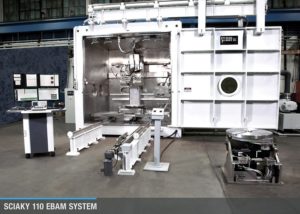
The goal of the R&D initiative between Sciaky, Inc., a subsidiary of Phillips Service Industries, Inc.; Aubert & Duval; and Airbus, and piloted by the Saint Exupéry Institute for Research in Technology (IRT) is to couple traditional metallurgy—high-power closed die forging—with emerging wire fed metal 3D printing techniques—in this case, Sciaky’s groundbreaking Electron Beam Additive Manufacturing (EBAM®) process—to develop new processes for manufacturing titanium alloys aircraft parts.
The Production Engineering laboratory of the National School of Engineering in Tarbes, France, will serve as an academic partner for this project, also known as the Metallic Advanced Materials for Aeronautics (MAMA) project.
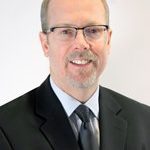
In this first phase, the project has global funding just under $4.8M (€ 4,2 M) of which 50% are supported by the French State as part of the “Investing in the Future” program (PIA – Programme Investissement d’Avenir), the other 50% being funded by its industrial partners.
“Sciaky is proud to work with the Saint Exupéry IRT, Aubert & Duval, and Airbus on this exciting project,” said Scott Phillips, president and CEO of Sciaky, Inc. “Industrial metal additive manufacturing technology continues to break new ground every day, and Sciaky is committed to keeping EBAM at the forefront of this movement.”