Amsterdam Auto Aluminum Supplier Increases North American Footprint
An Amsterdam-based aluminum supplier recently announced the opening of its new automotive structures plant in San Luis Potosí, Mexico, to supply aluminum crash management systems and structural components to automakers in Mexico.
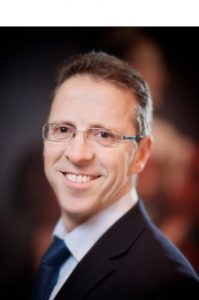
Constellium’s new facility in San Luis Potosí houses the latest technology for forming, machining, welding, and heat-treating aluminum automotive components, along with a state-of-the-art quality lab, in order to respond to the automotive industry’s expectation that “more than 5 million vehicles will be assembled annually in Mexico by 2020, making it one of the largest markets for automobile production,” according to company officials.
“It is an exciting day for Constellium as we expand our footprint in North America to better serve our customers and become part of the growing automotive industry in Mexico,” said Paul Warton, president of Constellium’s Automotive Structures and Industry business unit. “The San Luis Potosí plant is well-positioned to serve multiple customers, and to provide advanced aluminum solutions as the industry trend to electric vehicles gains momentum.”
The Governor of the State Juan Manuel Carreras López was present at the grand opening, along with the Secretary of Economic Development of the Government of the State, Gustavo Puente Orozco; the delegate of the Secretary of Labor and Social Welfare Edgar Durón Puente; and Octavio Martínez Angulo, general director of the plant.
Last year Constellium opened a new plant in White, Georgia, to supply automakers in the southeast U.S., in addition to its existing location in Van Buren, Michigan. A new joint venture (Constellium-Can Art) plant near Windsor, Ontario, Canada, called Astrex, produces aluminum extrusions for Constellium’s automotive projects in North America.
Amsterdam Auto Aluminum Supplier Increases North American Footprint Read More »