Building upon their collaboration begun last year, two aerospace titanium and alloy component suppliers recently concluded successful testing for optimizing alloy for performance.
Norsk Titanium (Norsk), which supplies aerospace-grade, additive manufactured, structural titanium components to Tier 1 client such as Boeing, partnered with QuesTek Innovations LLC and printed the additive manufacturer’s custom titanium wire in support of initial material properties testing.
Norsk’s patented Rapid Plasma Deposition™ (RPD™ ) process, which transforms titanium wire into complex components suitable for structural and safety-critical applications, is used in the aerospace industry. QuesTek, utilizing Integrated Computational Materials Engineering (ICME), has been involved in projects to resolve materials issues across various alloy systems in additive manufacturing (Al, Mg, Cu, Fe, Co, Ni and Ti) to improve component performance by modifying chemical compositions and optimizing the heat treatments, or designing entirely new alloys.
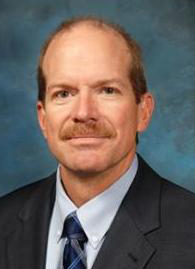
“QuesTek’s high-performance titanium alloy provides an opportunity for Norsk’s customers to optimize components printed with Norsk Titanium’s RPD™ process and opens doors for new applications,” said Norsk Chief Technology Officer Carl Johnson.
Norsk and QuesTek plan to perform additional testing, while working with aircraft and propulsion manufacturers on the improved business case the new alloy affords.
(Photo Credit: Handout/Rueters)