When it comes to optimizing the working life and overall performance of heat treatment alloy castings, proper alloy selection and design based on the intended application is a critical starting point. Discover the variables behind alloy selection and design and the additional factors that contribute: furnace maintenance, casting inspection, and cost reduction strategies.
This Technical Tuesday article was composed by Matthew Fischer, manager of Technical Sales, Castalloy Group for Heat Treat Today's August 2023 Automotive Heat Treating print edition.
Alloy Selection and Design Criteria

Manager of Technical Sales for Heat Resistant Products
Castalloy Group NA
Source: Castalloy Group
Optimal design and alloy composition for any heat treatment casting always requires careful consideration of a number of key operating variables. This is the only way to guarantee the part will deliver maximum utilization and efficiency for the intended application.
These variables include:
- Anticipated service and maximum operating temperature
- Size, orientation, and weight of the load
- Thermal cycling and/or quenching
- Range of temperature cycling
- Frequency of temperature cycling
- Rate of change of temperature
- Type of atmosphere or other corrosive conditions of the application
- Type of quenching or cooling
- Size, shape, and weight of part(s)
- How are the parts loaded and oriented? (e.g., manually, robotically, individually, bulk)
- How is the alloy supported in the equipment? (e.g., rails, hearth, rollers, piers)
- Additional processing requirements (e.g., machining, welding)
- Abrasive or wear conditions
- Ease of use (ergonomics) and replacement
- Cost — initial and total cost of ownership
In addition, there are fundamental factors that heavily influence optimal component design and alloy composition. For instance, the type of furnace used (e.g., box, pit, integral quench, continuous), alloy handling mechanism (fixture and tray), and application process (e.g., carburizing, normalizing, annealing, austempering, vacuum heat treating) all have an important role to play. It is worth noting, however, that the decision-making process is a fine balancing act that isn’t necessarily evenly weighted. While a specific alloy composition may Fiaddress the majority of performance needs, it may hinder others. Prioritizing end-use performance traits is therefore essential.
Furnace and Process Environment Maintenance
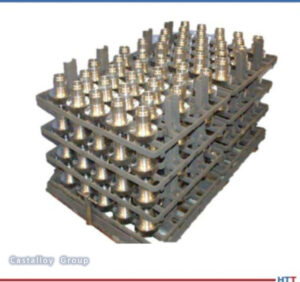
Source: Castalloy Group
How furnaces and processes are performance monitored and maintained is also key when seeking to optimize the performance and lifespan of heat treatment alloy castings. The specific type of furnace will dictate exact equipment and process maintenance requirements, but there are several universal best practice procedures and guidance processes that should be followed.
For instance, the Automotive Industry Action Group (AIAG) has established CQI-9 (Continuous Quality Improvement) standards for heat treatment. These standards provide the guidelines for a continuous cycle of assessment, planning, and improvement with respect to heat treat processing and due care of handling customer parts. The CQI-9 standards direct the heat treater to have and maintain the necessary equipment and associated control instruments used to monitor and record the furnace process operating parameters. They also promote the proper furnace operating process environment. However, the standards do not comprehensively address the overall maintenance requirements of the furnace and process environment equipment. Generally, yearly scheduled maintenance is important to the long-term successful continuous operation of furnace equipment. Lack of or intermittent maintenance can lead to unplanned shutdowns. Here are some of the most common maintenance issues to monitor and remedy:
Example 1: Support Misalignment
If base tray support mechanisms are in alignment (in the direction of travel) and flat (level throughout) to provide proper support of the base tray and associated fixtures and parts, then the tray should move through the furnace equipment without issue, provided the tray is in good operating condition. However, if there are broken rails or piers — or broken/deformed roller rails or wheels — then over time the tray may exhibit wear, deformation, cracks, or breaks.
Example 2: Transfer Mechanism Misalignment
If the transfer mechanisms are square to the tray (in the direction of travel) and level throughout, providing proper contact with the base tray, then the tray should move through the furnace equipment without issues, provided the tray is in good operating condition. However, if there are misaligned transfer mechanisms (pusher rods, pusher head, handler head etc.), then over time the tray may exhibit associated wear, deformation, distortion, cracks, or breaks.
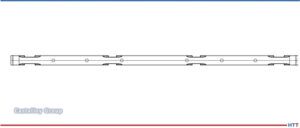
Source: Castalloy Group
Example 3: Uneven Heating
Although the furnace may be able to maintain an average furnace temperature as measured by a single control thermocouple, there may be uneven heating conditions (side-to-side, top-to-bottom, front-to back) due to a variety of factors, which could result in uneven thermal cycling of the alloy castings. This potential non-uniform heating of the alloy could lead to deformation, cracks, or breaks of the alloy castings. The CQI-9 standards work to monitor and address non-uniform heating using a periodic temperature uniformity survey (TUS) of the furnace heating chamber.
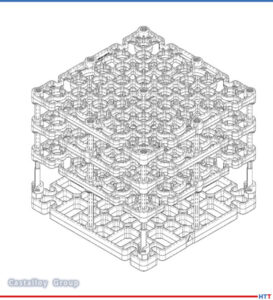
Source: Castalloy Group
Example 4: Non-Uniform Cooling
Although the quench chamber may be able to maintain an average quench medium temperature as measured by a control thermocouple, there may be uneven cooling conditions within a load due to a variety of factors, which could result in uneven thermal cycling of the alloy castings. If left unchecked, any of these issues may result in unintended wear, deformation, distortion, cracks, or breaks of the alloy castings. Furnace material handling issues may also result in an unplanned equipment downtime and productivity loss.
Alloy Castings Inspection
Alloy castings (fixtures, trays, grids) should be inspected periodically to ensure they are in adequate working order. This inspection could be performed when the furnace equipment is taken out of operation for summer or winter maintenance inspections and shutdowns. The main areas to consider are flatness, squareness, and proper proportion.
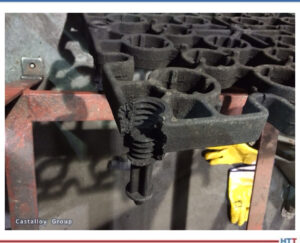
Source: Castalloy Group
Flatness
Trays, grids, and fixtures should remain flat or level across the width and length. Sagging, bowing, warping, or twisting can cause material handling issues within furnaces and associated process equipment. A simple method to check the flatness is to have a table with a flat and level surface where the tray, grid, or fixture may be placed to check and observe the flatness of the alloy casting. An alternate method to check the alloy casting flatness would be to use a level across the casting to check flatness.
Squareness
Trays, grids, and fixtures should remain square across the width and length. Being out of square can cause material handling issues within furnaces and associated process equipment. A simple method to check the squareness is to have carpenter’s square tool where the tray, grid, or fixture may be examined to observe the squareness of the alloy casting.
If the tray used in the heat treatment equipment is an assembly of trays, then each tray should be examined for squareness in all four corners. Trays that are out of square may cause tracking problems in the material handling of the furnace, or associated equipment, and should be replaced.
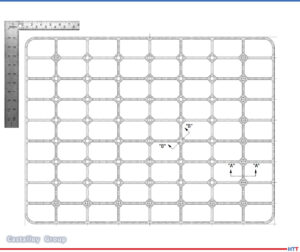
Source: Castalloy Group
Proper Proportion
Trays, grids, and fixtures should remain in proper proportion as originally designed. Having bulges or large breaks that are outside of the alloy dimensional alignment compared with the originally supplied alloy casting can cause material handling issues within furnaces and associated equipment. A simple method to check the dimensional proportion is to have a picture or drawing of the originally supplied alloy casting. The tray, grid, or fixture can be compared with this in order to observe the overall soundness of the alloy casting. Suspect castings should be removed from daily operation to prevent potential material handling and associated equipment maintenance issues. An alternative to visual inspection is to make a simple jig that can be used to confirm the dimensional integrity of the alloy casting. Observable patterns of proportional changes within a common area of the alloy castings may indicate a potential issue occurring within the heat treat equipment that should be monitored and investigated before it becomes a major equipment issue and causes an unplanned equipment shutdown.
Optimizing Alloy Castings Using Periodic Purchases
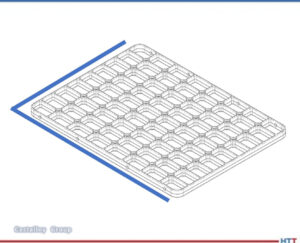
Source: Castalloy Group
Periodic purchases of alloy castings should be planned and budgeted annually to maximize casting working life, to minimize process interruptions due to potentially expired useful life of alloy castings, and to manage future expenditures for replacement alloy casting purchases.
In general, budgeting for a percentage of alloy purchases over a two to three- year period, depending on current and planned future operations, would be supportive of continuous production operations. The periodic alloy purchase is then integrated into the existing production operations and suspect alloy castings, if any, can be removed from daily production operations.
There are multiple approaches that can be implemented and adjusted according to individual plant production needs:
One approach to consider is the purchase of one-third of the total alloy purchase per year over the following three years after an initial purchase. In a continuous daily production operation, the initial purchased quantity of alloy castings will have been replaced, if needed, over the elapsed time.
An alternate approach to consider is a staggered percentage over three years. For example, 20–25% replacement the first year; 30–35% replacement the second year; 35–40% replacement the third year, adjusted as necessary based on current operating and business conditions.
This approach would also be useful for ramping up alloy quantity needs to meet increasing demand over time and could be an opportunity to address potential delivery time requirements with coordinated planned periodic purchases.
Additionally, intermixing newly purchased alloy castings along with production alloy castings, may provide for extended life for the latter.
Scrap Alloy Recycling: New Alloy Purchase Credit for Returning Your Scrap Alloy Material
When alloy castings are no longer usable in daily heat treatment operations, it can be advantageous to sell them back as scrap to the alloy supplier. The supplier should be able to provide a scrap repurchase credit that can be used for future purchases of new alloy castings.
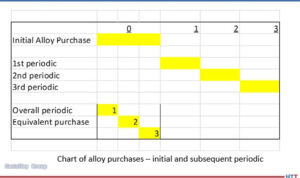
Source: Castalloy Group
Generally, this scrap alloy repurchase credit may be used in whole or in part as directed by the customer for new replacement alloy casting purchases.
As well as being cost-efficient, scrap alloy castings recycling supports the long-term sustainable use of metals, minimizes the potential negative impact on the earth’s environment, and reduces the overall carbon footprint of both alloy user and supplier.
Summary
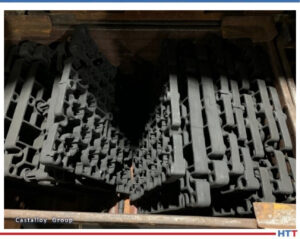
Source: Castalloy Group
To review, improving the working life of heat treating cast alloys starts with design and is maintained with factors that account for the full alloy casting life:
- Choosing the right design and alloy composition for heat treatment castings is fundamental to optimizing their working longevity and performance. This decision can only be made by carefully considering key aspects of the intended casting
- Maintaining furnace equipment and process environment operating conditions will also assist in maximizing the working life and overall performance of the alloy castings.
- Alloy casting inspection will support heat treat operations and minimize potential equipment downtime by providing evidence of furnace equipment issues or malfunction.
- Periodic budgeted alloy casting purchases support heat treat operations, will help maximize uptime, and minimize potential downtime associated with suspect or failing alloy castings.
- Scrap (expired useful life) alloy repurchases can be used to off set the costs associated with new alloy casting purchases. Scrap alloy recycling also minimizes negative impact on the environment.
About the Author:
Matthew Fischer is the manager of Technical Sales for Heat Resistant Products at Castalloy Group NA. He has thirty years of experience in furnace design and applications working for a leading heat treat furnace equipment supplier. Additionally, he has worked for several years as a senior heat treat manufacturing engineer for a global tier-1 automotive company as well as in the controls and instrumentation fields across multiple industries, including thermal processing and heat treating.
For more information:
Contact Matthew Fischer at Matthew.Fischer@castalloygroup.com