Hydrogen is a reducing gas used in thermal processing atmospheres for brazing, annealing, metal injection molding, metal additive manufacturing, and glass-to-metal and ceramic-to-metal sealing. Recent supply chain issues, safety concerns surrounding storage, and the growing metal additive manufacturing parts market are making on-site generated hydrogen a burgeoning trend among thermal processors.
This article first appeared in Heat Treat Today’s February 2022 Air & Atmosphere Furnace Systems print edition and was written by Lynn Gorman, a freelance writer.
Reliance on Hydrogen Delivery Can Be Risky
We learned in 2020 that when the pandemic hit, hydrogen gas supply declined, and liquid hydrogen production slowed accordingly.
Hydrogen is a byproduct of refineries processing crude oil, and when demand for gasoline and other crude oil-based products slows, so does hydrogen production. Even as the economy fights back post COVID-19 the long-term trends in crude oil processing are negative because of increasing fleet electrification.
Photo Credit: Nel Hydrogen
Besides having more control and assurance that hydrogen will be available on demand as needed, there are other benefits to generating hydrogen on site. According to David Wolff, regional manager at Nel Hydrogen, the only raw materials required to produce hydrogen on site are water and electricity, which are among the most reliable of supply chains. “Essentially the hydrogen becomes another utility with little personnel attention required,” he said. “Electricity and water come into a plant in pipes and wires and are highly reliable. Additionally, there are no hydrogen storage tanks taking up a large amount of unusable space.” He added further that electrolyzers produce ultra-pure, extremely dry hydrogen for best processing results; companies can move the electrolyzers if they relocate to another facility; generating hydrogen eliminates the supply interruptions and contract issues; and producing hydrogen reduces costs over time.
Photo Credit: Nel Hydrogen
Hydrogen Generation Facilitates Processing Atmospheres
For thermal processors, the ultimate priorities for a thriving business are parts and profits. Satisfying customers with high quality, heat treated components keep them coming back. To that end, generating hydrogen on site can play a significant role . For instance, hydrogen has the highest heat transmission of any gas, resulting in faster heating, faster cooling, and faster cycle times in both continuous and batch furnaces. Hydrogen atmospheres clean parts, and clean part surfaces enhance sintering/fusion. Hydrogen also scavenges oxygen which counteracts potential furnace leaks. Companies that make their own pure hydrogen, already formulated for their thermal process atmospheres and always available, can potentially improve plant productivity and part quality with the desired properties demanded by their customers.
“The many positives of hydrogen generation work for companies experiencing environmental pressures to choose alternatives to delivered and stored gases,” said Wolff. For instance, he cited a case in which a specialty wire producer in an urban area used dissociated ammonia for wire annealing for decades. However, a gradual shift in their neighborhood to less industry and more housing, schools, and places of worship made it risky to continue storing the toxic ammonia gas to make dissociated ammonia. The company chose to invest in hydrogen and nitrogen generation to replace their ammonia storage and dissociator. According to Wolff, the company is now using less electricity, and can use a leaner atmosphere blend because hydrogen is drier than dissociated ammonia. They are getting cleaner wire, saving money using less electrical power, and eliminating ammonia purchases and tank rental.
Regional Sales Manager
Nel Hydrogen
Photo Credit: Nel Hydrogen
In another case, a different specialty wire producer suffered a catastrophic fire that involved hundreds of hydrogen cylinders stored at their historic facility. The company had to replace the plant. To meet current safety and fire code standards, the decision to generate hydrogen was a great choice to comply with the demands of the local fire marshal. According to Wolff, “Authorities having jurisdiction are some of the best advocates for hydrogen generation versus storage.”
Certain Growing Applications Prefer Generated Hydrogen for Best Part Quality
The newest powder-based manufacturing technology is metal AM (metal additive manufacturing) which expands on the learnings and foundations of PM (powder metallurgy) and MIM (metal injection molding). Metal AM is growing rapidly in applicability. Several metal AM techniques are commercialized, and even more are in development. There are several ways that metal AM is revolutionizing fabrication by eliminating complex set-ups, molds, and fixtures, and thereby reducing the costs of short runs. The method allows for continuous design improvements, practically in real time. Metal AM enables parts to be very lightweight through internal strengthening, and parts can be directly translated and produced from a CAD file. In other words, metal AM can create parts that are impossible to make by other approaches. While there is a range of techniques that can be applied to the general category of metal AM parts, most of them use powder, as powder provides the best part finish quality. And, like previous powder fabrication technologies such as PM and MIM, metal AM uses sintering to adhere the metal powder particles together with metal-to-metal bonds.
Photo Credit: Nel Hydrogen
Metal AM powders are miniscule (20–100 microns), uncoated, and handled gently during fabrication. They are highly susceptible to oxidation if unprotected by an appropriate atmosphere. These tiny particles have an enormous surface area (3kg of typical metal AM 316 SS powder has the surface area of a tennis court). Pure hydrogen (or blended with N2 or Ar gas) is the optimal reducing atmosphere for sintering metal AM parts in both atmosphere furnaces and vacuum furnaces. According to Wolff, a company having the capability to produce its own hydrogen will have the best results with these kinds of parts that will grow in demand in the coming years.
Compliance Considerations in Hydrogen Use
While generating hydrogen for on-site use without storing inventory is far safer than storing hydrogen or ammonia, there are still rules to follow. There are issues surrounding exhaust, pressure balancing, air flow, heating/cooling, and other considerations. Safety, of course, is paramount when using hydrogen. Helpful publications to review include NFPA 2, NFPA 55, ASME Code for Pressure Piping B31.1, and FM Global Property Laws Hydrogen Data Sheet. Additionally, if the building is leased, the landlord should be aware of the use of hydrogen as should the insurance agent.
Photo Credit: Nel Hydrogen
“Thousands of hydrogen users have proven that, given the right set of circumstances, it’s in their interest and their customers’ interest to generate hydrogen on site,” said Wolff. “And that’s because hydrogen generators produce high purity, pressurized, dry hydrogen with zero hydrogen storage. It’s also a compact, portable, and reliable system, that provides a range of flow rates to suit any thermal processing requirement. And, the hydrogen cost is relatively fixed, so as production goes up, the cost per part goes down.”
For more information: Please send your inquiry to info@nelhydrogen.com or visit www.nelhydrogen.com.
.
Search this supplier's listing on Heat Treat Buyers Guide.com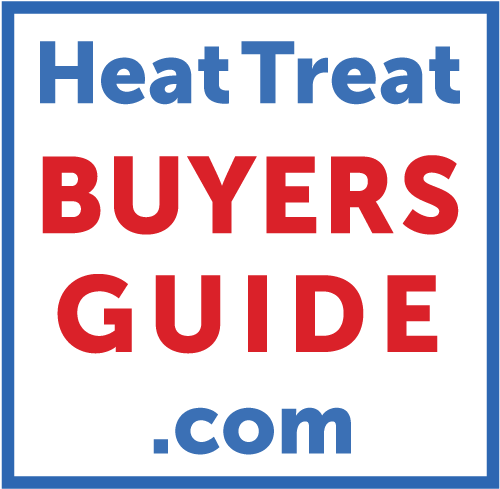