The Heat Treatment of Aerospace Fasteners
Dan Herring is recognized as the summa wizard of heat treating. This paper, originally published in the October 2014 issue of Fastener Technology International (FTI), then reprinted in Heat Treat Today’s March 2019 Aerospace print edition, addresses the critical issue of strength-to-weight in aerospace fastener applications and materials.
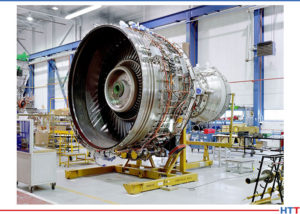
(photograph courtesy of Performance Review Institute)
When we deal with applications where strength-to-weight ratio is a critical consideration (Fig. 1[1]), we often turn to solutions involving the so-called “light metals”, namely aluminum, beryllium, magnesium, and titanium, to enhance engineering performance while minimizing the weight of components and structures.
It is important to remember that light metals possess other physical properties, which may be of importance in selection or service, such as the good electrical and thermal conductivity of aluminum, the machinability and noise dampening of magnesium, or the extreme corrosion resistance of titanium. Our heat treatment processes must retain and, in some cases, enhance these properties.
Aerospace Fastener Applications and Materials
There are many types of fasteners used in aerospace structural assembly, which include solid rivets, pins with collars, bolts with nuts, and blind fasteners. Other fastener types including latches, straight pins, head pins, lock pins, cotter pins, quick-release multiple piece fasteners, retaining rings, and washers are also commonplace. Aerospace fastener materials include aluminum (e.g. 2024, 6061, 7075), titanium (e.g. Ti-6Al-4V, Ti-6Al-2Sn-4Zr-2Mo), superalloys (e.g., Waspaloy, Hastalloy, Inconel 718) and in some instances steel, stainless steels, tool steels, and nickel alloys (e.g. K-Monel).
Aluminum is the most common fastener material used in the aerospace industry and in many other transportation systems as well. This is because aluminum alloys in addition to having an excellent strength-to-weight ratio can be heat-treated to achieve relatively high strength. Aluminum is easy to form and is relatively low cost. The heat treatable aluminum grades are the 2xxx, 6xxx, and 7xxx series. Aircraft manufacturers, for example, use high-strength alloy 7075 to fasten aluminum aircraft structures. This alloy has zinc and copper added for strength and machinability.
Titanium also has a number of attractive properties including low density and elastic modulus making it a good candidate material for aerospace fasteners, both of the internally and externally threaded varieties. The use of nuts with lower modulus than the male fastener is known to reduce the stress concentration effect at the first thread and improves the distribution of load over the length of the engaged threads. Titanium fasteners are used when a combination of strength and corrosion properties are important, such as when composite materials are involved.
Superalloys are used in applications requiring performance under high operating temperatures, extreme corrosion environments, demands for high creep strength and high fatigue strength, and in cryogenic applications. Superalloy fasteners are found on solid rocket motors, aircraft gas turbine engines, airframes, space shuttle structures, and the like. The superalloys fall into three basic groups: the iron-nickel-base superalloys; the nickel-base superalloys and the cobalt-base superalloys. The iron-nickel-base superalloys evolved from stainless steel technology and are generally wrought. Nickel-base and cobalt-base superalloys can be either wrought or cast. Nickel-base superalloys can be used at the very highest temperatures, just below their melting temperatures of about 2200°F to 2500°F (1205°C to 1370°C).
Heat Treatment of Aluminum Fasteners [2,3]
Aluminum alloys are classified as either heat treatable or not heat treatable, depending on whether the alloy responds to precipitation hardening, the key characteristic being that the alloying elements show greater solubility at elevated temperatures than at room temperature.
Solution Heat Treating
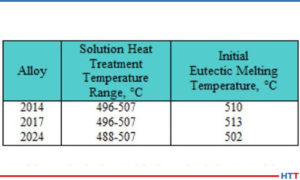
Solution heat treatment involves heating the aluminum and alloys to a temperature slightly below the eutectic melting temperature. The objective of solution heat treatment is to maximize the amount of solute in solid solution. This requires heating the material close to the eutectic temperature and holding the material at temperature long enough to allow the alloy to become a homogenous solid solution. After solution heat treatment, the material is quenched to maintain the solute in supersaturated solid solution. Temperature control is crucial because the solution heat treatment and the eutectic melting temperatures are so close, especially for 2xxx series alloys (Table 1[2]).
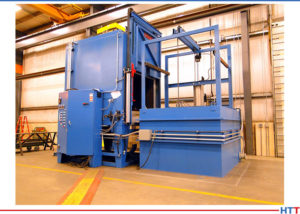
Solution heat treating problems include oxidation, incipient melting, eutectic melting, and under-heating and can be overcome by close control of process and equipment variability. Solution heat treating and quenching of these alloys is typically accomplished in large high-temperature ovens. In some applications, the oven is supported above the quench tank (Fig 2).
Quenching
The purpose of quenching is to create a supersaturated solid solution at room temperature so that the aging process can strengthen the material. The amount of precipitation occurring during quenching reduces the amount of subsequent hardening possible. This is because as solute is precipitated from solution during quenching, it is unavailable for any further precipitation reactions. This results in lower tensile strength, yield strength, ductility, and fracture toughness.
The cooling effect of quenchants has been extensively studied and the influence of quench rate on mechanical properties has been quantified. For example, it was determined that the critical quenching temperature range for 7075 aluminum alloy is 750°F to 550°F (400°C to 290°C). At quench rates exceeding 840°F/sec (450°C/s), it has been determined that maximum strength and corrosion resistance is obtained. At intermediate quench rates of 840°F/sec to 212°F/sec (450°C/s to 100°C/s), the strength obtained is lowered, but the corrosion resistance is unaffected. Between 212°F/sec and 68°F/sec (100°C/s and 20°C/s), the strength decreased rapidly, and the corrosion resistance is at a minimum. At quench rates below 68°F/sec (20°C/s), the strength decreases rapidly, but the corrosion resistance improved. However, for a given quenching medium, the cooling rate through the critical temperature range was invariant no matter the solution heat treat temperature.
Problems occurring during quenching are typically distortion or inadequate properties caused by a slow quench, resulting in precipitation during quenching and inadequate supersaturation.
Aging
The aging process for aluminum involves either natural aging or artificial aging. Natural aging involves the rapid formation of GP (Guinier-Preston) zones from the supersaturated solid solution and from quenched-in vacancies with strength increasing rapidly with properties becoming quasi-stable after approximately 4 to 5 days. These alloys will continue to exhibit changes in properties as the years go by.
Many heat treatable aluminum alloys are artificially aged after quenching. Precipitation hardening (aging) involves heating the alloyed aluminum to a temperature in the 200ºF to 450°F (95ºC to 230ºC) range. At this temperature, the supersaturated solid solution, created by quenching from solution heat-treating, begins to decompose and accelerates precipitation in heat treatable alloys. The aging curves for the alloys vary; however, generally the higher the aging temperature, the shorter the time required to attain maximum properties.
Heat Treatment of Titanium Fasteners
Titanium alloys are typically classified as pure titanium, alpha, beta, and alpha-beta alloys. There are also so-called near alpha and near beta (i.e. metastable beta) phase alloys. Under equilibrium conditions, pure titanium and alpha (α) phase have hexagonal close-packed structures up to 1620°F (882°C), above which they transform to beta (β) phase having a body-centered cubic structure up to the alloy’s melting point.
Near alpha alloys typically have a small amount (1 to 2 %) of the stabilizing beta phase present. In near beta alloys, significant additions of the beta-stabilizing phase suppress the Ms temperature below room temperature and the beta phase is retained at room temperature by rapid cooling or quenching from the alpha-beta phase. The inherent properties of all these structures are quite different.
Titanium alloys have a complex heat treatment process (Table 2[4], 3).
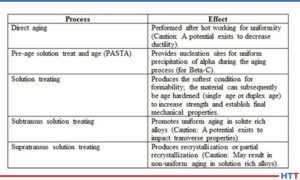
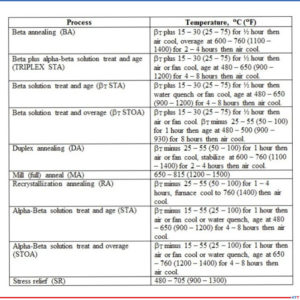
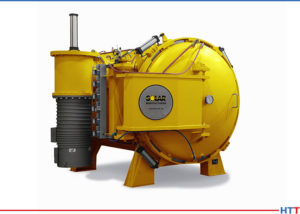
Most superalloys are hardened using a solution treating and aging process (Table 4[3]). Solution treating involves heating the alloy to a temperature in the range of 1800°F (982°C) or higher, followed by gas quenching. In most cases, superalloys are processed in a vacuum furnace (Fig. 3) and do not require a rapid quench. Pressures of two bar or less are often sufficient for quenching. This is followed by aging (age hardening) at intermediate temperatures for extended periods of time. Normally, the complete solution treat and aging cycles can be programmed into the furnace so that unloading is not required between cycles. Certain superalloys, however, require other special treatments to develop required properties.
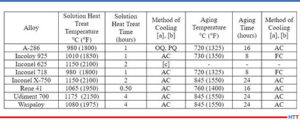
Summary
Fasteners account for a significant amount of component parts in aircraft, rotocraft, and space vehicles where strength, corrosion, and weight of structural assemblies are important. Fasteners play a critical role in defining the longevity, structural integrity, and design philosophy of most metallic aerospace structures.
Notes:
- Cooling nomenclature: FC = furnace cooling; AC = air cooling; RAC = rapid air cool; OQ = oil quench; PQ = gas pressure quench.
- Air cooling equivalent is defined as cooling at a rate not less than 22°C/min (40°F/minute) to 595°C (1100°F) and not less than 8°C/min (15°F/minute) from 595°C to 540°C (1100°F to 1000°F). Below 540°C (1000°F) any rate may be used.
- To provide adequate quenching after solution heat treatment, cool below 540°C (1000°F) rapidly enough to carbide precipitation. Oil or water quenching may be required on thick sections.
References
- Leigh, Joanna, New Checklist for Nadcap Audits, Industrial Heating, November 2011.
- Mackenzie, D. Scott, Heat Treating Aluminum, HOT TOPICS in Heat Treatment and Metallurgy, Vol. 2 No. 7, July 2004.
- Herring, D.H., Atmosphere Heat Treatment Volume I, BNP Media Group, 2014.
- Herring, D.H., Vacuum Heat Treatment, BNP Media Group, 2012.
- Herring, D.H., Metallurgy of Aluminum and Aluminum Alloys Parts One and Two, white paper, 2006.
About the Author: Daniel Herring, The Heat Treat Doctor®, is a metallurgist, designer, and materials scientist who takes seriously the initiative to educate current and future generations of heat treaters in the ways of the industry. More about The Heat Treat Doctor® can be learned from his Heat Treat Consultants page. This paper was originally published in the October 2014 issue of Fastener Technology International (FTI), then reprinted in Heat Treat Today’s March 2019 Aerospace print edition. It is published here with permission from the author.
The Heat Treatment of Aerospace Fasteners Read More »