top priorities of Komatsu worldwide, allowing us to better serve our customers and deliver innovative solutions.”
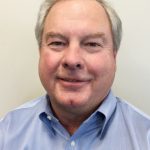
Of the new 189,000 sq-ft manufacturing space in Elko, Nevada, Komatsu Equipment Company John Pfisterer said: “The new building offers an exciting opportunity to bring together local employees of two major Komatsu subsidiaries: KEC and Komatsu Mining Corp. (KMC), into one integrated organization. Collaborating directly in a shared, state-of-the-art space, these combined teams will enhance customer support and operational efficiency.”
The new building will include a six-bay, full-service construction equipment and mechanical rebuild shop; a heavy welding and fabricating shop, large enough for rebuild and manufacturing of large shovel and truck structures and manufacturing of truck bodies; a heavy machine shop with large, horizontal milling and boring machine, plus vertical lathe capability; and a construction equipment and rental-machine yard. The Nevada project is planned for completion in early 2020.
Nevada, Wisconsin Construction Equipment Manufacturer Expansion Includes Heat Treat Read More »