How To Tell If You Really Have an Abrasion Problem
Understanding abrasion can be the key to extending the life of your refractory lining. The following article provided by Plibrico Company examines abrasion resistance, its role in choosing a refractory solution, and what factors to take into consideration when assessing counter-measures.
Refractory material is designed to be very durable, withstand extreme service conditions and defy mechanical abuse in many different types of thermal-processing operations. However, severe conditions that cause abrasion in the form of high levels of mechanical scraping and airborne particulate matter can challenge refractories, shortening their service lives.
Abrasion resistance is one of the most critical and possibly the most misunderstood considerations when choosing a refractory solution. A clear understanding of what abrasion is and, perhaps more importantly, what it is not can prevent needless repair costs and lead to significant savings. This is especially important when evaluating refractory designs for a new application or when considering upgrades for an existing one.
What Abrasion Is
Abrasion is the destructive process that causes a material to wear away through mechanical scraping or scratching. Anyone who has ever grated cheese or sanded wood has experienced the abrasion encountered in everyday life. As abrasion continues, thin layers of the abraded material are removed, leaving the object thinner and usually making its surface smoother.
The same process can be observed in the refractory world. Refractory linings are abraded by high-velocity airborne particulate, cleaning tools and fuel/process materials that pass through the unit and come into contact with the lining. The telltale sign of abrasion is a refractory lining that has steadily become thinner while its surface has become smoother. The surface may even shine as if it had just been polished, which is not surprising when we consider that polishing is another common form of abrasion.
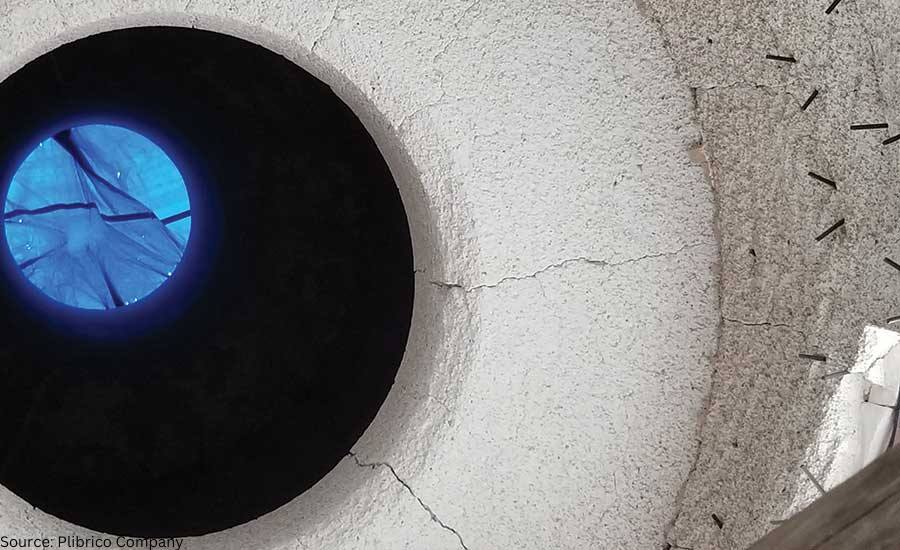
What Abrasion is Not
Abrasion is considered a type of mechanical abuse, but it is not the only type of mechanical abuse to which refractory linings are subjected. Equally common is impact: the sudden, forceful collision between the refractory lining and a moving object. Impact can come from a variety of sources. The moving object may be a cleaning tool, a piece of process material, a chunk of fuel or a dislodged mass of refractory or slag, depending on the application. Impact with such objects typically results in chips and cracks in the refractory lining.
Refractory materials designed for abrasion resistance tend to have increased strength and hardness compared to those found in traditional refractories, and these abrasion-resistant materials may provide some resistance to impact. Abrasion-resistant properties can also lead to increased brittleness. This is because if the impact exceeds the strength of the material, chipping and cracking could potentially be worse than in traditional refractories.
Compression and tension are also forms of mechanical abuse and can be caused by changes in the shape of the refractory lining as it is heated or cooled or by movements of the furnace shell itself – by intentional design or otherwise. Here again the increased strength and corresponding brittleness of the material could potentially result in a negative effect on the refractory lining.
All types of mechanical abuse can cause thinning of the refractory lining, so it is important to conduct a detailed investigation into the destructive mechanism before drawing any conclusions. Refractory solutions designed to resist abrasion may not be helpful against damage caused by impact, compression or tension.
Similarly, solutions designed to address other types of mechanical abuse may be ineffective against abrasion. For example, stainless steel needles are commonly incorporated into refractory linings to extend service life when impact resistance is required. The needles bridge cracks formed as a result of the impact, making it more difficult for these cracks to grow and connect. This helps the refractory lining hold together longer. The bridging provided by needles has no effect in an abrasion situation, however, since crack growth is not caused by the abrasion process.
Meeting Abrasion-Resistance Demands
Once abrasion is identified as the main mode of failure, there are several options to counter it. Selecting a refractory material based on a raw material hard enough to resist the abrasion is a common technique. For one material to abrade another it must be harder than the material being abraded. For instance, a diamond can be used to scratch glass, but glass cannot be used to scratch a diamond.
It follows that refractory materials based on very hard raw materials, like silicon carbide, can be used to resist abrasion and extend the life of the lining. It should be remembered, however, that a refractory lining is made up of many different materials, not just the main constituent raw materials. Clay, cement, silica and other softer components will still be exposed and abraded even if abrasion of the main aggregate is stopped completely.
Another option is to investigate the source of the abrasion and make adjustments to the process. Can a less-abrasive cleaning tool be used? Is there a way to limit the contact of the abrading process materials with the refractory lining? Is it possible to adjust the angle between the refractory lining and the incoming airborne particulate?
A seemingly minor change in the process, with minimal cost and no downsides to the operation, can save in refractory replacement costs. When changes to the process are not an option, it is best to consider the abrasion resistance of the lining as a whole and select a specifically designed abrasion-resistant solution. A qualified, knowledgeable refractory solution expert with genuine experience will help you make the best decision for your specific application, taking into consideration the following:
- Speed of installation
- Service life
- All-in price
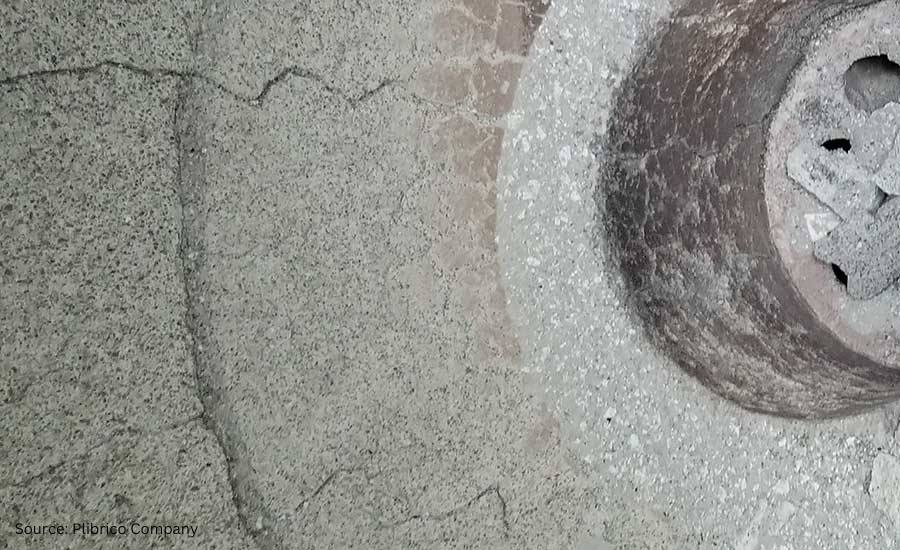
Abrasion-Resistance Testing
The most common measure of holistic abrasion resistance used to compare refractory solutions is the ASTM 704 test. This test exposes refractory lining materials to a stream of abrasive particulate that cause a portion of the sample to be abraded over time. By keeping sample size and shape constant – along with particle velocity, particle material and test duration – various refractory materials can be compared on an apples-to-apples basis.
This testing can be performed by any qualified refractory testing lab and most reputable refractory manufacturers. Test results are recorded based on the volume of material lost from the sample during the test and are reported in cubic centimeters. Products with excellent abrasion resistance consistently test at 5 cc of loss or less, while elite materials can score less than 3 cc of loss.
Products designed specifically for abrasion resistance will report ASTM 704 results on their material technical data sheets. It is important to remember that the abrasion-loss numbers reported on material technical data sheets are based on samples prepared in a lab under controlled conditions. Achieving these same properties in the field under real-world, job-site conditions would require a high-quality refractory installer partnered with a world-class refractory manufacturer.

Conclusion
The thinning of a refractory lining due to abrasion is a source of frustration for many thermal-processing operations and is one of the most common modes of failure encountered in the refractory world. But, by taking the time to understand the failure mechanism and learn about the options available, you can realize significant savings by avoiding needless costs in the future.
Learn more at www.plibrico.com.
This article was initially published in Industrial Heating. All content here presented is original from the author.
Find heat treating products and services when you search on Heat Treat Buyers Guide.Com
How To Tell If You Really Have an Abrasion Problem Read More »