Medical Device Manufacturer Acquires Metal and Silicon Nitride Developer
A medical device design, development, and manufacturing company recently announced plans to acquire an innovative biomaterials and OEM company that develops and commercializes silicon nitride for various biomedical applications including orthopedic, dental and arthroplasty.
Amedica Corporation announced that it has entered into an asset purchase agreement with CTL Medical, based in Dallas, Texas, medical device manufacturer with in-house manufacturing facilities that focuses on the spine implant and instrument market. The agreement will make CTL Medical the exclusive owner of Amedica’s portfolio of metal and silicon nitride spine products, with access to future silicon nitride spine technologies.
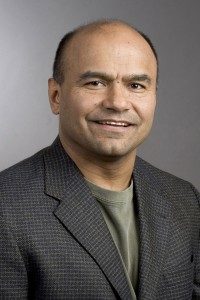
As part of the up to $10 million transaction, CTL Medical will acquire Amedica’s entire existing inventory of spine products, including US and OUS regulatory clearances and intellectual property related to such. Amedica’s products, which are presently sold under the brand names of Taurus, Preference, and Valeo will be transferred to CTL Medical, while manufacturing, R&D, and all intellectual property related to the core biomaterial technology of silicon nitride will remain with Amedica in Salt Lake City. Amedica will serve as CTL’s exclusive OEM provider of silicon nitride products.
Following the purchase, CTL Medical will change its name to CTL Amedica. Amedica will re-position under a new name that is reflective of the breadth of its technology and potential applications.
“The transaction makes strategic sense, by monetizing our commercial spine sales organization and allowing Amedica to focus on its core biomaterials and OEM business,” said Dr. Sonny Bal, Chairman of the Board of Directors of Amedica. “The addition of a highly-differentiated silicon nitride and metal product line to CTL Medical’s complete offering of spine surgery implants and instruments will benefit both companies, as well as our surgeon customers. Amedica’s products and scientific data have established that silicon nitride resists bacteria, promotes bone healing, and has superior clinical outcomes. CTL Medical is best positioned to profitably leverage these advantages in the retail spine market.”
CTL Medical produces a full line of cervical, thoracic, and lumbar products (hence “CTL”) at its manufacturing headquarters in Dallas, Texas.
Medical Device Manufacturer Acquires Metal and Silicon Nitride Developer Read More »