Heat Treat 2019 is coming, and one of the great benefits of gathering with a community of heat treaters is the opportunity to challenge old habits and look at new ways of doing things. Heat Treat Today’s 101 Heat Treat Tips is another opportunity to learn the tips, tricks, and hacks shared by some of the industry’s foremost experts.
For Heat Treat Today’s latest round of 101 Heat Treat Tips, click here for the digital edition of the 2019 Heat Treat Today fall issue (also featuring the popular 40 Under 40), and to be distributed in print at Heat Treat 2019, in Detroit, Michigan, October 14-17, 2019.
Today’s Technical Tuesday features 10 Tips from a variety of categories, including SCR Power Controls (56), Cooling Systems (64), Combustion (66, 101), Induction Heat Treating (71), Thermocouples (79), AMS2750 (86), Vacuum Furnaces (92), and Miscellaneous (41, 87). These tips come from the 2018 list of 101 Heat Treat Tips published in the FNA 2018 Special Print Edition. This special edition is available in a digital format here.
Heat Treat Tip #41
Discolored Part—Who’s to Blame?
If your parts are coming out of the quench oil with discoloration and you are unsure if it is from the prewash, furnace, or oil quench, you can rule out the quench if the discoloration cannot be rubbed off. Check this before the part is post-washed and tempered.
Other possible causes:
- Can be burnt oils as parts go through the quench door flame screen
- Poor prewash
- Furnace atmosphere inlet (particularly if it is drip methanol)
Submitted by AFC-Holcroft
Heat Treat Tip #56
Electrical Energy Savings
When we buy a pint of beer we don’t expect the head (or foam) to be ½ the glass. We can get this situation when we pay for our plant’s electricity; we pay for both the working power that drives the process (analogy: beer) and reactive power that doesn’t directly drive the process (analogy: foam/head). The lower the Power Factor the worse this situation. The latest SCR devices can help combat this while maintaining precise control and reducing overall peak load demands (using flexible firing methods).
Submitted by Eurotherm
Heat Treat Tip #64
Buy a Cooling System Capable of Growth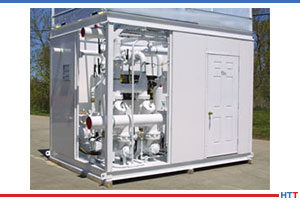
Plan for future growth. It is more cost-effective to provide additional capacity while equipment is being installed. Simple planning for the addition of future pumps (e.g. providing extra valved ports on tanks) and space for heat transfer equipment (e.g. pouring a larger pad or adding extra piers) can save considerable money down the road with little upfront expenditure. Consider installing one size larger piping for the main distribution supply and return. If this is not possible make sure you can add an additional piping run on the hangers you will install now.
Above all, be sure to include all necessary drains, vents, isolation valves, and plenty of instrumentation. These items are critical aids in maintenance and troubleshooting and future system expansion.
Submitted by Dry Coolers
Heat Treat Tip #66
Tune That Burner!
Don’t neglect burner tuning—a 1% reduction in excess O2 in the flue products can save you $1,000.00/year on your IQ batch or $2,000.00/year on a 2000-pound/hour continuous furnace—not to mention consistent temp uniformity, better heat-up rates. Pretty good payback for a couple of hours’ work.
Submitted by Combustion Innovations
Heat Treat Tip #71
Tube & Pipe Heat Treatment Is Different Than Solid Cylinder Heat Treating
Induction heating of tubes and pipes is somewhat different from the heating of solid cylinders. There is a difference in the frequency selection that would maximize energy efficiency for heating tubular products as compared to solid cylinders. In tube and pipe heating, the frequency, which corresponds to maximum coil efficiency, is typically shifted toward lower frequencies providing larger current penetration depth than the tube wall thickness (except for heating of tubes with electromagnetically small diameters). This condition can produce an improvement in electrical efficiency of 10–16 % and even higher. One simplified formula that is used in industry for rough estimate of the electrically efficient frequency is shown in the image, where:
- ρ – electrical resistivity of heated metal (Ω*m)
- Am = average diameter; Am = (Tube O.D. – h) (m)
- h = wall thickness (m)
In cases when induction heaters cannot be considered to be electromagnetically long coils, the values of the optimum frequency will be higher than the values suggested according to formula, and computer modeling can help determining its exact value.
Heat Treat Tip #79
Order SAT Probes All at Once
Place a yearly blanket order for your SAT probes and ask that they are made from the same coil. This will give you the same correction factors and temperature tolerances.
Submitted by GeoCorp
Heat Treat Tip #86
AMS2750 Is Golden
This standard is gold and unfortunately has a bad rap today because companies feel it’s just added cost into the process. Today’s technology means you can afford AMS2750E compliant controllers and digital recorders for only a few hundred dollars above a standard offer. This investment will be paid back many times over due to the longer lifetime expected with a quality instrument as well as the quality benefits from better drift performance between calibration intervals, redundant recording (in case of record loss), and overall accurate temperature control, leading to less rejects and reduced rework.
Submitted by Eurotherm
Heat Treat Tip #87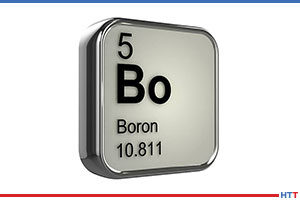
Pay Attention to Material Chemistry
When trying to determine a materials response to heat treatment, it is important to understand its form (e.g., bar, plate, wire, forging, etc.), prior treatments (e.g. mill anneal, mill normalize), chemical composition, grain size, hardenability, and perhaps even the mechanical properties of the heat of steel from which production parts will be manufactured. The material certification sheet supplies this basic information, and it is important to know what these documents are and how to interpret them.
Certain alloying elements have a strong influence on both the response to heat treatment and the ability of the product to perform its intended function. For example, boron in a composition range of 0.0005% to 0.003% is a common addition to fastener steels. It is extremely effective as a hardening agent and impacts hardenability. It does not adversely affect the formability or machinability. Boron permits the use of lower carbon content steels with improved formability and machinability.
During the steelmaking process, failure to tie up the free nitrogen results in the formation of boron nitrides that will prevent the boron from being available for hardening. Titanium and/or aluminum are added for this purpose. It is important, therefore, that the mill carefully controls the titanium/nitrogen ratio. Both titanium and aluminum tend to reduce machinability of the steel, however, the formability typically improves. Boron content in excess of 0.003% has a detrimental effect on impact strength due to grain boundary precipitation.
Since the material certification sheets are based on the entire heat of steel, it is always useful to have an outside laboratory do a full material chemistry (including trace elements) on your incoming raw material. For example, certain trace elements (e.g. titanium, niobium, and aluminum) may retard carburization. In addition, mount and look at the microstructure of the incoming raw material as an indicator of potential heat treat problems.
Submitted by Dan Herring, The Heat Treat Doctor®
Heat Treat Tip #92
Hacksaw Your Hearth!
When loading parts, carefully place the workload on the center of the hearth (front-to-back and side-to-side). Make sure it is stable and no part of the load is close to or touching the heating elements. This can create arcing and damage your parts. Tip: Once the load is in place, mark the hearth posts with a hacksaw to quickly find the front and back measurements each time.
Submitted by Ipsen USA
Heat Treat Tip #101
Can We Achieve Perfect Combustion?
Perfect combustion is based upon the concept of neither excess oxygen or a deficiency of oxygen in the combustion process. This is known as stoichiometric or theoretical combustion. Why is this considered as theoretical and not possible under normal field conditions? Consider the factors that can affect your combustion process: temperature of air or gas, pressure fluctuations, gas composition or supply changes, operating conditions, etc. Therefore theoretical combustion is just that: perfect combustion is only possible in a lab setting. Burner adjustment and calibration normally maintains a minimum of 10% excess air to compensate for these variables and avoid operating gas-rich with high levels of CO in the combustion process.
Submitted by WS Thermal