Now that a new year is in full swing, it may be time to consider that all of the heat treating equipment that’s currently in the workplace has aged along with us. Without proper maintenance in place, you may start to see signs of age, wear, and tear on the high output furnaces that this industry relies on.
This Technical Tuesday, was originally published in Heat Treat Today’s January/February 2024 Air and Atmosphere Heat Treat print edition.

Mechanical Engineer
Premier Furnace Specialists, Inc./BeaverMatic
Source: Premier Furnace Specialists, Inc./BeaverMatic
Most companies have a “workhorse” furnace which is run exhaustively, and even new furnaces that run this way can start looking quite worn after just months of use. Yet decades-old equipment remains in regular use across the country, thanks to knowledgeable maintenance personnel. Since there is somewhat of a void in personnel for this position, here are a few ways to make sure your furnaces keep running into old age.
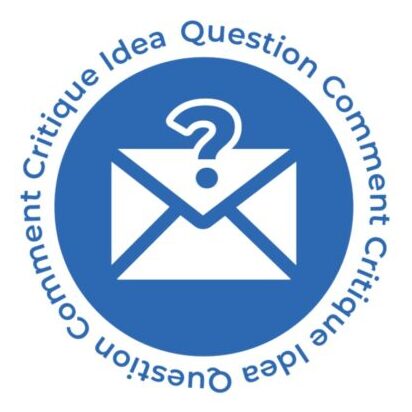
For roller hearth or belt furnaces with rollers, there can be an extensive number of points in the drive which may facilitate misalignment. Most maintenance crews know to keep chains and sprockets in alignment and to keep bearings well-greased to avoid seizing, but these may not be enough for the high temperatures at which these furnaces typically run. Even though they are turning at slow speeds, the roller’s bearings should be filled with high-temperature grease which is designed not to break down and leak despite the heat constantly being transferred through the roller to the external trunnions (shaft ends). If the bearing already has standard grade grease, it needs to be fully pumped out of the bearing with new high-temperature grease to avoid contamination or reactions between the two which could cause leaking or seizing.
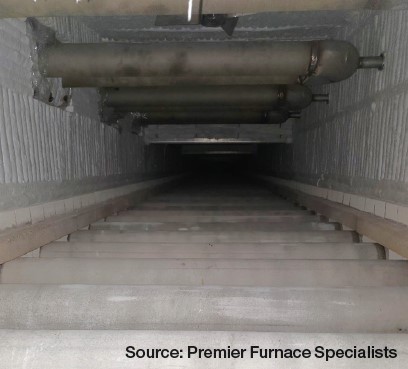
For driven rollers, it’s only necessary to “lock-down” the drive side of the roller’s components using cone or dog point set screws (sometimes both) and thread locking compounds. As the furnace heats up, the rollers will expand. By leaving the idle end “free,” it allows a path of least resistance for growth, which allows for the best chance to keep drive mechanisms in-line.
An infrared (IR) thermometer can be a useful tool for diagnosing heat leaks around any furnace and avoiding burns while doing so during operation. It’s important to note that on stainless steel components and the glossy enamel coatings on some furnaces, IR temperature readings likely will not be exact. Quality IR thermometers have adjustable emissivity settings which greatly reduce the error caused by these highly reflective surfaces, but readings still should be used simply as reference points.
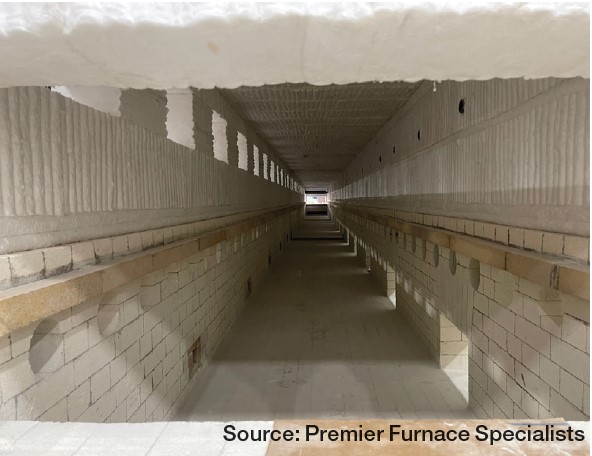
It’s a good idea to occasionally check the furnace case for “hot spots,” and this tool allows it to be done without much effort. These are areas which have a higher than typical temperature compared to the rest of the furnace. This can be one of the earliest signs that insulation quality in that spot has issues. The insulation can be checked and repaired rather than waiting until the furnace’s case steel begins to turn white and burn away, leading to more costly repairs. For brick-lined furnaces in particular, one ideal time to perform this check is during the lengthy dry-out procedure to ramp up to operating temperature after a shutdown. The idle time at low temperatures helps to catch issues before high operating temperatures quickly make them worse. For roller hearth furnaces, simply checking the average temperature of each roller’s exposed trunnions and bearing housings can give insight into potential future issues if individual rollers run hotter than others.
As they say, “The best time to start was yesterday. The next best time is now.” Even a furnace that has seen better days can be maintained, repaired, or rebuilt to keep operations running smoothly and, most importantly, safely.
About the Author
Jacob Laird is a mechanical engineer at Premier Furnace Specialists. Jacob has a BS in both mechanical engineering and physics from South Dakota State University. Among many other things, Jacob is known for his skills in sizing/design of combustion systems, burner assembly, and electrical heating systems.
For more information: Contact Jacob at JLaird@premierfurnace.com.