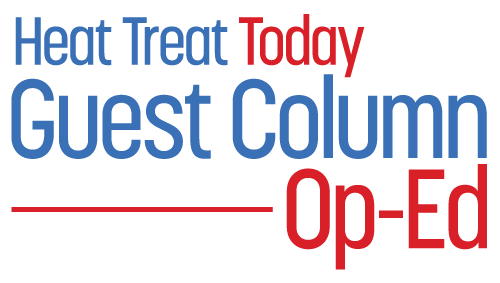
The Heat Treat Doctor® has returned to offer expert advice to Heat Treat Today readers and to answer your questions about heat treating, brazing, sintering, and other types of thermal treatments as well as questions on metallurgy, equipment, and process-related issues.
This informative piece was first released in Heat Treat Today’s May 2025 Sustainable Heat Treat Technologies print edition.
Stress relief is a heat treatment operation primarily intended to reduce or redistribute the internal stresses present in steel and other materials that were introduced from various manufacturing processes like bending (see Figure 1), drawing, rolling, shearing, forging, sawing, machining, grinding, milling, tuning, welding, etc., as well as from prior mill processing. The application end use of a part ultimately defines its allowable stress state. So, what is it, and how does one perform a stress relief operation? Let’s learn more.
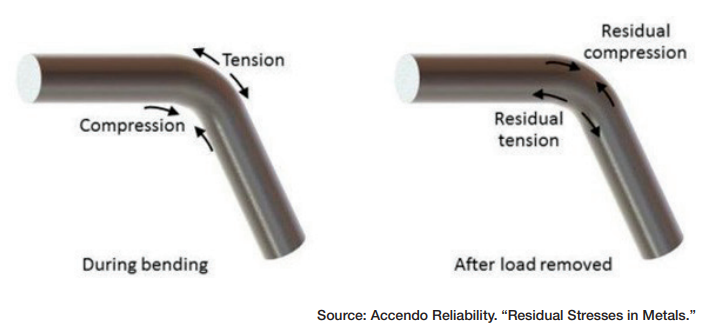
How Does It Work?
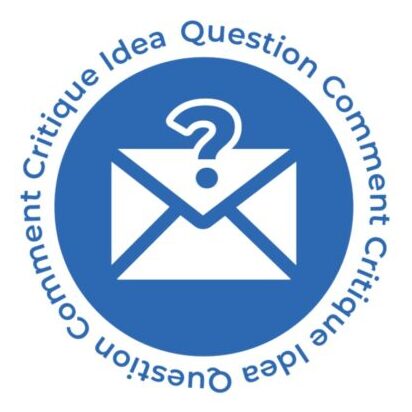
Processes that depend on slow cooling (e.g., annealing, normalizing, stress relief) do so for a variety of reasons: to soften a material for subsequent operations (e.g., machining), to improve chemical homogeneity, to refine grain size, to relieve stresses, and for such reasons as embrittlement relief or magnetic properties (see Haga, L. J.). Residual stresses can compromise a material’s mechanical properties, leading to issues such as warping, cracking, and premature failure under service loads. As a general rule, the larger or more complex the part and/or the more aggressive certain manufacturing processes, the greater the amount of internal stress present.
Stress relief can be differentiated from other slow cooling processes in that it is most o en performed below the lower critical temperature (Ac1). Time at temperature depends on such factors as the complexity of the part, and enough time must be allowed to achieve the desired reduction in residual stress level. Following stress relief, the steel is cooled at a sufficiently slow rate to avoid formation or reintroduction of excessive thermal stresses. The stress relief process should be designed to reduce or eliminate internal stresses in a material without significantly altering its microstructure.
Stress relief helps improve a material’s stability, especially in applications where parts are subjected to cyclic or dynamic loading, since residual stresses can lead to fatigue failure over time. Stress relief helps to reduce these stresses, thus improving the material’s fatigue resistance and overall stability. During processes like welding, casting, or machining, the rapid cooling of steel can result in uneven contraction, leading to distortion in the final part. Stress relief helps reduce distortion, ensuring the part maintains its intended dimensions and shape.
Stress relief is particularly important after welding, which can introduce a significant amount of residual stress again resulting in distortion and/or cracking in service if not negated. Stress relief helps to minimize these effects and ensures the structural integrity of welded components.
How Do We Perform a Stress Relief Operation?
For carbon and alloy steels, stress relief operations are typically performed at 105°F–165°F (40°C–75°C) below the lower critical temperature, that is in the range of 930°F–1200°F (500°C–650°C). It is also important to understand the elimination of stress is not instantaneous, being a function of both temperature and time for maximum benefit. Typically, soak times of one hour per inch (25 mm) of maximum cross-sectional area (once the part has reached temperature) are recommended, with most soak times being in the range of 30 minutes to 2 hours, depending on the size and thickness of the part. Larger parts or components with complex geometries may require longer holding times to ensure uniform stress relief throughout the entire part. Alloy steels, especially if used in highstress environments (e.g., turbines, pressure vessels) benefit significantly from stress relief to improve their durability and fatigue resistance.
After removal from the furnace or oven, the parts rely on slow cooling to achieve a minimal residual stress state — the desired effect. Parts are typically still air cooled. Rapid cooling will only serve to reintroduce stress and is the most common mistake made in stress relief operations. A properly performed stress relief cycle often removes more than 90% of the internal stresses.
For tool steels the process is similar; it is common to perform a stress relief operation in the temperature ranges of 925°F–1025°F (500°C–550°C) for most tool steels or 1115°F–1300°F (600°C–700°C) for hot work and high-speed grades, allowing the parts to slowly cool to room temperature before subsequent operations. For stainless steels, the situation is more complex (see Atmosphere Heat Treatment, Volume 1 and ASM International’s Metals Handbook). Stress relief is done in the range of 550°F–800°F (290°C–425°C), which is below the sensitization range to avoid precipitation of carbides and reduced corrosion resistance. The operation depends on the form of the material, the operation being performed (e.g., machining), or if a completed assembly is to have a stress relief performed on it (Figure 2).
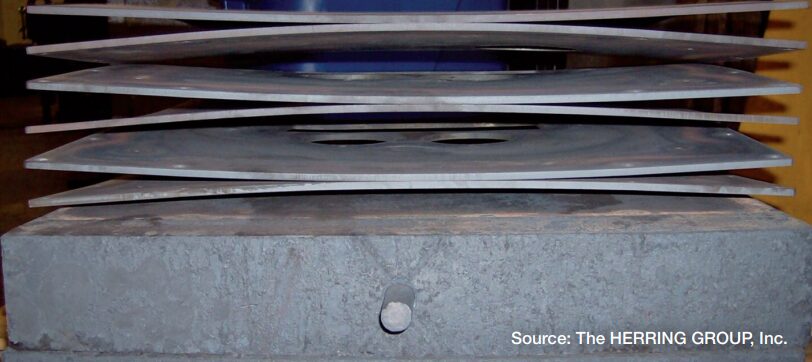
At stress relief temperature, atomic movement increases, allowing the material to “rearrange” its internal structure, thus effectively relieving internal stresses. Steel is usually held at the stress relief temperature to ensure the remaining stresses are evenly distributed and reduced.
How Slow Is Slow?
Once the desired stress relief temperature has been reached and the part held for the appropriate time, the steel is then cooled slowly, typically in air, to prevent reintroduction of new thermal stresses. Rapid cooling (such as quenching) is to be avoided. A “still air cool” is often recommended, being defined as cooling at a rate of 40°F (22°C) per minute or faster to 1100°F (593°C) and then at a rate of 15°F–25°F (8°C–14°C) per minute from 1100°F–300°F (593°C–150°C). Below 300°F (150°C), any cooling rate may be used.
Poor Man’s Stress Relief
In hardening, rapid cooling/quenching alone or in combination with pre-existing internal stresses can result in unwanted distortion and even brittle fracture near welds in certain grades of metal. Stress corrosion cracking is another concern. For these reasons, a number of heat treaters introduce a “stress relief hold” during hardening or case hardening treatments. This involves heating of a workload to an intermediate temperature, in the range of 1000°F–1300°F (538°C–705°C) and soaking for a period of time equivalent to one hour per inch of maximum cross-sectional area. The idea is to allow for stress relaxation so that more predictable dimensional change occurs on quenching.
Types of Stress Relief Operations
While the basic process parameters for stress relief are largely the same, various types of methods can be used to achieve the desired results. Depending on the size and type of components being treated, one can use:
- Batch furnaces where the load sits in the furnace or oven while being heated and soaked. This often allows precise control of these process variables. The load is then removed from the furnace for cooling.
- Continuous furnaces where large volumes of component parts are moved through a heated section (usually but not always with multiple control zones) and then conveyed into one or more cooling sections as parts move through the furnace. The cooling sections are typically 2–2½ times the length of the heated section for adequate cooling time.
- Induction heating for localized stress relief or when dealing with large or irregularly shaped components where heating the entire component part may not be desired. Stresses can be relieved in precise locations without affecting the entire part.
- Vibratory Stress Relief, which uses mechanical vibration to redistribute residual stresses without the need for high temperature treatments. This technique has been used on castings and in some cases large, welded structures. The amount of stress relieved is often significantly less than thermal methods.
- Post-Weld Heat Treatment (PWHT), often used during or after fabrication of welded steel structures. (Note: PWHT will be the subject of next month’s Ask The Heat Treat Doctor® column.)
In Summary
Stress relief is an oft-ignored but important heat treat process. By reducing internal stresses during manufacturing, stress relief operations help minimize post-heat treat distortion and improve mechanical properties. Understanding the significance of stress relief, selecting the best time/temperature cycles for a given material, and carefully controlling the process (especially as it relates to cooling rate) are keys to achieving the final result.
References
Accendo Reliability. “Residual Stresses in Metals.” Effective April 3, 2024. https://accendoreliability.com/residual-stresses-inmetals/. ASM International. “Metals Handbook, 10th ed., vol. 4, Heat Treating, Cleaning and Finishing.” (1991).
Grenier, Mario and Roger Gingras. “Rapid Tempering and Stress Relief Via High-Speed Convection Heating.” Industrial Heating, May 2003.
Haga, L. J., “Understanding Slow Cooling: Part 1 — Stress Relief.” Heat Treating, (October 1980).
Hebel, Thomas E. “Sub-harmonic Stress Relief Improves Mold Quality.” Mold Making Technology, 2009.
Herring, Daniel H. Atmosphere Heat Treatment, vol. I. BNP Media, 2014.
Herring, Daniel H. “Stress Relief.” Wire Forming Technology International (Summer 2010).
Lindqvist, Stefan and Jonas Holmgren. “Alternative Methods for Heat Stress Relief.” Master’s Thesis, Lulea University of Technology, 2007.
About the Author
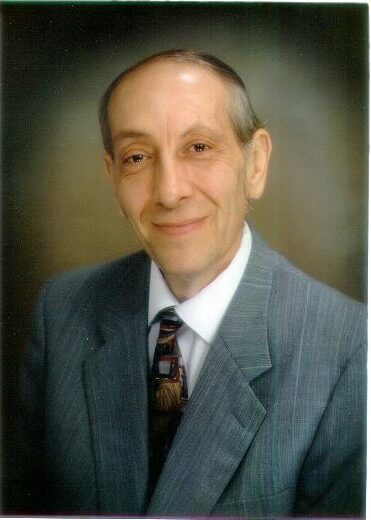
“The Heat Treat Doctor”
The HERRING GROUP, Inc.
Dan Herring has been in the industry for over 50 years and has gained vast experience in fields that include materials science, engineering, metallurgy, new product research, and many other areas. He is the author of six books and over 700 technical articles.
For more information: Contact Dan at dherring@heat-treat-doctor.com.
For more information about Dan’s books: see his page at the Heat Treat Store.