Japanese Bearings Maker Opens New Plant with Heat Treating in TN
Source: The Rogersville Review
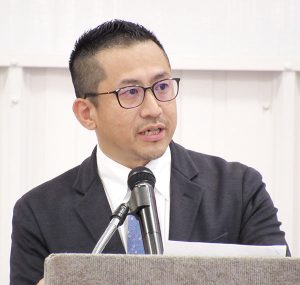
A Japanese bearing manufacturer which incorporates heat treating into its processing recently celebrated the opening of its new 48,000-sq-ft plant in Phipps Bend Industrial Park in Surgoinsville, Tennessee.
This is Miyake Forging’s first expansion into North America. The company currently operates in Japan and Thailand, producing bearings and components for bearing assemblies for the automotive industry. Bearing the name Miyake Forging North America, the facility was built to adapt to growth and allow for expansion.
“I have a great feeling about opening our new facility in Hawkins County. At Miyake, we are very happy to expand our business in the United States of America. We are extremely thankful to all of the people who helped make this happen.” ~ Akitsohi Fujikawa, president of Miyake Forging North America Corporation
Photo credit and caption: The Rogersville Review, Miyake Forging North America company officials and representatives after the ribbon-cutting.
Japanese Bearings Maker Opens New Plant with Heat Treating in TN Read More »