Busch Group Adds 60,000 sqft US Facility
Busch Vacuum Solutions, part of the Busch Group, a global company in vacuum and overpressure technology, has announced the development of its newest U.S. facility. As a key regional hub, the facility will specialize in the repair, service, and overhaul of vacuum pumps, vacuum systems, and overpressure equipment including turbo molecular pumps, leak detectors, valves, and accessories. The almost 60,000-square-foot facility will be located in Tempe, Arizona.
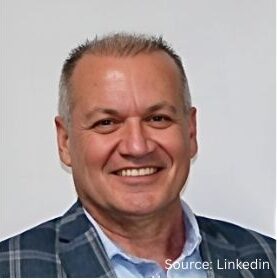
President & CEO
Busch Group USA
The state-of-the-art facility is scheduled to open in October 2025. This expanded capability brings greater flexibility, technical expertise, and responsiveness to customers across the semiconductor, industrial, medical, and environmental sectors. The Tempe Service Center will provide faster turnaround times, expert support, and more efficient service delivery tailored to the unique operational needs of those across the U.S.
“This investment represents more than just added square footage. It’s about proximity, partnership, and performance. With the launch of our Tempe location, we’re better positioned to deliver unmatched value…on advanced vacuum technologies in high-performance environments,” said Turgay Ozan, president & CEO of Busch Group USA.
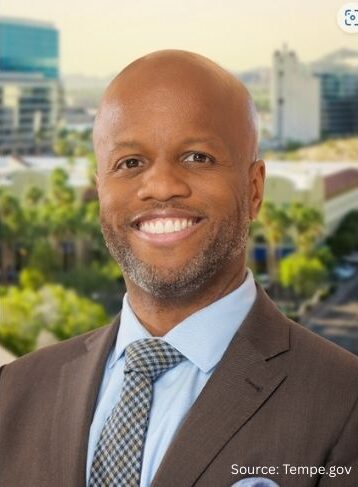
Mayor
Tempe, Arizona
The mayor of Tempe, Corey Woods, commented, “We’re excited to welcome Busch Vacuum Solutions…Their decision to invest here speaks to the strength of Arizona’s semiconductor ecosystem, diversity of thriving industries located here, and the spirit of innovation that defines our community. The new Tempe Service Center will create skilled employment opportunities, strengthen business partnerships, and keep Tempe at the forefront of high-tech growth and excellence.”
In addition to semiconductor and industrial markets, Busch’s vacuum technology supports automotive, food and beverage, packaging, metallurgy, pharmaceuticals, plastics, and large-scale distribution. These capabilities enable more localized production and increase operational resilience across essential supply chains.
Press release is available in its original form here.
Find heat treating products and services when you search on Heat Treat Buyers Guide.Com
Busch Group Adds 60,000 sqft US Facility Read More »