How often do you think about the intelligent designs controlling the thermal loop system behind your heat treat operations? With ever-advancing abilities to integrate and manage data for temperature measurement and power usage, the ability of heat treat operations to make practical, efficient, and energy-conscious change is stronger than ever. In part 1, understand several benefits of thermal loop systems and how they are leveraged to comply with industry regulations, like Nadcap.
This Technical Tuesday article by Peter Sherwin, global business development manager — Heat Treatment, and Thomas Ruecker, senior business development manager, at Watlow was originally published in Heat Treat Today's January/February 2024 Air & Atmosphere Heat Treat print edition.
Introduction

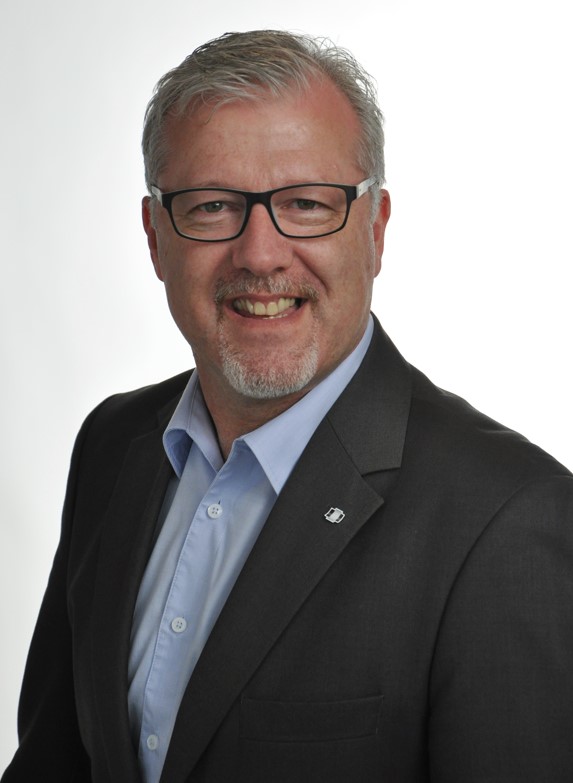
Heat treatment processes are a crucial component of many manufacturing industries, and thermal loop solutions have become increasingly popular for achieving improved temperature control and consistent outcomes.
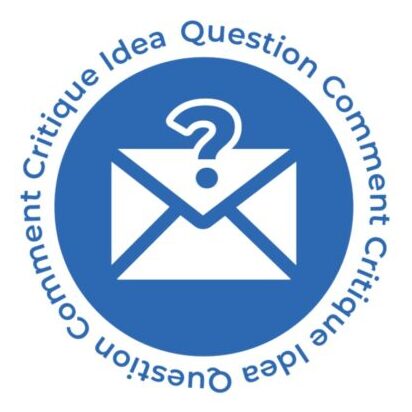
A thermal loop solution is a closed loop system with several essential components, including an electrical power supply, power controller, heating element, temperature sensor, and process controller. The electrical power supply provides the energy needed for heating, the power controller regulates the power output to the heating element, the heating element heats the material, and the temperature sensor measures the temperature. Finally, the process controller adjusts the power output to maintain the desired temperature for the specified duration, providing better temperature control and consistent outcomes.
Performance Benefits
Heat treatment thermal loop solutions offer several advantages over traditional heat treatment methods, including improved temperature control and increased efficiency. The thermal loop system provides precise temperature control, enabling faster heating and cooling and optimized soak times. In addition, the complete design of modern thermal loop solutions includes energy-efficient heating and overall ease of use.
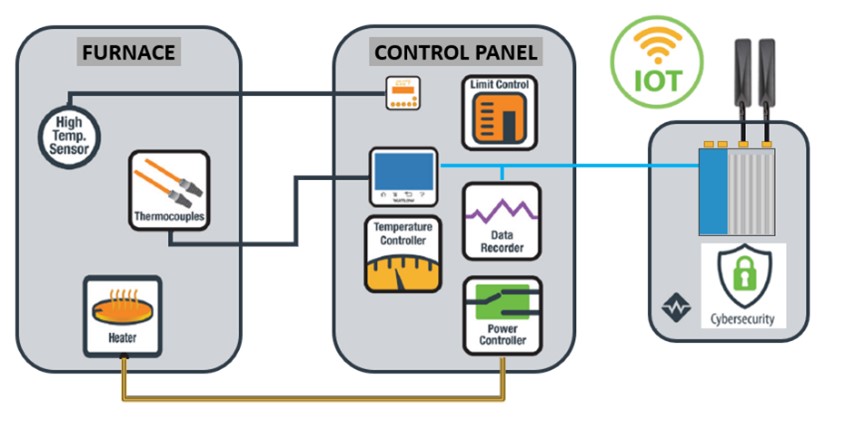
Heat treatment thermal loop solutions are integrated with Industry 4.0 frameworks and data management systems to provide real-time information on performance. Combining artificial intelligence and machine learning algorithms can also provide additional performance benefits, such as the ability to analyze data and identify patterns for further optimization. Ongoing performance losses in a heat treatment system typically come from process drift s. Industry 4.0 solutions can explore these drift s and provide opportunities to minimize these deviations.
Heat treatment thermal loop solutions can be optimized using Failure Mode and Effects Analysis (FMEA). FMEA is a proactive approach to identifying potential failure modes and their effects, allowing organizations to minimize the risk of process disruptions and improve the overall efficiency of their heat treatment processes. Historically, this was a tabletop exercise conducted once per year with a diverse team from across the organization. Updates to this static document were infrequent and were primarily based on organization memory rather than being automatically populated in real time with actual data. There is a potential to produce “live” FMEAs utilizing today’s technology and leveraging insights for continuous improvement.
Th e effectiveness of heat treatment thermal loop solutions can be measured using metrics such as overall equipment effectiveness (OEE). OEE combines metrics for availability, performance, and quality to provide a comprehensive view of the efficiency of a manufacturing process. By tracking OEE and contextual data, organizations can evaluate the effectiveness of their heat treatment thermal loop solutions and make informed decisions about optimizing their operations.
Regulatory Compliance
Nadcap (National Aerospace and Defense Contractors Accreditation Program) is an industry-driven program that provides accreditation for special processes in the aerospace and defense industries. Heat treatment is considered a “special process” under Nadcap because it has specific characteristics crucial to aerospace and defense components’ quality, safety, and performance. Th ese characteristics include:
- Process sensitivity: Heat treatment processes involve precise control of temperature, time, and atmosphere to achieve the desired material properties. Minor variations in these parameters can significantly change the mechanical and metallurgical properties of the treated components. This sensitivity makes heat treatment a critical process in the aerospace and defense industries.
- Limited traceability: Heat treatment processes typically result in changes to the material’s microstructure, which are not easily detectable through visual inspection or non-destructive testing methods. Th is limited traceability makes it crucial to have strict process controls to ensure the desired outcome is achieved consistently.
- Critical performance requirements: Aerospace and defense components often have strict performance requirements due to the extreme conditions in which they operate, such as high temperatures, high loads, or corrosive environments. The heat treatment process ensures that these components meet the specifications and can withstand these demanding conditions.
- High risk: The failure of a critical component in the aerospace or defense sector can result in catastrophic consequences, including loss of life, significant financial loss, and reputational damage. Ensuring that heat treatment processes meet stringent quality and safety standards is essential to mitigate these risks.
Nadcap heat treatment accreditation ensures suppliers meet industry standards January/February and best practices for heat treatment processes. The accreditation process includes rigorous audits, thorough documentation, and ongoing process control monitoring to maintain high quality, safety, and performance levels.
The aerospace industry’s AMS2750G pyrometry specification and the automotive industry’s CQI-9 4th Edition regulations are crucial for ensuring consistent and high-quality heat treated components. Adherence to these regulations is essential for meeting the stringent quality requirements of the aerospace and automotive industries and other industries with demanding specifications.
Temperature uniformity is a crucial requirement of both AMS2750G and CQI-9 4th Edition, mandating specific temperature uniformity requirements for heat treating furnaces to ensure the desired mechanical properties are achieved throughout the treated components. AMS2750G class 1 furnaces with strict uniformity requirements +/-5°F (+/-3°C) provide both quality output and predictable energy use. However, maintaining this uniformity requires significant maintenance oversight due to all the components involved in the thermal loop.
Calibration and testing procedures are specified in the standards to help ensure the accuracy and reliability of the temperature control systems used in heat treat processes.
Detailed process documentation is required by AMS2750G and CQI-9 4th Edition, including temperature uniformity surveys, calibration records, and furnace classifications. This documentation ensures traceability, enabling manufacturers to verify that the heat treat process is consistently controlled and meets the required specifications.

Modern data platforms enable the efficient collection of secure raw data (tamper-evident) and provide the replay and reporting necessary to meet the standards.
Th e newer platforms also off er the latest industry communication protocols — like MQTT and OPC UA (Open Platform Communications Unifi ed Architecture) — to ease data transfer across enterprise systems.
MQTT is a lightweight, publish-subscribe- based messaging protocol for resource-constrained devices and low-bandwidth, high-latency, or unreliable networks. IBM developed it in the late 1990s, and it has become a popular choice for IoT applications due to its simplicity and efficiency. MQTT uses a central broker to manage the communication between devices, which publish data to “topics,” and subscribe to topics that they want to receive updates on.
OPC UA is a platform-independent, service-oriented architecture (SOA) developed by the OPC Foundation. It provides a unified framework for industrial automation and facilitates secure, reliable, and efficient communication between devices, controllers, and software applications. OPC UA is designed to be interoperable across multiple platforms and operating systems, allowing for seamless integration of devices and systems from different vendors.
The importance of personnel and training is emphasized by CQI-9 4th Edition, which requires manufacturers to establish training programs and maintain records of personnel qualifications to ensure that individuals responsible for heat treat processes are knowledgeable and competent. With touchscreen and mobile integration, a significant development in process controls has occurred over the
last decade.

mobile application
By integrating these regulations into a precision control loop, heat treatment thermal loop solutions can provide the necessary level of control and ensure compliance with AMS2750G and CQI-9 4th Edition, leading to the production of high-quality heat treated components that meet performance requirements and safety standards.
Continuous improvement is also emphasized by both AMS2750G and CQI-9 4th Edition, requiring manufacturers to establish a system for monitoring, measuring, and analyzing the performance of their heat treatment systems. This development enables manufacturers to identify areas for improvement and implement corrective actions, ensuring that heat treat processes are continuously improving and meeting the necessary performance and safety standards.
To Be Continued in Part 2
In part 2 of this article, we’ll consider the improved sustainability outcomes, potential challenges and limitations, and the promising future this technology offers to the heat treat industry.
About the Authors
Peter Sherwin is a global business development manager of Heat Treatment for Watlow and is passionate about offering best-in-class solutions to the heat treatment industry. He is a chartered engineer and a recognized expert in heat treatment control and data solutions.
Thomas Ruecker is the business development manager of Heat Treatment at Eurotherm Germany, a Watlow company. His expertise includes concept development for the automation of heat treatment plants, with a focus on aerospace and automotive industry according to existing regulations (AMS2750, CQI-9).
For more information: Contact peter.sherwin@watlow.com or thomas.ruecker@watlow.com.
This article content is used with the permission of heat processing, which published this article in 2023.