Clifford-Jacobs Receives Improved Temperature Control System on Heat Treat Equipment
In today’s Heat Treat Today Technical Tuesday feature, learn more about how a temperature control system can improve the performance of heat treat equipment.
A century-old producer of die forgings recently needed to improve the process controls on its heat treating furnaces.
With process controls well over 10 years old, Clifford-Jacobs turned to Conrad Kacsik to improve its temperature process control system. The company, which serves a number of industries, including energy, aerospace, construction, mining, forestry, and rail, was eager to upgrade, particularly because the incumbent system was producing inconsistent work.
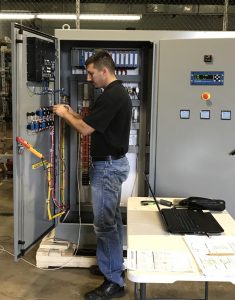
The Challenge
Clifford-Jacobs was not getting consistent, repeatable results from its furnaces. The company also wanted more efficient and automated processes with data acquisition and electronic operating capability.
“We looked at a number of controls companies throughout the Midwest and interviewed them to learn about their experience with system controls and data acquisition,” said Bud Kinney, vice president of Innovation and Technology at IMT Corporation, the parent of Clifford-Jacobs. “We knew we wanted an integrated system so we started looking at companies that did that as a matter of course. Most companies are limited to traditional controls, but Conrad Kacsik has a lot of experience doing the exact type of job we needed.”
Increasing Demands
Clifford-Jacobs makes forged parts for a variety of clients. Although forging does not generally require as much precision as other types of processes, customers are increasingly demanding, said Kinney.
“We believe that sooner rather than later things like Nadcap will come into forging, and our customers are very interested in us being able to demonstrate that our processes are always in control, even forge heating,” Kinney said. “This project helps ensure that we meet those needs. We couldn’t track things like set-point input values before. That’s another element we wanted to manage.”
The System
Conrad Kacsik built a full process temperature control system that includes SCADA software from SpecView. They were able to retrofit the system on Clifford-Jacobs’ existing 16 furnaces, saving the company considerable expense and time. The temperature process control system uses Watlow F4T controllers paired with SpecView SCADA software, which allows for programming jobs/recipes, remote operation, secure (password protected) operation of furnaces, and accurate automatic temperature recording. Conrad Kacsik also added alert lights that allow the operators to quickly see the status of each furnace from the shop floor.
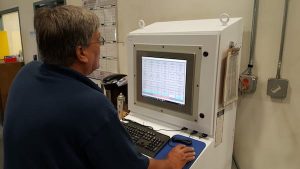
H2: Benefits of Temperature Control System Integration
Clifford-Jacobs has noted several beneficial results from the new temperature control system. These include:
• Increased accuracy. The new system runs each recipe exactly and records the results. The company can also control which employees can adjust temperature settings, preventing operators from rushing jobs with a higher temperature or inadvertently setting the furnace incorrectly.
• Higher efficiency. With preprogramming, each furnace is always at the exact temperature it needs to be for the given task. An automatic preheat setting also safely prepares the furnace for the workday—eliminating downtime or the need to send an employee in early to start the furnaces.
• More speed. Clifford-Jacobs can preprogram any recipe it needs, allowing for highly accurate and fast running of complex processes.
• More convenience. Clifford-Jacobs can operate their furnaces from anywhere with an internet connection, or via an iPad used by an approved employee.
• Precision for the future. The new system can be part of a Nadcap-approved process should the need arise. The SpecView software and advanced controllers automatically record each job and retain all data for verification.
The Results
“We used to have to use all kinds of resources to provide oversight on temperature control,” said Kinney. “This has given us a heating strategy. We write the recipes we want and just select from
those. In addition to that, we know exactly what every furnace is doing at all times.”
The company is also pleased with the increased efficiency. They only heat product when they are ready to run production, and the furnace only uses the exact energy needed for each recipe. They are also saving on staffing, as they used to have to schedule people to ensure the furnace was at the right temperature.
“With this system, we can develop recipes for each part we make, which is both convenient and precise. It’s doing exactly what we expected it to do,” said Kinney.
This article first appeared in December’s Heat Treat Today‘s Medical and Energy Heat Treating magazine.
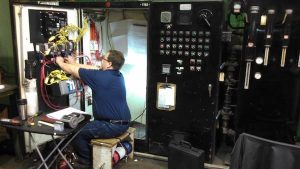
Clifford-Jacobs Receives Improved Temperature Control System on Heat Treat Equipment Read More »