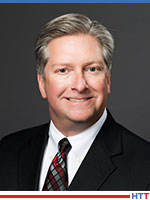
Automotive part designs and heat treating processes have undergone many changes over the years, especially the powertrain. By looking back at the progress of these changes, we can learn more about emerging trends in automotive heat treating today.
In this Heat Treat Today Technical Tuesday feature, Bill Disler, president and CEO of AFC-Holcroft, brings his familiarity with big atmosphere carburizing systems and LPC automotive cell carburizing systems and looks at how the evolution of equipment and process requests says a lot about the trends we see today in automotive heat treating.
This article originally appeared in Heat Treat Today’s June 2019 Automotive print edition.
Although many components undergo heat treatment processes, the powertrain—specifically, gears— typically requires more carburizing time than other automotive parts. Not surprisingly, the powertrain has also seen many changes in heat treatment trends.
Not only have powertrain designs gone through tremendous transformations but so has the equipment being used to process those evolved components. Having spent years on the supplier side of atmosphere furnaces, vacuum carburizing, and gas quench as well as induction systems, I find it interesting to look back at some of the drivers that have helped morph this industry’s heat treat needs.
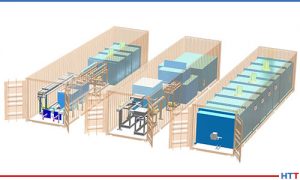
Large atmosphere pusher furnaces produced nearly all of the powertrain gears 20+ years ago. Today, cellular low-pressure carburizing (LPC) and gas quench systems carry the load, although the results have not been cost saving. Moving from high volume gas heated carburizing equipment to small batch carburizing in electrically heated furnaces did not reduce utility costs per part; instead, other areas adjusted to compensate. Eliminating the expense of hard grinding transmission gears was an acceptable rationale for this increase in both capital expense and operating costs. Eventually, streamlining the overall gear manufacturing process, combined with locating heat treat within machining lines, produced positive measurable results. Plant traffic decreased, minimizing safety risks. Cooler and cleaner furnace systems were designed. And installations were made easier. Many agreed the changes were justified.
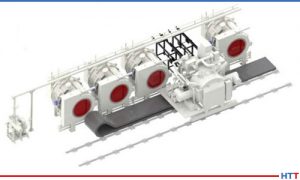
As we look back, many of these drivers for change proved valid. Others, not so much. In most cases, consumer preference for quiet powertrains necessitates hard grinding of gears. Green is in and talk of the absolute need for zero intergranular oxidation (IGO) in carburized gears has slowed. LPC/Gas post quenched parts are perceived as cleaner and leaner; however, it is often difficult to differentiate green parts from processed parts, so it has become a best practice to add part marking after carburizing and hardening to avoid even the remote risk of sending soft parts down the line to the next stage of manufacturing. Shot peening is still common for strength reasons. The ability to nest large cellular LPC systems within machining has been a success, but rarely are the installations as quick and easy as promised.
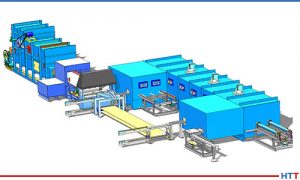
Conventional atmosphere furnace technology has advanced as well, although at a slower pace, in step with a renewed interest in energy efficiency, particularly in the U.S. where gas is cheap and electric is not. Combustion systems operate cleaner and at much higher efficiency than in the past. Having said that, it is curious how little interest end users have in trading cost-saving gas-heated systems for the easier to install, neater looking electric heating options. In addition, it is no longer common to use water for cooling conventional atmosphere furnace systems as end users do not want to deal with the cost and complications that accompany this option. The market is polarized over this. LPC systems rely on large water volumes for cooling, and they are small batch, electrically heated systems. At the same time, gas quench systems consume huge quantities of water and require giant 300 HP plus motors that are tough to manage in plant power systems.
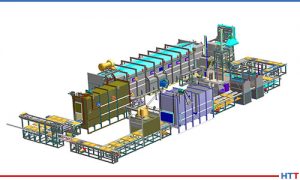
It is my observation that the automotive market is anticipating the next iteration of heat treat equipment. One type of process or equipment style will not fit all needs, yet all hope for the perfect single part flow solution—an elusive dream due to physics. The cost/time equation still does not balance, and carburizing offers the benefits many manufacturers are looking for, despite the desire to design the process out of practice. Many automotive transmission parts that were originally processed in LPC and gas quenched now use gas nitriding instead, even though gas nitriding is another long process, and nitriding introduces ammonia back into the process—something most automotive plants are not enthusiastic to have in their plants. Two steps forward and one step back.
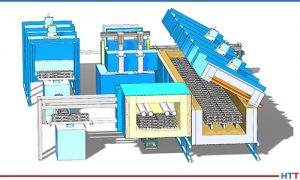
With the widening range of processes and solutions under exploration, as well as ever changing powertrain systems designed to accommodate supplemental electric motors, lighter weights, smaller cars, and larger SUVs, all we can be certain of is ongoing change. I believe that we have witnessed major adjustments in automotive heat treat processing as the pendulum has swung from big, multi-row atmosphere pushers with salt or oil quench to electric-heated cellular LPC and gas quench units. One surprising result has been the resurgence of salt quenching, which controls distortion of high-pressure gas at a much lower cost with less complexity. Salt, like gas, is a single-phase quench media: It does not boil in these processes like oil does, and it can be used at temperatures that support martensitic quench with far less thermal shock and much higher heat transfer than the options. Older processes carry the baggage of tarnished past reputations, but I no longer count them out. Today’s automation, process control technology, and innovation can provide the foundation for brand new concepts, repackaging of older ideas, and hybrids of multiple technologies. Together, these create building blocks that heat treat equipment suppliers will use to meet changing trends in automotive carburizing and heat treatment. It will be interesting to be involved in the journey as these changes take place.
About the Author: Bill Disler is president and CEO of AFC-Holcroft, part of the Aichelin Group located in Vienna, Austria. He is a member of the Board of Trustees -Metal Treating Institute (MTI), and a member of the Board of Advisors at Lawrence Technical University, College of Engineering in Southfield, Michigan. This article originally appeared in Heat Treat Today’s June 2019 Automotive print edition.