Pittsburgh Metals Company Acquires Aerospace & Defense Additive Manufacturer
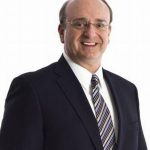
A Pittsburgh-based specialty metals company recently announced that it has acquired a leading pro metal alloy-based additive manufacturer for the aerospace and defense industries, located in New Britain, CT.
Allegheny Technology Incorporated (ATI) purchased Addaero Manufacturing, combining “ATI’s deep knowledge and experience in commercial aerospace and our industry-leading powder metal manufacturing capabilities, including our new aerospace-qualified Bakers Powder Operations, and Addaero’s technical expertise to produce aerospace quality parts using various additive manufacturing technologies,” said Rich Harshman, ATI’s chairman, president and CEO.
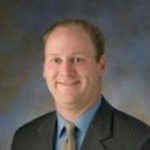
“Addaero’s competencies are a natural extension of ATI’s metallic powder expertise and will expand our capabilities to provide comprehensive customer solutions ranging from the design of parts for additive manufacturing to the production of ready-to-install components. The acquisition of Addaero is another building block in our strategy to enhance ATI’s full specialty materials capabilities to provide end customers with finished products,” Harshman added.
“The Addaero team is excited to be a part of ATI. The combination of ATI and Addaero will increase the speed to market of new and innovative additively manufactured powder metal solutions for our aerospace and defense customers and beyond,” said Rich Merlino, president, Addaero Manufacturing.
Photo credit: Addaero Manufacturing; photo caption: 1) The Addaero Manufacturing team; 2) The above rocket nozzle was fabricated in Inconel 718 with internal cooling channels to reduce wall temperature. The engine was hot fired 10 times for up to 30 seconds in duration.
Pittsburgh Metals Company Acquires Aerospace & Defense Additive Manufacturer Read More »