Aluminum Caster Expands Facility, Technology Capabilities, Including Heat Treatment
An aluminum casting producer in New Hampton, Iowa, announced ongoing plans to expand its plant and technical capabilities, including space to house expanded heat treatment operations, to keep up with growing demand. ATEK Metal Technologies ships thousands of aluminum castings each day and has recently completed a significant expansion of its metal casting, heat treatment and finished machining capabilities. The major building expansion is expected to be completed in December of 2018.
“We need additional plant space to support growth,” said Tom Christie, president of ATEK Metal Technologies. “The new building will allow us to consolidate our warehousing and shipping areas and make room on the plant floor for ongoing expansion of operations.”
On the technical side, the new robotic de-gating and deburring of castings operations will be operational in July 2018.
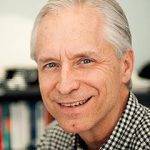
“We added 40 percent to our low-pressure permanent mold casting capacity to keep up with our accelerating growth,” said Christie. “We also have added state-of-the-art precision machining capabilities to be able to provide our customers with cast and machined finished components.”
ATEK Metal Technologies supplies aluminum castings that meet specifications for motorsports, recreation, transportation and industrial markets industries. The entire plant expansion is scheduled to be complete by the end of 2018.
Aluminum Caster Expands Facility, Technology Capabilities, Including Heat Treatment Read More »