Guest post by www.MetallurgyData.com
MetallurgyData.com has produced a video series entitled Steel Metallurgy. Preview this episode at –http://www.metallurgydata.com/index.php/metallurgy-for-non-metallurgists-2/steel-metallurgy/. The preview runs under 4 minutes with the full video being just over 19 minutes long. The full video can be purchased for $4.99 from www.metallurgydata.com.
This is the second in a series of blogs titled ‘Metallurgy for the Non-Metallurgist’. The first blog looked at materials (https://www.heattreattoday.com//2016/08/metallurgy-for-non-metallurgists-from-metallurgydata-com/). In this second post we will look at the fundamentals of steel metallurgy.
Steel is primarily iron with up to 1% carbon, plus other alloying additions (generally totalling less than 5%).
A steel composition can be thought of as a recipe; different amounts of each ingredient make up your final product. In steel these ingredients are known as alloying additions and can affect the steel in different ways. We can affect the:
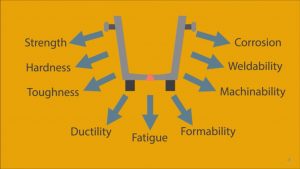
- strength
- hardness
- toughness
- ductility
- fatigue
- formability
- machinability
- weldability, and
- corrosion resistance.
The addition of carbon to iron is probably the most important addition in steels which makes ‘The Iron Carbon Equilibrium Diagram’ very useful. Equilibrium means that enough time has been allowed on heating and cooling for any reactions to fully complete.

In a steel <723°C, different structures are present and depending on the carbon content we can have at <0.8% Carbon – ferrite and pearlite, at 0.8% carbon – pearlite and >0.8% carbon – pearlite and cementite.
While the iron carbon diagram describes the structures of steel under equilibrium conditions, two further diagrams can be used when faster cooling rates are used; these are the CCT (continuous cooling transformation) diagram and the TTT (time temperature transformation) diagram. Both of these diagrams are helpful in selecting the optimum steel and process parameters.
When we cool a steel at faster cooling rates we can achieve additional structures, these can be bainite and martensite. CCT and TTT help determine the structures achieved.
In metallurgy the hardenability of a steel is a key parameter and when we talk about hardenability in steels we are often describing how deep into the steel we can achieve hardening. If a steel is described as having a low hardenability this will mean that the steel will produce a shallower depth of hardness. Hardenability is not to be mistaken for hardness; when describing the hardness we are often looking at the microstructure achieved during cooling. For a given steel it can be assumed that the quicker the cooling rate the greater the chance of achieving a harder structure and if that steel has a high hardenability this hard structure will be present deeper into the thickness.
In metals there are atomic defects called dislocations, these dislocations reduce the strength of the metal. The principle of strengthening mechanisms is to reduce the ability of these dislocations to move through the metal, this can be achieved by:

- Grain Size; the grains can interact with the dislocations preventing further movement. If we reduce the grain size we can increase the number of grains interacting with the dislocations, preventing movement and thus strengthening the metal.
- Cold work introduces a large amount of strain into the metal; this strain interacts with the dislocations strain field, impeding the movement of the dislocations.
- Solid solution strengthening is applied when we add other chemical elements to a metal. Addition of these elements can either be called interstitial or substitutional solid solution strengthening and will cause distortion in the atomic structure, restricting the dislocation movement and strengthening the steel.
- Dispersion or precipitation strengthening is highly related to the structure of the metal and takes place when a phase is finely precipitated through a softer matrix. This precipitate acts as a barrier to dislocation movement.
The next in the series will be Steel Making and Casting.