This week’s Technical Tuesday installment is a Heat Treat Today original that was first published in the Heat Treat Today Automotive magazine in June 2019.
This industry is richly endowed with a heritage of experienced metallurgists and skilled professionals. This era is one of innovation and trends – especially in automotive manufacturing. How does the heritage of the industry and the vision of the future come together? We’ve compiled input from a selection of Heat Treat Today’s own industry experts on a question about new stuff going on in both the labs and the shops. (To see what other fields and specialties our Heat Treat Consultants work in, go to: www.heattreattoday.com/consultants)
Question: “Thinking about the automotive heat treating industry, what is one of the more interesting, innovative or helpful technologies, processes, materials, or products that you’ve seen recently?”
The Heat Treat Brain Trust Responds:
Sandra Midea
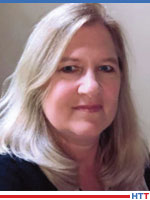
I’ve had the opportunity to work first hand with an induction company in North Royalton, Ohio, (Induction Tooling Inc.) to create an in-house facility that develops and validates induction heat treating processes. The objective was to create a space with the right equipment and personnel where induction processes and tooling could be tested—to innovate, to provide proof of concept, to troubleshoot, and/or to validate processing parameters, in the most streamlined process available. For the automotive industry,
the lab has been used to reduce the time required to get products/processes ready for the PPAP. Bill Stuehr, the company’s president and CEO, had the vision that induction process development could occur rapidly by condensing the design, manufacturing, development, testing, and characterization and metallurgical validation processes all into one facility. With seven power supplies from different manufacturers and three material handling systems available for induction process development, an automotive supplier’s production induction heat treating department can be mimicked for power, frequency, quench & quench method, and material handling methodology. This allows incremental process and tooling development to occur in a laboratory environment without the cost of breaking into production.
This development facility is backed up with an ISO 17025 commercial metallurgical testing laboratory. Sample parts are checked for appropriate microstructure, grain size and hardness requirements and reported to the customers. Initial lots of evaluation parts can also be produced. This allows the inductor and process to be developed and validated before the tooling ships to the heat treating customer. While some process tweaks may need to occur at the final facility, the time required for a company to be ready to begin the PPAP process can be significantly reduced.
Max Hoetzl
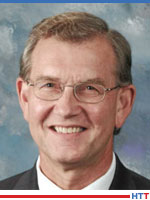
One of the most interesting things I’ve seen in the automotive heat treat industry is the use of robots to load and unload furnaces. The use of robots has significantly improved the operation in many ways.
Following are some of the examples:
- Remove humans from hazardous environment,
- Increase throughput,
- Provide part loading for uniform thermal treatment.
Joe Benedyk
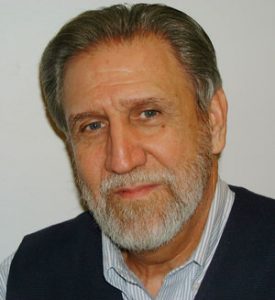
Reducing Heat Treatment Time in the Precipitation Hardening of Aluminum Alloys
Strengthening aluminum alloys through the precipitation hardening process by solution heat treatment and aging is considered a fundamental step in the manufacturing of high strength-to-weight products that meet performance requirements in both the aerospace and automotive industries. The automotive industry is focusing on 7xxx alloys because of their high strength. Among the high strength 7xxx (Al-Mg-Zn) alloys is the mainstay alloy 7075, which can achieve a tensile strength of as high as 80 ksi when age hardened to a -T6 temper. However, to achieve these high strength levels in 7075 alloy at conventional aging temperatures requires aging for 24-48 hours, a stumbling block to its application in automotive products.
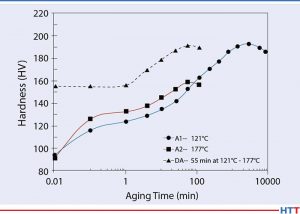
Research at the Illinois Institute of Technology Thermal Processing Technology Center has shown that by selectively double aging 7075 alloy, the aging time to achieve maximum hardness and strength can be reduced to as low as two hours under laboratory conditions (see Figure 1) or demonstrably much shorter aging times in an extrusion plant trial. The obvious advantages of significantly shorter aging time for 7075 and other heat treatable aluminum alloys are not only energy savings but also increased plant productivity through much reduced processing time. The begged question of applying the double aging process to other heat treatable wrought aluminum alloy systems is under review.
Jim Senne
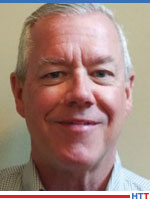
PSA generated nitrogen has become increasingly popular for use in heat treating applications, and at a fraction of the cost, due to advances in PSA technology. Typical cost per standard unit volume are 15% to 25% of the cost of bulk liquid nitrogen. Purity can range from 95% to 99.999%, however many processes demand less than full purity. PSA technology can dial into the specific requirement, making it even more economical. The equipment has excellent reliability and requires only general maintenance on the associated air compressor and periodic filter changes. As well, the CMS (Carbon Molecular Sieve) material can last 20+ years. Processes that require a nitrogen cover gas are particularly well suited, such as induction hardening, tempering, and stress relieving. Other suitable applications include nitrogen/methanol atmosphere, FNC, N2+scavenger gas mixes, and purging.
Matt Orfe
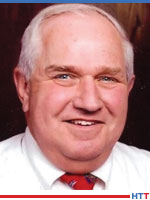
One of the most impressive pieces of equipment that I’ve seen in use in VAB (vacuum aluminum braze) furnaces in the automotive industry would be the in-furnace data loggers for monitoring the temperature of the parts being brazed. The instrument is loaded into the VAB furnace with the parts to be brazed and wirelessly transmits the temperature data through the furnace chamber wall to the receiver/monitor.
This eliminates the need to plug in thermocouples with the furnace door opened, as the load sensors can be attached to the unit prior to insertion into the chamber.
Multiple thermocouples can be used with the system and multiple data logger units can be used for high volume applications. Very accurate, very easy-to-use, and very impressive!
Debbie Aliya
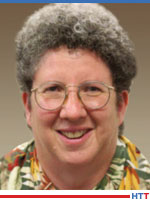
My instant response is always that the most innovative, interesting, and helpful technologies are educational in nature— the knowledge that allows people to make the best use of the common materials that still form the foundation of our industry. How many products would be more reliable if people properly selected, specified, and inspected the heat-treated materials that they use? How many products would be more reliable if the purchasing and specifying functions had a realistic idea of how much variation they should expect in a given part, lot, from lot to lot, and over an extended period of time? For example, how many people in engineering and purchasing know what a furnace uniformity survey is?
Purchasing often does not want to use an alloy steel, but if they need uniformity of strength, and there are different section thicknesses, they may save money and headaches if they pay the extra up-front to get the hardenability into a range that will provide consistency.
How many companies have minimum hardness or case depth specifications, without an upper limit? If the parts are to be electroplated, they increase the risk of hydrogen embrittlement, an issue that seems to come around in the industry every 10 years or so.
It wasn’t an automotive company, but I have had at least one client specify a quench and temper heat treatment for an HSLA (high strength low alloy) steel, which completely defeats the purpose of the HSLA grade system.
There are still a lot of people doing design work who think that calling out a composition requirement gives a certain strength level. For many of the European and Asian steel specifications, this is true, but the American specifications are often for composition only.
How many companies still do not require lot traceability? In the automotive world, if it’s a critical part, traceability is generally required, but there are still a lot of parts that fall through the cracks.
Doug Shuler
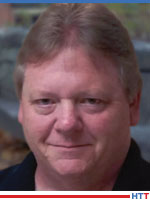
The most interesting thing I have seen in the automotive heat treating industry is a new pyrometry technology software system known as C3 Data.
This solution enables those in the heat treatment industry to comply with specific industry quality requirements of pyrometry, saving enormous amounts of time in the process.
While C3 Data is currently better known in the Nadcap world for their solution for AMS2750, their new CQI-9 version should be something that heat treaters in the automotive world consider.
This fits with my motto of working smarter—not harder!
Irwin Brown
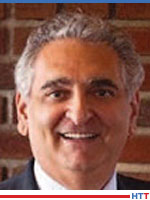
Nowadays, the heat treating industry, especially automotive, enjoys an abundance of riches. We are witnessing increased business volume coupled at the same time with efficient new equipment and technologies, such as additive manufacturing, AI, supply chain improvements, and amazing software. So, why are so many thermal processors unable to raise EBITDA? We are also witnessing critical worker shortages as well as many current employees voluntarily resigning in record numbers. What is the secret to improved quality and increased profits? In our work with industry clients, we found a way to lead employees to better serve customers, thus unlocking vast potential. This strategy, based upon a little deployed thirty-year old method, provides a rapid turnaround that makes productivity soar.
This “secret sauce” is Servant Leadership, which remains the best and most useful technique for transforming difficult relationships among modern multi-cultural employees. Old style command-and-control employers hesitate to recognize and acknowledge how decades-old management behavior is unsustainable with today’s workforce. More enlightened owners, in their own self-interest, value a more dedicated workforce. Employees do not leave companies; employees leave their managers.
Servant Leadership permits owners to run their business rather than having the business run them. Building strong, working relationships creates positive results and is not soft leadership. As Ken Blanchard likes to say, “the power of love beats the hell out of the love of power.” Servant Leadership costs nothing and has proven it can spearhead a rapid turnaround.
Dan Herring
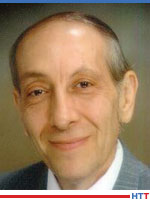
Intriguing question. In my mind, it is the emergence of the electric car and the innovations it will spawn. The motivation is there: a new generation that demands to be green, countries such as China passing laws on vehicle energy reduction (a so-called energy vehicle score), and technological improvements. Battery performance is rising (distance per charge), battery costs are falling (potentially lowering vehicle cost), battery life is up, and weight reduction is a reality. Another reason is the simplicity it brings to the vehicle (the absence of a multi-speed transmission, for example) and a reportedly lower cost for common repairs (this might be a bit misleading as one has only internal combustion engine vehicles to compare with).
While the transition has begun, I feel there are two major hurdles to overcome. First is infrastructure. A massive investment is required to make recharging as available to the public as stopping now to get gas. Every gas station in any country in the world must be mandated to have multiple charging stations. The hidden issue here, both domestically and around the world, is that it will require changes in the law – and the fossil fuel lobbyists are powerful, well established, and entrenched in the government sector. Also, the cost of electricity (in some regions of the world) is not price competitive. Second is public perception. Yes, everyone wants one, but who wants to be first? The phrase I like to use is that John Q. Public doesn’t mind being on the cutting edge, he just doesn’t want to be on the bleeding edge.